Специально для портала «Перспективы»
Владимир Кондратьев
Кондратьев Владимир Борисович – руководитель Центра промышленных и инвестиционных исследований ИМЭМО РАН, профессор, доктор экономических наук.
Очередная статья из цикла материалов о состоянии отдельных секторов экономики в России и мире посвящена цементной индустрии. Хотя эта отрасль реже попадает в фокус внимания, чем, к примеру, энергетика, металлургия, машиностроение или агробизнес, ее экономическое значение больше, чем может показаться непрофессионалам. Цемент и бетон являются самым употребляемым после воды ресурсом на земле. А темпы развития цементной промышленности в 1,5-2 раза превышают темпы роста мирового ВВП.
Цемент вместе с бетоном является вторым после воды наиболее употребляемым ресурсом на земле: ежегодно его потребление на нашей планете составляет около 1 тонны на человека. Цемент производится в 156 странах мира. Однако 70% мирового производства цемента сосредоточено лишь в 10 странах мира, где проживает 70% населения земли. Цементная промышленность имеет ключевое значение для экономического развития, поскольку производит основной вид строительных материалов для жилищного, промышленного строительства и для строительства объектов инфраструктуры. Темпы ее развития в 1,5-2 раза выше, чем темпы роста мирового ВВП.
Цемент - один из базовых строительных материалов, который называют "хлебом строительства". Являясь основным вяжущим компонентом, цемент находит широкое применение в производстве бетона, железобетона, строительных растворов, а также в асбестоцементной, нефтедобывающей и других отраслях промышленности. Он пользуется спросом при возведении новых промышленных объектов, реконструкции и строительстве зданий и сооружений, в том числе гидротехнических объектов, индивидуальном строительстве. Уникальные свойства цемента позволяют на его основе изготавливать специальные конструкции, такие как железнодорожные шпалы, строительные блоки, панели и плитки, многие другие изделия.
Цементная промышленность – одна из ведущих отраслей производства строительных материалов. Выпускаются различные виды цемента: портландцемент, шлакопортландцемент, пуццолановый портландцемент, специальные цементы (декоративные, тампонажный, глинозёмистый, сульфатостойкий, цемент для гидротехнических сооружений, быстротвердеющий цемент и др.).
В последние несколько лет как в производстве, так и потреблении цемента существенно вырос удельный вес развивающихся стран. Их доля в мировом потреблении цемента к 2010 г. достигла 90% . Этому способствовали благоприятная демография, растущая урбанизация населения, все возрастающий спрос на жилье и объекты инфраструктуры. Первое место принадлежит Китаю: в 2012 г., согласно оценкам, на эту страну будет приходиться почти 60% мирового потребления цемента (в 1990 г. она потребляла только 18%) (рис. 1, 2).
Рис. 1.
Структура спроса на цемент по регионам мира в 1990 г., %
1 – Индия; 2 – Северная Америка; 3 – Китай; 4 – Западная Европа; 5 – остальные страны.
Рассчитано по :
Рис. 2.
Структура спроса на цемент по регионам в 2012 г.
1 – Северная Америка; 2 – Западная Европа; 3 – Индия; 4 – остальные страны; 5 – Китай.
Рассчитано по : Cementing growth. Ernst & Young, 2011.
В последние 20 лет произошла существенная трансформация и самой цементной промышленности. Она стала по-настоящему глобальной. На этом рынке появилось несколько транснациональных корпораций. На семь крупнейших глобальных цементных корпораций в 2010 г. приходилось примерно 30% мирового производства цемента. Эти компании активно перемещали свои мощности и строили новые заводы в развивающихся странах, где наблюдались самые высокие темпы спроса на строительные материалы (табл. 1).
Таблица 1. Доля развивающихся стран в совокупных мощностях ведущих цементных компаний мира, %
Компании |
2001 г . |
2010 г . |
Heidelberg cement | ||
Источник: Davy research , RBS research , данные корпоративной статистики.
Так, за период с 2001 по 2010 г. доля развивающихся рынков в общих цементных мощностях швейцарской компании Holcim выросла с 53 до 67%, а французской Lafarge – с 59 до 71%.
Ежегодно в мире производится свыше 3 млрд т цемента. При этом за последние 11 лет выпуск цемента год от года возрастал. С 2000 г. по 2011 г. объемы производства выросли более чем в 2 раза, с 1,6 млрд т до 3,6 млрд т (табл. 2).
Таблица 2. Динамика мирового производства цемента и темпы прироста в 2000-2011 гг.
Рассчитано по : US Geological Survey, Mineral Commodity Summary, January 2012.
Наиболее высокие темпы роста производства (108– 110% к уровню предыдущего года) наблюдались в 2003– 2007 гг. в условиях строительного бума – в строительстве потребляется более 80% цемента. В 2008 г. в связи с началом мирового экономического кризиса темпы роста выпуска цемента снизились до 102,5%. Однако уже в 2009 г. в мире было выпущено свыше 3 млрд т цемента, что на 7,7% выше уровня предыдущего года. В 2010 г. объем выпуска достиг 3,3 млрд т (+7,8%), а в 2011 г. – 3,6 млрд т.
Более половины этого объема в 2010 г. приходилось на предприятия азиатских стран. В первую очередь это Китай (53%) и Индия (6%). Вклад государств Западной Европы составляет около 9%, США – 2,7%, Бразилии – 1,7% (рис. 3). Доля стран СНГ не превышает 2,5% мирового производства (в том числе России – 1,4 %).
Рис. 3.
Страновая структура мирового производства цемента в 2010 г., %
1 – Китай, 2 – Западная Европа, 3 – Индия, 4 – США, 5 – Бразилия, 6 – Россия, 7 – прочие производители.
Источник : U.S. Geological Survey, Mineral Commodity Summaries, January 2011.
Обращает на себя внимание, что один только Китай производит теперь больше цемента, чем все остальные страны мира вместе взятые. За пять лет, с 2005 по 2010 г., производство в этой стране практически удвоилось. Высокими темпами росло производство цемента в Бразилии, Турции и Вьетнаме. В Западной Европе и России это производство стагнировало. В результате в 2010 г. по сравнению с 2005 г. Бразилия переместилась в списке мировых производителей цемента с 13-го места на 5-е, Турция – с 10-го на 4-е, а Вьетнам – с 17-го на 9-е (табл. 3).
Доля Китая в общемировом производстве цемента имеет тенденцию к росту. Так, в 2000 г. этот показатель составлял лишь 36,4%, в 2006 г. превысил 47%, а в 2010 г. достиг почти 53%. При этом произошло снижение доли США с 5% в 2000 г. до 4% в 2005 г. и 2,7% в 2010 г., а доля Японии снизилась с 3% в 2005 г. до 1,6% в 2010 г.
Таблица 3. Производство цемента в ведущих странах мира, млн т
Источник : U.S. Geological Survey, Mineral Commodity Summaries, January 2011.
Потребность в цементе в значительной степени определяется ростом промышленного производства и инвестиционной активностью в стране или регионе. Объемы производства (потребления) цемента наглядно показывают, где в настоящее время идет бурное строительство, – это Китай, а также страны Юго-Восточной и Центральной Азии.
В будущем (до 2020 г.) ожидается расширение мирового спроса на цемент: в частности, в странах Юго-Восточной Азии – на 90%, Юго-Западной Азии – на 70%. Выше среднего ожидается рост потребления в других частях Азии, Африке и Латинской Америке, в то время как в США прогнозируется снижение спроса на 4–6%.
Ежегодный прирост объема внутреннего рынка Китая, в связи с ожидаемыми высокими темпами роста экономики страны, оценивается на уровне 8%. Это сохранит за КНР статус крупнейшего и наиболее перспективного рынка цемента. В странах ЕС рост спроса на цемент будет ниже среднемирового уровня.
В настоящее время на мировом рынке цемента доминирует ряд крупных компаний: Lafarge (Франция), Holcim (Швейцария), HeidelbergCement (Германия), Italcementi (Италия), Cemex (Мексика,), Anhui Conch Cement (Китай), Taiheiyo (Япония). На их долю приходится свыше 1/3 совокупного мирового производства цемента и 2/3 его продаж (табл. 4).
Таблица 4. Крупнейшие цементные компании мира
|
Компания |
Производство, млн т |
Общая мощность заводов, млн т |
Численность занятых, тыс. чел. |
Объем продаж, млрд долл. |
Число заводов |
Число стран |
|
Holcim (Швейцария) | ||||||||
Lafarge (Франция) | ||||||||
Hiedelberg Cement (Германия) | ||||||||
Cemex (Мексика) | ||||||||
Italocementi Group (Италия) | ||||||||
Buzzi Unicem (Италия) | ||||||||
Cimpor (Португалия) | ||||||||
Taiheiyo Cement (Япония) | ||||||||
Евроцемент груп (Россия) |
Рассчитано по данным корпоративной статистики.
Среди лидеров по производству цемента можно выделить швейцарскую компанию Holcim, основанную еще в 1912 г., которой принадлежит 140 цементных заводов в 70 странах мира. Производственные мощности компании по итогам 2010 г. составили 211,5 млн т цемента, объем производства – 136,7 млн т, уровень загрузки мощностей – 65%. Численность занятых составляла на 2010 г. более 80 тыс. чел. Эта компания активно присутствует в Индии и других странах Азии, на которые приходится 26% всех ее мощностей.
Другой крупнейшей транснациональной цементной корпорацией является французская Lafarge, владеющая 160 цементными заводами в 50 странах мира. Это одна из старейших компаний, она была основана еще в 1833 г. Производственные мощности по итогам 2010 г. составили 217 млн т цемента, объем производства – 135,7 млн т, уровень загрузки – 63%. Lafarge также активно работает в Азии (28% всех мощностей), при этом акцент делается на Китай, где сосредоточено более половины всех азиатских заводов компании.
Для еще одного лидера, немецкой компании Heidelberg Cement, основанной в 1874 г., характерны следующие показатели: производственная мощность по итогам 2010 г. – 116,5 млн т цемента, объем производства – 78,7 млн т, уровень загрузки мощностей – 68%. Значительная часть мощностей (почти 30%) приходится на страны Северной Америки.
Таким образом, общий объем производства трех крупнейших компаний в 2010 г. составил почти 11% мирового производства цемента.
Развивающиеся страны в списке мировых лидеров цементной промышленности представлены лишь одной мексиканской компанией Cemeх, которая существует с 1902 г. В настоящее время это четвертая по объемам производства цемента корпорация в мире. В 2010 г. она выпустила 74 млн т цемента на 66 заводах в 50 странах мира.
В 2010 г. средний уровень рентабельности среди производителей цемента на развитых рынках составил 18%, при этом за последние четыре года данный показатель снизился на 5-6 процентных пунктов. На российском рынке рентабельность в среднем находится в пределах 10%. Разница в рентабельности объясняется различными технологиями производства и уровнем износа цементных заводов (рис. 4).
Рис. 4.
Уровень рентабельности крупнейших производителей цемента в 2010 г., %
Рассчитано по данным корпоративной отчетности: Российская индустрия цемента; Новая волна спроса; ТКБ Капитал, 2011.
В последние годы заметно растет международная торговля цементом. Однако доля экспортно-импортных операций в общих объемах производства цемента все еще незначительна и составляет от 5 до 7%. Это означает, что производство этого строительного материала существует прежде всего для удовлетворения внутренних локальных потребностей. Среди стран-экспортеров цемента первое место (с большим отрывом от других) занимает Китай (табл. 5), что не удивительно, принимая во внимание долю этой страны в мировом производстве.
Таблица 5. Ведущие страны-экспортеры цемента, 2010 г.
Источник: UN Comtrade 2010 .
Интересно отметить, что больше половины стран-экспортеров, представленных в таблице, не являются ведущими производителями цемента. Например, США, Россия и Испания, являясь ключевыми производителями, не попадают в десятку главных экспортеров. Это объясняется тем, что многие ведущие производители используют этот строительный материал на своем растущем внутреннем рынке. Примечательно и то, что среди 10 ключевых стран-экспортеров 7 представляют азиатский континент. Это свидетельствует о значительных конкурентных преимуществах азиатских стран в производстве строительных материалов.
Доля экспортных поставок цемента от общего объема производства составляет: в Китае – 2,7%, в Индии – 3%, в Турции – 8%, в Японии – 14%. Ведущие производители цемента не всегда обладают излишками этого материала для экспорта. А страны-экспортеры, имеющие излишки, пользуются конкурентными преимуществами, связанными с более низкими издержками добычи необходимого для производства цемента сырья .
Статистические данные свидетельствуют, что крупнейшим импортером цемента в мире являются США (табл. 6).
Таблица 6. Ведущие страны-импортеры цемента, 2010 г.
Источник: UN Comtrade 2010 .
Первые пять стран, потребляющие около 55% всего импортируемого в мире цемента, расположены в Западной Европе и Северной Америке. Анализ страновой структуры экспорта и импорта позволяет сделать вывод, что ведущими производителями цемента являются, как правило, развивающиеся, а его потребителями – развитые страны. Единственным исключением оказывается Южная Корея, которая присутствует в обоих списках.
Выявленные тенденции объясняются, в частности, жестким экологическим регулированием в развитых странах, заставляющим переводить производственные цементные мощности в страны третьего мира, где издержки производства ниже, а экологические требования гораздо мягче.
Цементная промышленность России постепенно восстанавливается после кризиса 2009 г. Сокращение спроса было вызвано снижением строительной активности в стране вследствие остановки многих инфраструктурных проектов из-за кризиса ликвидности. В 2010 г. спрос на цемент вырос на 14% после падения на 27% в 2009 г. Потребление достигло 51,5 млн т (в 2009 г. – 45,2 млн т). В ближайшей перспективе можно ждать роста спроса примерно на 8–10% в год благодаря осуществлению крупных инфраструктурных проектов, связанных, в том числе, с проведением Олимпиады в Сочи и саммита АТЭС на Дальнем Востоке. Долгосрочные планы государства включают расходы на экономическое развитие страны в объемах до 1 трлн долл. к 2020 г. и 400 млрд долл. инвестиций в инфраструктуру страны к 2015 г. Тем не менее в стране остро ощущается потребность в модернизации и замене около 70% устаревших цементных мощностей. Прирост мощностей может не поспеть за динамикой спроса на цемент, что приведет к росту объемов импорта этого строительного материала.
Производители цемента в России также продемонстрировали в 2010 г. позитивную динамику, показав 13,9% рост (производство достигло 50,4 млн т). Положительная динамика сохранилась и в 2011 г. По предварительным оценкам, общий объем производства цемента в 2012 г. составит 56,2 млн т. Среднегодовой рост производства цемента за период 2011– 2015 гг., по нашим оценкам, составит 8,2% (табл. 7).
Таблица 7. Динамика производства цемента в России, млн т
* Прогноз.
Источник: СМПРО, оценка ТКБ Капитал.
Основными факторами роста цементной промышленности в России остаются жилищное строительство и инфраструктура. Развитие отрасли в большой степени зависит от темпов роста жилищного строительства. По мнению экспертов, на фоне крайне низкой обеспеченности жильем его строительство в среднесрочной перспективе будет активно наращивать обороты.
Согласно статистике, пик рождаемости в России пришелся на 1980– 1987 гг. Сейчас это экономически активная часть населения, которая нуждается в улучшении жилищных условий. Покупки жилья продолжаются даже несмотря на рост цен, что подтверждают тенденции 2007– 2008 гг. На этом фоне цементная отрасль обладает хорошими перспективами роста в ближайшие годы. За 2005– 2011 гг. ввод жилья в России увеличился с 42 млн до 59 млн кв. м и к 2015 г., по прогнозам, может возрасти до 80 млн кв. м. Среднегодовые темпы роста жилищного строительства в 2011– 2015 гг. оцениваются в 6,8%.
Возросшая строительная активность повысила спрос на цемент и привела к росту его стоимости. При текущих ценах на газ и электроэнергию уровень рентабельности многих цементных компаний балансирует на грани убытков. Поэтому вероятно, что при сохранении текущего спроса компании будут вынуждены повышать цены. По нашим оценкам, средняя цена на цемент у производителей по итогам 2011 г. выросла на 15% – до 2500 руб. за тонну, а в 2012 г. вырастет еще на 9% – до 2700 руб. за тонну. Для сравнения, в 2005 г. средняя цена цемента в России была на уровне 2000 руб. за тонну .
Цемент может перевозиться любыми видами транспорта. В связи с несовершенством автомобильных дорог в России для этого используется в основном железнодорожный транспорт, на его долю приходится до 85% всех перевозок цемента. Остальная часть перевозится автомобильным транспортом. По нашим оценкам, расходы на транспортировку цемента за последний год увеличивали его продажную стоимость в среднем на 18%. Так, в мае 2010 г. стоимость тонны цемента у производителей составляла 2020 руб., при этом рыночная цена с учетом доставки достигала 2480 руб. В мае 2011 г. тонна цемента у производителей стоила 2340 руб., а рыночная цена с учетом доставки достигла 2830 руб.
В 2011–2012 гг. объем ввода новых мощностей по производству цемента в России оценивается на уровне 25 млн т. За следующие пять лет производственные мощности могут вырасти на 16%. Несмотря на кризис 2008–2009 гг., строительство и модернизация цементного производства продолжаются. Так, в 2010 г. в эксплуатацию были запущены два новых цементных завода общей производственной мощностью 3,2 млн т, а также расширены на 3,5 млн т мощности двух существующих. Кроме того, до 2015 г. планируется запустить еще 14 заводов общей мощностью 24,8 млн т. По нашим оценкам, в период с 2011 по 2015 г. производственные мощности в России с учетом амортизации увеличатся на 16%, до 97,3 млн т цемента в год. Согласно рыночным данным, стоимость строительства цементного завода мощностью 1 млн т в год оценивается в 300 млн долл. Средний срок строительства такого завода составляет два года.
Крупнейшие мощности по производству цемента располагаются в центральной части России. Близость к столице обеспечивает стабильный спрос. В ближайшие два-три года Южный федеральный округ может приблизиться к показателям Центрального округа. Спрос на цемент со стороны компаний, расположенных в данном регионе, обеспечивает близость к проектам Олимпиады 2014 г. в Сочи. За последние три года доля Южного федерального округа в объеме производства цемента в России выросла на 3 процентных пункта, до 19,5%. Сейчас в Краснодарском крае строятся цементные заводы общей мощностью 4,5 млн т, в стадии планирования мощности еще на 5,6 млн т. В случае запуска всех проектов общая производственная мощность региона составит 14,7 млн т (рис. 5).
Рис. 5.
Структура производства цемента по регионам России в 2010 г., %
1 – Дальневосточный; 2 – Северо-Западный; 3 – Уральский; 4 – Северный; 5 – Южный; 6 – Приволжский; 7 – Центральный.
Рассчитано по данным Росстата.
Доля импорта в объеме потребления цемента в России оценивается в пределах 3,1%.По нашим оценкам, существующая транспортная инфраструктура позволяет принимать до 10 млн т импортного цемента в год. Свои возможности рынок продемонстрировал в 2008 г. – импорт цемента вырос в 2,5 раза, до 8,4 млн т. Отмена 5%-й импортной пошлины и более чем двукратный рост цен на цемент позволяли странам-импортерам получать прибыль даже с учетом расходов на транспортировку. В октябре 2008 г., когда пошлина была восстановлена, объем импортного цемента резко снизился (до 1,8–1,9 млн т в год), из чего можно сделать вывод, что при использованиями российскими компаниями импортного цемента грань между прибылью и убытком была достаточно тонкой. Сейчас цены на 40% ниже пиковых значений середины 2008 г., поэтому даже в случае отмены пошлины на ввоз цемента импорт его в Россию будет нерентабелен. По нашим прогнозам, доля импортного цемента в общем объеме потребления в 2011–2015 гг. составит в среднем не более 3,1%.
Абсолютным лидером по производству цемента в России является компания «Евроцемент». В 2010 г. она произвела 19,4 млн т цемента, заняв 38,5% российского рынка. Второе место досталось «Новоросцементу»: несмотря на меньшую по сравнению с «Сибирским цементом» производственную мощность (4,1 млн т против 5,5 млн т), удачное расположение вблизи строительства олимпийских объектов позволило компании произвести и реализовать 3,8 млн т при 93% загрузке мощностей (табл. 8).
Таблица 8. Крупнейшие производители цемента в России, 2010 г.
Компания |
Мощность заводов, млн т |
Производство, млн т |
Доля рынка, % |
Евроцемент груп | |||
Сибирский цемент | |||
Мордовцемент | |||
Новоросцемент | |||
Holcim/Альфа-цемент | |||
Dyckerhoff AG/Сухоложскцемент | |||
Серебряковцемент | |||
Горнозаводскцемент | |||
Искитимцемент | |||
ИТОГО |
|
||
|
|
||
|
|
Цементная промышленность является составной частью тяжелой промышленности и определяет потенциал любого государства. Отрасль является основным поставщиком сырья для производства бетона и железобетона (свыше половины производимого цемента), который в свою очередь выступает основным конструкционным материалом в строительстве. Другими словами, это сектор, спрос, на продукцию которого прямо зависит от объемов жилищного и промышленного строительства.
Цементная промышленность имеет две основные отличительные особенности. Первая - производство цемента чрезвычайно энергоемко. Доля энергоресурсов, а также топлива превышает половину себестоимости. Это делает ее очень чувствительной к колебаниям стоимости энергоресурсов и различных видов топлива. Цемент является ключевым элементом в производстве основного строительного материала - железобетона, и, соответственно, цементная промышленность в экономике играет роль одного из каналов трансляции инфляции издержек на всю экономику. Доля затрат на топливно-энергетические ресурсы в себестоимости зависит от технологии производства.
Влияние стоимости энергоресурсов на цементную промышленность очень велико. Низкая стоимость газа на внутреннем рынке вкупе с постоянно растущей стоимостью электроэнергии делают экономически невыгодным переход на более передовое производство сухим способом, к тому же изначально большинство цементных заводов сориентировано на мокрую технологию (по ней производится чуть менее 90% цемента). Впрочем, ситуация меняется по мере увеличения стоимости газа. Однако вопрос энергоемкости на фоне постоянного роста энерготарифа пока открыт.
Другая важная особенность отрасли - то, что при перевозках на дальние расстояния доля тарифа на грузоперевозки в стоимости для потребителя может достигать половины себестоимости продукта. Это резко усиливает локализацию рынка в рамках отдельных региональных сегментов. В основном же перевозки внутри региона имеют смысл только при существенном недостатке мощностей по производству цемента либо возможности существенно сэкономить на железнодорожном тарифе.
Цементная промышленность является одной из старейших отраслей нашей страны. Первый цементный завод был построен в 1839 г. в Петербурге, затем были построены заводы под Москвой и в Прибалтике. В 1900 г. в России уже насчитывалось около 50-ти цементных заводов. В годы первой мировой войны производство цемента резко упало и составило всего 36 тыс. тонн. Общая мощность цементных заводов к концу 1940 г. возросла по сравнению с 1928 г. в три раза и составила 5675 тыс. тонн. Дальнейший рост производства был прерван Великой Отечественной войной. К маю 1945 г. были частично восстановлены 11 заводов, а в 1948 г. удалось произвести довоенный уровень производства цемента. В 1953 г. было выпущено цемента в три раза больше, чем в 1940 г. По объему производства СССР вышел на первое место в мире, а в 1966 г. перегнал США по производству цемента на душу населения.
Рекордные объемы производства цемента были отмечены в России в 1990 г., когда было выпущено 83 млн. т. цемента. Затем последовал затяжной спад. В 1998 г. выпуск этого вида строительных материалов снизился до 25,9 млн. т. Таким образом, начавшийся в 1999 г. устойчивый рост производства цемента продолжается. В среднегодовом исчислении он составил за этот период 10%.
В настоящее время в цементной промышленности России действует 50 заводов с проектной мощностью 69,2 млн. т. и фактической - 62,3 млн. т. На предприятиях высокий износ оборудования - в среднем по отрасли - 70%. Для обеспечения выполнения национальной программы по строительству доступного жилья, по расчетам специалистов, необходимы инвестиции в размере 5,1-6,3 млрд. долл. Эти средства должны быть направлены на поддержание и модернизацию действующих мощностей и строительство новых цементных заводов. Непринятие срочных мер может привести к дефициту цемента в 2010 г. в объеме, превышающем 20 млн. т.
Оценивая состояние цементной промышленности России, следует отметить следующее. Отрасль в целом прошла стадию экономического спада и в настоящее время находится в состоянии подъема. Большая часть цементных предприятий России стала собственностью крупных корпораций, в том числе иностранных.
Основными направлениями развития цементной промышленности России являются:
техническое перевооружение и реконструкция заводов с целью обновления основных фондов и доведение доли сухого способа производства цемента до 80-85%;
обеспечение широкого вовлечения в хозяйственный оборот отходов производства смежных отраслей промышленности;
подготовка и повышение квалификации специалистов цементной промышленности;
уменьшение вредных выбросов в атмосферу и улучшение условий труда;
подготовка цементных предприятий к переходу на использование в качестве технологического топлива угля и горючих отходов промышленности;
переоснащение машиностроительной базы страны и организация производства цементного оборудования нового поколения.
Таким образом, цементную отрасль сегодня можно отнести к разряду стабильно развивающихся.
1.2 Характеристика рынков
Анализ структуры потребления в разрезе федеральных округов показывает, что региональная сегментация российского рынка цемента в целом совпадает с размещением основных его производств. Одна из причин этого - экономическая нецелесообразность продажи цемента с транспортировкой на расстоянии более 1000 км. Регионом с наиболее емким рынком является центральный федеральный округ, где сконцентрировано 36,1% внутреннего потребления цемента. За ним с существенным отставанием располагается Приволжский (18,3%), Южный округ (15%), Уральский (11,3%), Северо-Западный (7,0%), Сибирский (9,5%) и Дальневосточный (2,8%).
Следует отметить, что внутри округов области также сильно дифференцируемы по объемам потребления. Поэтому при рассмотрении региональных рынков целесообразно учитывать и деление по областному признаку, так как в основе выделения области учтены, экономические, географические и производственные, организационные и другие факторы.
Наиболее перспективными с точки зрения объемов потребления цемента являются Московский регион (22,7% общероссийского рынка), Краснодарский край (5,6%) и Свердловская область (5,2%). Среди других территорий весьма развитые региональные рынки имеют Татарстан, Тюменская и Челябинские области, а также Башкортостан (таблица 1.1). В целом на долю 10 регионов с максимальными объемами потребления цемента приходится более половины внутреннего рынка.
Таблица 1.1
Региональная структура потребления цемента в России,%.
Наименование региона |
Доля региона |
Московский регион (Москва и обл) | |
Краснодарский край | |
Свердловская область | |
Республика Татарстан | |
Тюменская область | |
Челябинская область | |
г. Санкт-Петербург | |
Республика Башкортостан | |
Новосибирская область | |
Волгоградская область | |
Из 11 экономических районов, производящих цемент, в 4 районах - Волго-Вятском, Центрально-Черноземном, Поволжском и Уральском - его производство превышает потребление. В Центральном, Западно-Сибирском, Северо-Кавказском, Северо-3ападном, Северном, Восточно-Сибирском и Дальневосточном потребление цемента, напротив, превышает его выпуск. При этом следует отметить, что имеющиеся мощности по производству цемента на ряде предприятий всех упомянутых экономических районов используются лишь на 30-50%.
Основные страны-покупатели российского цемента и клинкера - Испания, Китай, Украина, Казахстан, Венгрия, Финляндия, страны Ближнего Востока, Алжир, Азербайджан, Польша, Турция, Эстония, КНДР, Монголия.
Основные страны поставщики цемента в Россию - Белоруссия, Литва, Казахстан, Германия, Бельгия, Дания, Италия, Республика Корея, Словакия, Франция.
Объем производства цемента определяется следующими факторами: объем экспорта цемента; состояние производственных мощностей; уровень спроса на цемент на внутреннем рынке; возможность экспорта.
Основная доля в потреблении цемента в России приходится на портландцемент. По оценке, его удельный вес на рынке составляет не менее 92%, тогда как оптимальную часть занимает шлакопортландцемент и, в значительно меньших объемах, другие разновидности цемента.
В видовой структуре потребления портландцемента преобладают сорта, содержащие минеральные добавки. На их долю приходится почти половина портландцемента, используемого в России. Весьма значителен сегмент продукции, не содержащий минеральных компонентов. Его удельный вес превышает 38% суммарного объема потребления. Из специальных видов цементов наибольшим спросом пользуется сульфатостойкий цемент. Рынок других видов продукции пока еще остается крайне узким: так, например, цемент с пластифицирующей добавкой занимает лишь 0,1% общего объема применения, а быстродействующие сорта - около 0,5%.
Структура потребления по основным видам портландцементов в 2005 г. с минеральными добавками 47,0%, без добавок 38,5%, прочие 8,3%, 6,2% - сульфатостойкий.
В марочном ассортименте лидирует потребление цемента марок 400 и 500. На их долю приходится соответственно 66,2% и 32,6% общего объема рынка. Следует отметить, что с этой точки зрения в структуре потребления цемента произошли качественные изменения, в бывшем СССР потребители в силу дефицита качественной продукции были вынуждены использовать цементы более низких марок. Так, в конце 80-х г. г. сегмент цемента марки 300 составил более 10%, тогда как в настоящее время он сузился до 0,4%. Явный прогресс достигнут и в потреблении цемента марки 500, удельный вес которой в общем объеме используемого цемента возрос за последние годы (табл.1.2).
Таблица 1.2
Структура потребления цемента по основным маркам в России и в бывшем СССР.
2004-2005 гг. | |||||
Середина 80-х гг. |
Основными потребителями цемента являются предприятия по изготовлению железобетонных изделий и конструкций. Примерно одинаково оцениваются доли изготовителей асбестоцементных изделий и строительно-монтажных организаций.
Структура рынка цемента по основным группам потребителей в России представлена на рис.1.1:
производство ЖБИ - 53%;
проведение СМР - 21%;
производство АЦИ - 20%;
население
- 6%.
Рис.1.1 Структура рынка цемента по основным группам потребителей в России
Производство и продажа цемента в настоящее время в России, в связи с прекращением крупного промышленного строительства, стали сезонными. Причем "пик" потребления и производства на абсолютном числе предприятий приходится на III квартал года. Наиболее низкий уровень продаж и производства приходится на I квартал года. Это ставит перед цементными предприятиями задачи изменения организации производства и труда, переоснащения основного и вспомогательного оборудования, изменения системы его ремонтов, создания резервных мощностей по упаковке цемента и другие.
Следовательно, одним из главных вопросов для цементного рынка и его потребителей являются цены, которые повышаются раз в год ближе к лету, когда спрос на этот вид строительных материалов многократно возрастает. Но причины увеличения цен не только в этом. Главные из них - рост инфляции и увеличение тарифов естественных монополий, составляющих значительную долю в себестоимости продукции цементных заводов.
Несмотря на постоянно опережающий рост цен на топливно-энергетические ресурсы (131,5%), тарифов за перевозки (138,6%) и другие услуги транспортных, ремонтных и других организаций и, в связи с этим, увеличение эксплуатационных затрат и себестоимости цемента, индекс цен на цемент в среднем по цементной промышленности России равен 1,28.
Цель работы: определить и проанализировать текущие . Для анализа использованы агрегированные данные статистической отчетности крупных и средних предприятий (П-1, П-2, источник: Росстат), данные по внешнеэкономической деятельности (). Использованы агрегированные данные по виду деятельности «Производство цемента» (код ОКВЭД 2007 года 26.51, код ОКВЭД 2014 года 23.51).
Краткое описание отрасли. Основные компании-участники.
Цементная промышленность является одной из старейших в России, первый завод по производству портландцемента был построен еще в 1839 году. В настоящее время цемент и изготовляемые из него бетон и железобетон являются основными строительными материалами, которые используются в самых разнообразных областях строительства. При этом цемент остается относительно простым, универсальным и дешевым материалом, для изготовления которого требуются довольно доступное сырье - известняк, мергель, глины, мел, гипс, а также вода.
В настоящее время существуют следующие основные способы производства цемента: мокрый, сухой, комбинированный, а также их вариации. Преимуществом сухого метода производства по сравнению с мокрым является более высокий съем клинкера с 1 кв. метра печного агрегата, а также более низкий расход топлива. Так, производство портландцементного клинкера сухим способом требует в два раза меньше расхода топлива, чем мокрым. Глобальными тенденциями в производственном процессе цементных заводов являются отказ от мокрого способа производства и постепенный переход на сухой.
Основными факторами размещения предприятий цементной промышленности являются потребительский и сырьевой. Первый выражается в концентрации производства вблизи потенциальных потребителей - крупнейших городов и промышленных центров. Второй обусловлен наличием доступной и недорогой сырьевой базы.
На сегодняшний день в России насчитывается 58 цементных заводов с суммарной производственной мощностью порядка 106 млн. тонн цемента в год (Для получения детального анализа отрасли производств цемента, можно обратиться к сотрудикам — ). Производителей цемента на российском рынке условно можно разделить на три группы: российские холдинги, объединяющие несколько заводов; российские заводы, не входящие в состав промышленных групп; зарубежные холдинги, осуществляющие свою деятельность на территории России.
К крупнейшим российским холдингам относятся , «Сибирский цемент»; ведущие зарубежные производители представлены на российском рынке компаниями LafargeHolcim, Heidelberg. Российские заводы, не входящие в состав промышленных групп, выпускают, как правило, небольшие объемы цементной продукции.
Крупнейшим производителем цемента в России является АО «Евроцемент Груп», которое представляет собой международный вертикально интегрированный промышленный холдинг по производству строительных материалов и объединяет 19 цементных заводов, 16 из которых расположены в России, остальные - в Украине и Узбекистане. Суммарная производственная мощность российских цементных заводов, входящих в состав АО «Евроцемент груп», составляет свыше 50 млн. тонн цемента в год. Также в состав холдинга входят заводы по производству бетона, ЖБИ, холдинг располагает богатейшей сырьевой базой — запасы нерудных материалов составляют более 5,5 млрд. тонн. По данным союза производителей цемента, на долю заводов АО «Евроцемент Груп» пришлось около 30% произведенного в 2016 году цемента.
Табл. 1. Цементные заводы, входящие в состав АО «Евроцемент груп»
Название | Регион | Производственная мощность, млн. тонн |
«Белгородский цемент», ЗАО | Белгородская область | 4,1 |
Воронежский филиал, АО «Евроцемент груп» | Воронежская область | 3,1 |
«Жигулевские стройматериалы», ЗАО | Самарская область | 2,0 |
«Кавказцемент», АО | Карачаево-Черкесская республика | 3,4 |
«Катавский цемент», АО | Челябинская область | 1,8 |
«Липецкцемент», АО | Липецкая область | 2,3 |
«Мальцовский портландцемент», АО | Брянская область | 4,7 |
«Михайловцемент», АО | Рязанская область | 2,2 |
«Мордовцемент», ПАО | Мордовия, республика | 10,6 |
«Невьянский цементник», АО | Свердловская область | 1,3 |
«Осколцемент», ЗАО | Белгородская область | 4,5 |
«Петербургцемент», ООО | Ленинградская область | 2,6 |
«Пикалевский цемент», АО | Ленинградская область | 2,6 |
«Савинский цементный завод», ЗАО | Архангельская область | 1,4 |
«Сенгилеевский цементный завод», ООО | Ульяновская область | 2,4 |
«Ульяновскцемент», АО | Ульяновская область | 2,7 |
Второй по величине представитель российской цементной промышленности - ОАО «Новоросцемент» — старейшее цементное предприятие, в текущем 2017-ом году, отмечающее свой 135-летний юбилей. В структуре ОАО «Новоросцемента» 3 цементных завода суммарной производственной мощностью 5,7 млн. тонн цемента.
Еще один крупный игрок российского цементного рынка - АО ХК «Сибирский цемент» включает в себя 3 цементных завода суммарной производственной мощностью 5,6 млн. тонн цемента в год, предприятия по производству строительных материалов на основе цемента, предприятие по добыче и первичной обработке известняка и гипсового камня, а также ряд сервисных компаний.
Табл. 2. Цементные заводы, входящие в состав АО ХК «Сибирский цемент»
Крупнейший иностранный цементный холдинг, осуществляющий свою деятельность в России - LafargeHolcim, создан в 2015 году в результате слияния двух мировых лидеров по производству и продажам цемента Lafarge и Holcim. В настоящее время в структуре холдинга 4 цементных завода суммарной производственной мощностью 8 млн. тонн цемента в год.
Табл. 3. Цементные заводы, входящие в состав холдинга LafargeHolcim
Еще один крупный участник российского цементного рынка — «ХайдельбргЦемент» — является частью одного из крупнейших мировых производителей нерудных строительных материалов - немецкой группы компаний Heidelberg. В России «ХайдельбергЦемент» специализируется на производстве различных марок цемента, щебня и минерального порошка. Компания оперирует четырьмя российскими цементными заводами суммарной мощностью 5,6 млн. тонн цемента в год, также компания владеет цементными терминалами в Калининграде и Мурманске, производством нерудных строительных материалов (щебень и бетон) в пос. Новогуровском Тульской области.
Табл. 4. Цементные заводы, входящие в состав холдинга «ХайдельбергЦемент»
Анализ внешнеэкономической деятельности.
На экспорт идет всего порядка 2-4% от общего объема произведенного в стране цемента. Основные потребители российского цемента - страны СНГ: Казахстан, Украина, Беларусь, Азербайджан. Доля экспорта в эти страны в разные периоды составляет 95-99%. Несколько изменилась структура экспорта цементной продукции в 2016 году, что связано с ростом поставок отечественной продукции в Финляндию и Абхазию. Поставки в Финляндию и Прибалтику в рамках подписанных контрактов осуществляет холдинг «Евроцемент груп». В Абхазию свою продукцию поставляют АО «Кавказцемент», входящий в состав «Евроцемент груп», и ОАО «Новоросцемент».
Достаточно низкие объемы экспорта обусловлены рядом факторов — это и строгие нормы принятые, к примеру, в Евросоюзе, которые не дают без прохождения сложной и длительной процедуры сертификации потенциальной возможности наращивать объемы экспорта российским производителям, и достаточно высокая себестоимость российского цемента, что является основным фактором, влияющим на конкурентоспособность. В России по-прежнему высока доля производства по энергоемкому и соответственно высокозатратному «мокрому» способу.
Высокая себестоимость отечественного цемента и низкие требования к качеству и стандартам импортной цементной продукции позволили зарубежным производителям постоянно наращивать объемы поставок цемента в Россию. В 2008 году были зафиксированы рекордные объемы импортных поставок цемента - 7,9 млн. тонн, или 13% от внутреннего потребления в стране. После кризисного 2009 года объемы импорта снова стали расти, положительная динамика импортных поставок цемента наблюдалась вплоть до 2015 года. На сегодняшний день из-за девальвации российского рубля зарубежные поставщики утратили основное преимущество, как следствие объемы импорта цемента в 2015-2016 гг. заметно снизились. Изменилась и структура импортных поставок в разрезе стран-поставщиков. Если в 2010 году основными поставщиками цемента в Россию были Турция, Китай, Южная Корея, страны Прибалтики, и на их долю приходилось свыше 80%, то по итогам 2016 года основной объем ввозимого из-за рубежа цемента приходится на страны СНГ: Беларусь и Казахстан - 83,2%.
Объемные показатели цементной отрасли.
Неблагоприятная экономическая обстановка в стране в период 2015-2016 гг. отразилась практически на всех отраслях промышленности, цементная отрасль также не осталась в стороне. Объем производства цемента по итогам 2016 года составил 55 млн. тонн, что ниже показателя докризисного 2014-ого года на 20%. По сути, российские производители в настоящее время используют только 50% своих мощностей. Наибольшее негативное влияние на показатели объемов производства цементной продукции оказывало снижение потребительского спроса в этот период. Постоянно растущие с 2010 года объемы ввода жилья в 2016 году показали падение, которое продолжилось и в начале текущего года.
1 Введение 3
1.1 Современное состояние цементной промышленности 3 1.2 Перспективы развития цементной промышленности 4
2 Общая часть 8
2.1 Способы производства клинкера 8
2.2 Обоснование выбора вращающейся печи сухого способа 10
производства клинкера
3 Технологическая часть 12
3.1 Характеристика топлива 12
3.2 Технологический и теплотехнический режим вращающейся печи 12
с циклонными теплообменниками
3. 3 Конструкция и принцип действия вращающейся печи 15
с циклонными теплообменниками
3.4 Мероприятия по экономии теплоты и топлива 17
4 Расчетная часть 19
4.1 Расчет горения топлива 20
4.2 Расчет потоков воздуха, газа и пыли 24
4.3 Тепловой баланс вращающейся печи 30
4.4 Расчет воздуха на горение и количество отходящих газов 34
4.5 Температура газов на выходе из циклонных теплообменников, 40
пыльной камеры и вращающейся печи
4.6 Конструктивный расчет вращающейся печи 51
5 Охрана окружающей среды и охрана труда 55
5.1 Мероприятия по охране окружающей среды 55
5.2 Правила техники безопасности при обслуживании печи 57 5.3 Правила технической эксплуатации вращающейся печи 58
6 Литература 61
1
Введение
Современное состояние цементной промышленности
Объем производства цемента по итогам первого квартала 2012 года вырос на 15% по сравнению с аналогичным периодом прошлого года и составил 9,609 млн тонн, подсчитали в СМПРО. На докризисные показатели рынок еще не вышел - в 2007-2008 годах в первом квартале объем выпущенного цемента превышал 11 млн тонн. По расчетам президента "Лафарж Цемент" Алекса де Валухоффа, производство в 2012 году вырастет на 10% по сравнению с итогами 2011 года (56,2 млн тонн). "Рынок просто продолжает постепенно восстанавливаться за счет закладки новых домов, инфраструктурного строительства",- отмечает директор по маркетингу СМПРО Евгений Высоцкий. Прошлый год стал рекордным по объему введенного жилья с 2007 года: было сдано 63,2 млн кв. м.
Цена на цемент в первом квартале обычно не растет: в марте тонна без НДС и доставки стоила столько же, сколько в декабре 2011 года,- 2,8 тыс. руб. Евгений Высоцкий говорит, что производители не могут поднимать цены зимой, несмотря на рост тарифов на энергоносители, так как в холодное время спрос на цемент снижается, а объем производства остается высоким. "В сезон, который длится с конца апреля до сентября, цены отыгрывают этот период",- поясняет господин Высоцкий. В прошлом году в этот период цены выросли на 20%, в 2012-м динамика будет сопоставимая, добавляет эксперт.
У производителей цемента более консервативный прогноз. В "Сибирском цементе" рассчитывают, что в этом году цемент подорожает на 12-15% в летний период. Председатель совета директоров "Сухоложскцемента" Максим Сотников считает, что в ближайшие годы ежегодное увеличение цены будет достигать 10%. При таком прогнозе получается, что цены на цемент выйдут на докризисный уровень не раньше 2019 года. В 2007 году одна тонна с учетом доставки стоила около $178, или 4,548 тыс. руб.
Фактором, ограничивающим рост цен на внутреннем рынке, остается импорт, говорит генеральный директор "Базэлцемента" Вячеслав Шматов. По данным СМПРО, объем импортных поставок в первом квартале 2012 года вырос в два раза по сравнению с аналогичным периодом прошлого года и составил 340 тыс. тонн. Господин Шматов напоминает, что, пока нет резкого роста цен, импортерам невыгодно возить цемент в Россию, где цены ниже, чем в Европе. Для сравнения: стоимость тонны в Германии составляет?80 (выше 3 тыс. руб.).
Основным риском для российских производителей в этом сезоне остается транспортная проблема. Аренда вагонов подорожала на 10-15%, и их не хватает, говорит Максим Сотников. Впрочем, постепенно объем перевозок железнодорожным транспортом сокращается в пользу автомобильной доставки: по данным СМПРО, в 2010 году на железную дорогу приходилось 65% поставок, в 2011 году - 60%.
1.2 Перспективы развития цементной промышленности
Цементная промышленность России является базовой отраслью строительного комплекса, от которой зависит состояние и развитие экономики страны, решение проблем воспроизводственных процессов, специальных вопросов строительства жилья, объектов здравоохранения, просвещения и т.п. основными направлениями развития цементной промышленности России являются:
Техническое перевооружение и реконструкция заводов с целью обновления основных фондов, доведения доли сухого способа производства цемента до 80-85%;
Разработка и внедрение высокоэффективных энергосберегающих технологий, удовлетворения требований строительного комплекса в ассортименте и строительно-технических свойствах цемента;
-обеспечение широкого вовлечения в хозяйственный оборот отходов производства смежных отраслей промышленности;
Подготовка и повышение квалификации специалистов производства и научных кадров цементной промышленности;
Уменьшение вредных выбросов в атмосферу и улучшение условий труда;
Подготовка цементных предприятий к переходу на использование в качестве технологического топлива угля и топливо содержащих отходов промышленности;
Переоснащение машиностроительной базы страны и организация массового выпуска цементного оборудования нового поколения;
Совершенствование размещения производства цемента по субъектам федерации, в частности, за счет строительства региональных цементных помольных установок (РЦПУ) на обжиг имеющихся инфраструктур предприятий стройиндустрии тех субъектов Российской Федерации, которые не имеют
цементных предприятий, а также строительство терминалов совмещающих хранение запасов цементного клинкера и других составляющих цементной шихты помол и отгрузку цемента потребителям водным и другими видами транспорта.
На сегодняшний день цементная индустрия является наиболее перспективной сферой развития промышленности. Именно поэтому, по вопросу перспективы развития цементной промышленности составляют рефераты и доклады многие ведущие маркетологи и менеджеры высшего звена компаний, задействованных в данной индустрии. Совсем недавно в России прошла международная конференция, посвящённая перспективам развития цементной промышленности в рефератах и докладах, как на российском, так и на мировом рынке обменивались перспективами применения цемента, проблемами экологии и совершенствования технологий производства. На данной конференции присутствовали представители журнала Цемент Известь Гипс (ZKG International),
который является ведущим техническим журналом на международной арене, целиком охватывающим цементную промышленность и ее смежные отрасли. Акцент был сделан на разработки по рационализации производства, снижению энергопотребления, повышению качества и защите экологии.
В ходе конференции была отмечена положительная тенденция в приросте производственных мощностей в российской цементной промышленности. Особое место занимает холдинг «Евроцемент групп», в состав которого входят десятки заводов по производству цемента, среди которых небезызвестные завод «Жигулевские стройматериалы». Жигулёвский цемент – основная продукция, производимая ОАО «Жигулевские стройматериалы» на территории Самарской области. Жигулёвский цемент в основном обеспечивает отрасли народного хозяйства на территории Средней Волги и славится высоким качеством по приемлемой цене. Кроме того, ОАО «Жигулевские стройматериалы» известен песчано цементными трубами из высококачественного песка - цемента - плиткой и оборудования. Песчано цементные трубы ОАО «Жигулевские стройматериалы» благодаря качественному песку и цементу с применением профессионального оборудования завоевали весь российский рынок данной отрасли.
Участниками конференции завод «Холсим» был отмечен как «завод белого цемента», являющийся крупнейшим производителем данного строительного материала. Продукция «завода белого цемента» имеет высокий коэффициент светоотражения, что позволяет использовать данные строительные материалы для получения любого оттенка при производстве цветных бетонов, искусственного камня и кирпича, цветных сухих смесей и затирок, а также цементной краски, обладая при этом высокой морозостойкостью.
На конференции были отмечены заслуги компании «Накал», специализирующейся на производстве печей шахтных цементационных. Печи шахтные цементационные данной компании отличились высоким качеством, простотой управления и обслуживания и безопасностью. Кроме того, печи шахтные цементационные отличаются своим соответствием с современными
требованиями к энергосбережению.
Также, на конференции было замечено, что перевозка цемента автомобилями является наиболее рациональным способом транспортировки. Перевозка цемента автомобилями представляет собой использование автомобилей-цементовозов для бестарной перевозки цемента. Перевозка цемента в автомобиле-цементовозе в герметически закрытых емкостях обеспечивает его сохранность при погрузке-разгрузке, транспортировании, а также защиту экологии от попадания в атмосферу вредных веществ.
В процессе конференции, особое внимание было уделено лабораторному оборудованию для испытания цемента. Лабораторное оборудование для испытания цемента включает в себя: машины для испытаний цемента на сжатие и изгиб, встряхивающий стол, бачок для испытания цемента кипячением и прибор ПВ-300 для определения густоты цементного теста. Данное лабораторное оборудование для испытания цемента можно приобрести на заводе по производству цемента модульного. Завод по производству цемента модульного также входит в состав холдинга «Евроцемент групп».
Подводя итоги конференции, было отмечено, что в настоящее время наблюдается процесс наращивания инвестиционной активности, происходит процесс перехода цементной промышленности на энергосберегающие технологии (сухой способ производства), строятся и вводятся новые мощности по производству цемента. Но кроме перспектив, были отмечены и некоторые факторы и риски, существенно затрудняющие развитие российской цементной промышленности. К ним, прежде всего, относятся отсутствие четкой информации о потребностях регионов в цементной продукции, необходимой при планировании строительства новых заводов. В связи с этим, одной их первоочередных задач, является недопущение диспропорций в обеспечении цементом российских регионов.
Как развивается цементная промышленность России? Какие проблемы назрели внутри отрасли? Можно ли на основе опыта технологической модернизации в США и ЕС определить перечень необходимых мероприятий для перевода данной отрасли с энергоемкого (мокрого) способа производства на экономный (сухой)?
1. Краткая история развития отрасли. Цементная отрасль наряду с лесной и деревообрабатывающей, химической промышленностью, черной и цветной металлургией образует комплекс конструкционных материалов (ККМ), влияющий на экономический потенциал и уровень промышленного развития страны. Все отрасли ККМ относятся к отраслям по производству промежуточной продукции, т.е. основная часть продукции отрасли направляется на переработку в другие сектора экономики при относительно небольшой доле выпуска, приходящейся на конечное потребление.
Цементная промышленность России характеризуется как отрасль с высоким уровнем физического и морального износа производственных мощностей (износ активной части основных фондов превысил 70%), с низким технологическим уровнем развития, а, следовательно, и низкими показателями экологической безопасности производства. Во многом данная ситуация обусловлена историей развития данной отрасли промышленности в постсоветское время :
- 1989-1991 гг. – потеря управления, начало экономических реформ и спада производства, приватизация как попытка решения основной задачи экономической реформы – создание класса эффективных собственников.
- 1991-1992 гг. – резкое снижение объемов строительства, падение спроса на цемент, тяжелая адаптация цементных заводов к условиям рыночной экономики.
- 1992-1998 гг. – кризисные явления трансформации плановой экономики в рыночную. Этот период характеризуется снижением производства цемента более чем в 3 раза с 84.7 до 26.0 млн. тонн, выбытием 19 млн. тонн мощностей, существенным сокращением отраслевой науки, приходом на российский рынок зарубежных компаний «Holderbank» (Holcim), «Dyckerhoff», «Lafarge». По данным Росстата в этот период до 40% цементных заводов были убыточными. На основе московских перевалочных терминалов консолидируется крупнейшая цементная компании РФ – ОАО «Штернцемент».
- 1999-2001 гг. – начало подъема экономики и как следствие увеличение спроса на цемент. Первые успешные попытки крупных игроков влиять на ценообразование на рынке. Формируется высокая инвестиционная привлекательность цементной отрасли. Ведется активная скупка акций цементных заводов российскими и зарубежными компаниями.
- 2002-2005 гг. – период крупных M&A сделок. Росуглесбыт поглощает ОАО «Штернцемент» с дальнейшим переименованием в Евроцемент. Компания ИНТЕКО, начав с приобретения двух заводов, доводит их количество в группе до пяти. На рынке наблюдается интенсивный рост производства цемента на 8-12% в год, сопровождающийся ценовой войной между ключевыми участниками рынка.
- Апрель 2005 г. – формирование монопольного игрока на рынке цемента Европейской части РФ (Сделка Евроцемент-ИНТЕКО и Евроцемент-Су-155). Евроцемент контролирует более 40% российского рынка цемента. Вмешательство ФАС в регулирование показателей цены и объемов производства носит скорее демонстративный характер.
- 2005-2007 гг. – темпы роста производства цемента продолжают оставаться высокими. Цены на цемент, объемы производства, инвестиционная привлекательность цементного бизнеса достигают максимальных уровней. Появляются признаки дефицита цемента и тенденция к увеличению объемов импорта. Использование мощностей на многих предприятиях Европейской части РФ приблизилось к своему пределу.
По объемам производства в условиях постоянного роста спроса за период 2000-2007 гг. Россия достигла уровня 72% от объема выпуска 1990 года.
В докризисный период основными локомотивами роста спроса на цемент являлись федеральные целевые программы (ФЦП) “Доступное жилье”, “Сочи 2014” и др. Национальные программы, реализуемые в РФ, являются весьма емкими по объему вовлекаемых ресурсов, в том числе и в рамках продукции промышленности строительных материалов, строительного сектора.
Ожидалось, что среднегодовой темп прироста потребности экономики России в цементе до 2015 г. будет не менее 10%. По экспертным оценкам НИИцемента, датированным 2007 годом, потребность стройкомплекса в цементе в 2010 г. могла составить 80-90 млн. т, а в 2012-2015 гг. – 115-120 млн. т. При дальнейшем снижении темпов прироста до 8% в 2016 г. и до 5% в последующие годы потребность выросла бы до 125-127 млн. т, в 2020 г. – до 150-162 млн.т. и в 2025 г. – до 190-206 млн. т.
В докризисный период спрос на данную продукцию отрасли опережал предложение, что приводило к увеличению цен на внутреннем рынке, созданию условий для импорта цемента из Европы, Китая, Турции и других стран.
Следует учитывать, что спрос на цемент носит сезонный характер, зависящий как от спроса со стороны основных его секторов-потребителей, так и применяемых технологий для его производства. Устаревшие технологии производства не позволяют в отдельных случаях производить клинкер в зимний период, что формирует дисбаланс в месячной загрузке на отдельных производствах, напрямую влияет на уровень использования производственных мощностей, привлечение инвестиций в отрасль, загрузку транспортного парка для перевозки цемента (табл.1) .
Таблица 1. Производство цемента в России по месяцам (млн.т).
2010 | 1,70 | 2,10 | 3,20 | 4,00 | 4,90 | 5,60 | 5,60 | 5,90 | 5,30 | 5,10 | - | - | - |
2009 | 1,63 | 2,42 | 3,00 | 3,49 | 4,08 | 4,64 | 5,16 | 4,90 | 4,80 | 4,30 | 3,00 | 2,80 | 44,22 |
2008 | 2,95 | 3,68 | 4,62 | 5,37 | 5,38 | 5,09 | 5,53 | 5,40 | 5.02 | 4,62 | 3,21 | 2,58 | 53,48 |
2007 | 6,04 | 3,49 | 4,37 | 5,23 | 5,62 | 5,87 | 6.01 | 6,09 | 5,96 | 5,78 | 4,58 | 3.45 | 59,66 |
2006 | 2,06 | 2,30 | 3,64 | 4,44 | 5,02 | 5,41 | 5,97 | 5,93 | 5,44 | 5,31 | 4,57 | 4,02 | 54,73 |
2005 | 2,07 | 2,39 | 3,15 | 3,64 | 4,10 | 5,05 | 5,34 | 5,53 | 5,10 | 4,94 | 3,64 | 3,23 | 48,35 |
2004 | 2,00 | 2,40 | 3,20 | 3,80 | 4,30 | 4,80 | 5,00 | 5,00 | 4,70 | 4,40 | 3,40 | 2,60 | 45,61 |
2003 | 1,60 | 2,10 | 2,70 | 3,30 | 3,80 | 4,30 | 4,70 | 4,70 | 4,30 | 4,10 | 3,20 | 2,30 | 40,99 |
2000 | 1,70 | 1,80 | 2,20 | 2,50 | 2,80 | 3,20 | 3,30 | 3,60 | 3,30 | 3,20 | 2,80 | 2,10 | 32,28 |
2. Развитие отрасли в кризисный период. Первым годом развития отрасли в условиях кризиса является 2008 г. Наибольший спад объемов производства в 2008 году к аналогичным месяцам в 2007 году приходится на январь (в 2 раза). В остальные месяцы – на 15-20% по отношению к аналогичным периодам. Спад объясняется как ростом цен на энергоносители, так и снижением объемов строительства жилья.
Другой составляющей, оказавшей влияние на объемы производства цемента, явилось принятие мер по регулированию импортных поставок данной продукции. После отмены таможенных пошлин на импорт цемента ведущие холдинги данного сектора экономики, на долю которых приходится более 70% всех производственных мощностей (ЗАО “ЕВРОЦЕМЕНТ-груп”, “Холсим” и “Сибирский цемент”), для удержания отпускных цен стали сокращать объемы его производства, создавая тем самым “искусственный дефицит” (8,8 млн. т цемента), который впоследствии был компенсирован за счет внешних поставок.
Итогом данных мероприятий явилось сокращение объема производства цемента в 2008 г. по сравнению с 2007 г. на 10,6% (53,48 млн. т). В 2009 г. динамика сокращения выпуска сохранилась (с 53,48 до 44,1 млн. т).
Падение спроса на жилье вследствие снижения платежеспособности населения, рост цен на энергоносители (электроэнергию, природный газ, уголь) нашло прямое отражение на объемах внутреннего потребления цемента, объемах его производства: за январь-июль в 2009 году отрасль достигла аналогичных объемов 2003 года. Наибольший спад объемов производства в 2009 году к аналогичным месяцам в 2008 году приходится на январь (почти в 2 раза). С февраля по июль – 15-20%, в остальные месяцы – 5-7% по отношению к аналогичным периодам.
Объем производства цемента в 2009 г. составил 96,7% от выпуска 2004 г. Отчетный период можно охарактеризовать как переломный: за первые шесть месяцев 2010 г. было произведено 21,5 млн. т цемента, что на 11,6% больше аналогичного показателя за 2009 г.
Максимальные объемы производства цемента в 2010 г. достигнут уровня 49-51 млн. т, т.е. уровня 2005-2006 годов.
Перспективные объемы производства цемента зависят от скорости восстановления объемов строительства жилья.
По экспертным оценкам, за 2010-2011 гг. будет введено около 110 млн. кв. м жилой площади (110-120 млн. т цемента), что фактически может быть покрыто за счет существующих производственных мощностей цементной промышленности.
Исходя из вышеизложенного, перспективы развития отрасли определяются такими ключевыми факторами как: используемые технологии, спрос на продукцию, инвестиции и транспортная инфраструктура.
3. Технологическое развитие отрасли. Производство цемента состоит из двух технологических циклов: 1. производство клинкера; 2. измельчение клинкера совместно с гипсом и другими добавками – получение портландцемента. В зависимости от способа подготовки сырьевых смесей различают сухой, мокрый и комбинированный способы производства клинкера.
При мокром способе тонкое измельчение сырьевой смеси производят в водной среде с получением шихты в виде водной суспензии – шлама 30-50%. В настоящее время в России мокрым способом производится около 85% клинкера.
При сухом способе производства сырьевую шихту готовят в виде тонкоизмельченного сухого порошка, поэтому перед помолом или в процессе его сырьевые материалы высушивают. Данный способ нашел наибольшее распространение в мире, поскольку является менее энергоёмким по сравнению с мокрым способом.
Комбинированный способ может базироваться как на мокром, так и на сухом способе производства шихты. В первом случае сырьевую смесь готовят по мокрому способу в виде шлама, обезвоживают на фильтрах и подают на обжиг в печи в виде полусухой массы. Во втором случае сырьевую смесь готовят по сухому способу, а затем гранулируют с добавкой воды, после чего происходит обжиг.
Одной из основных проблем отрасли является несовершенство технологического процесса, поскольку российский цемент производится по высокозатратным, устаревшим технологиям.
Почти 85% клинкера в отечественной цементной промышленности производится мокрым способом производства с удельным расходом условного топлива до 200-230 кг.у.т./т, в то время как в промышленно-развитых странах (Япония, ЕС) большая часть клинкера обжигается по сухому способу с расходом 120-130 кг.у.т./т., а в отдельных случаях – 100 кг.у.т./т. В США 80% мощностей ориентированы на сухой способ производства, 20% – на мокрый.
Процесс перехода США с мокрого на сухой способ производства цемента составил около 25 лет: доля мощностей, работающих по технологии сухого производства, была увеличена с 38% до 80% . Изменение пропорций производства цемента в США сухим, мокрым и комбинированным способами представлено на рис.1.
Рис.1. Изменение пропорций производства цемента в США сухим, мокрым, комбинированным способами с 1990 по 2008 гг.
Печной парк цементной промышленности США по состоянию на 01.01.2007 состоит из 54 печей мокрого способа и 132 – сухого способа производства (табл.2) .
Таблица 2. Структура печного парка США.
Технологическая структура производства цемента в других странах-производителях представлена в табл.3 .
Таблица 3. Структура производства цемента по видам технологий в мире.
Страна | Технологии производства клинкера (% от объема производства (выпуска)) | |||
---|---|---|---|---|
Сухой | Полусухой | Мокрый | Старые шахтные печи | |
ЕС | 90 | 7,5 | 2,5 | |
Китай | 50 | 0 | 3 | 47 |
Индия | 50 | 9 | 25 | 16 |
Япония | 100 | |||
Испания | 92 | 4,5 | 3,5 | 0 |
Мексика | 67 | 9 | 23 | 1 |
Проводя модернизацию цементной промышленности, Россия первоначально должна приблизиться к структуре США. Только 2 из 190 действующих в России печных агрегатов могут быть отнесены к числу современных (ОПО “Невьянский цементник” (Свердловская область) и ОАО “Серебряков цемент” (Волгоградская область)). Технологическая структура печного парка цементной промышленности России представлена в табл.4 .
Таблица 4. Структура печного парка России.
Российские заводы, работающие по сухому способу, в основном, используют устаревшие технологии, что не дает экономии в затратах, типичной для этого способа производства в других странах.
Почти весь цемент и до 90% сырья в отечественной промышленности измельчается в шаровых мельницах открытого цикла помола. Расход электроэнергии только на передел помола цемента составляет около 40 кВт*ч, в то время как при широко распространенном за рубежом замкнутом цикле он не превышает 25-30 кВт*ч.
Кроме того, использование в системах замкнутого цикла высокоэффективных сепараторов 3-го поколения позволяет направленно влиять на гранулометрический состав цемента и обеспечивать получение заданных свойств, в том числе при производстве многокомпонентных цементов. Расход топлива на этих агрегатах составляет соответственно 128 и 143 кг.у.т./т клинкера, т.е. находится на уровне 60-65% от среднеотраслевого уровня затрат и соответствует уровню расхода в ЕС (табл.5) .
Таблица 5. Удельный расход топлива на 1 т клинкера.
Однако переход на сухой способ производства в России влечет за собой определенные проблемы. Если цена тонны условного топлива у нас в стране повысится до уровня западной, то не менее 80% цемента Россия вынуждена будет производить по сухому способу производства или же вообще прекратить его производство. Дешевле станет покупать его в Турции, Китае и других странах. Энергоемкий мокрый способ производства станет неконкурентоспособным по сравнению с сухим, являющимся более дешевым. На коренную же реконструкцию и модернизацию требуются достаточно большие вливания инвестиций в данный сектор экономики. Так, в частности, на перевод завода мощностью в 1 млн. т на сухой способ производства требуется около 70 млн. долларов США.
Поэтому в условиях технологической реструктуризации данной отрасли необходимо проведение мероприятий по поэтапному переводу мощностей на сухой способ производства, проявляющееся как в реконструкции действующих линий, так и строительстве новых цементных заводов. Использование помола сырья в замкнутом цикле, позволяющего снизить энергоемкость процесса в 1,5 раза (с 40 до 25 кВт*ч), а также снижение влажности шлама за счет применения новых более эффективных разжижителей, позволяющих сократить на 15-20% удельный расход топлива, дают возможность приблизить (по затратам топливно-энергетических ресурсов) мокрый способ производства к сухому, обеспечивая его конкурентоспособность.
Удешевление затрат на топливно-энергетические ресурсы возможно также посредством использования альтернативных источников.
В мировой практике используют различные подходы к выбору топливно-энергетических ресурсов, используемых при производстве клинкера. К основным топливно-энергетическим ресурсам можно отнести природный газ, уголь, мазут, сланцы. Наряду с ними широкое применение находит внедрение альтернативных видов топлива, позволяющее решать одновременно две задачи – утилизацию вторичного сырья и замену основного ресурса (природного газа, угля, мазута).
В странах ЕС в составе технологического топлива, используемого при производстве цемента, все в большей степени находят применение вторичные виды ресурсов. Замещение основного вида топлива вторичным в отдельных странах ЕС составило: во Франции – 27%, в Австрии – 29%, в Швейцарии – 34%, в Нидераландах – 72%.
В качестве альтернативного топлива используются топливо-содержащие отходы – шины, резина, отработанные масла, пластик, бумага, переработанные фракции из бытовых отходов, животной муки и жиров, древесины, растворителей и т.п.
Доля энергоносителей в себестоимости цемента, производимого в РФ, составляет 50-57%. Распределение топлива, используемого при производстве цемента, представлено в табл.5 (% от объёма использованных топливно-энергетических ресурсов) .
Таблица 5. Структура топливно-энергетических ресурсов, используемых при производстве цемента (%).
Вид топлива | 2000 | 2001 | 2002 | 2004 | 2006 | 2008 | 2009 |
---|---|---|---|---|---|---|---|
Природный газ | 86.8 | 90.7 | 91.7 | 93.2 | 92.4 | 92.1 | 91,9 |
Мазут | 4.7 | 2.2 | 2.3 | 1.5 | 1.5 | 1.9 | 2,2 |
Уголь | 8 | 6.5 | 5.4 | 5 | 6.1 | 6 | 6,9 |
Сланец | 0.5 | 0.6 | 0.6 | 0.3 | 0 | 0 | 0 |
Ориентация отрасли на один топливно-энергетический ресурс делает ее “уязвимой” к динамике цен на него. Опережающий рост цен на топливно-энергетические ресурсы по сравнению с ценами на цемент приводит к увеличению себестоимости продукции данной отрасли, а в условиях стабилизации цен на него – снижению финансовых показателей, влияющих на объем привлекаемых инвестиций, определяющих процесс модернизации цементной промышленности, её технологическое развитие.
Наглядно это может быть проиллюстрировано на основании данных базовых индексов цен на промышленную продукцию за период 1995-2009 гг. (табл.6) .
1996 | 1997 | 1998 | 1999 | 2000 | 2001 | 2002 | 2003 | |
---|---|---|---|---|---|---|---|---|
Электроэнергия | 100.0 | 108.50 | 110.89 | 132.73 | 188.08 | 242.25 | 310.80 | 325.50 |
Топливо дизельное | 100.0 | 121.00 | 130.20 | 419.88 | 646.62 | 602.00 | 627.89 | 797.40 |
Мазут топочный | 100.0 | 116.00 | 123.19 | 316.85 | 594.09 | 380.22 | 591.24 | 578.80 |
Газ естественный | 100.0 | 100.60 | 109.25 | 124.11 | 201.06 | 307.82 | 417.40 | 295.10 |
Уголь | 100.0 | 99.40 | 98.90 | 122.24 | 171.26 | 212.02 | 237.89 | 242.40 |
Цемент | 100.0 | 107.90 | 114.37 | 151.89 | 227.23 | 282.90 | 343.44 | 437.50 |
Таблица 6. Базовые индексы цен производителей на топливно-энергетические ресурсы и цемент (%).
2004 | 2005 | 2006 | 2007 | 2008 | 2009 | |
---|---|---|---|---|---|---|
Электроэнергия | 392.6 | 435.8 | 480.7 | 548.5 | 650.19 | 737.7 |
Топливо дизельное | 1275.1 | 1505.9 | 1454.7 | 1899.8 | 1238,7 | 1397.9 |
Мазут топочный | 548.7 | 1139.2 | 1154.0 | 1879.8 | 979,38 | 1527.7 |
Газ естественный | 624.1 | 740.2 | 840.2 | 961.2 | 1183,6 | 1141.0 |
Уголь | 347.9 | 415.7 | 397.8 | 463.1 | 630.0 | 562.59 |
Цемент | 500.5 | 590.6 | 745.4 | 1233.6 | 969.24 | 798.36 |
Данные табл.6 показывают, что на всем анализируемом периоде цены на газ росли быстрее цен на цемент, исключением является 2003 г.; аналогичная ситуация и с продуктами нефтепереработки (топливо дизельное, мазут топочный). Уголь является наиболее предпочтительным топливно-энергетическим ресурсом. Ограничениями на перевод производственных мощностей на уголь являются: 1. транспортные издержки на его доставку потребителю; 2. необходимость установки нового оборудования, работающего на нем (в настоящее время в РФ не используются технологии ориентированные на комбинированный вариант – уголь+природный газ); 3. Использование определенных марок угля (марки, группы, подгруппы бурых углей и антрацитов Д, ДГ, СС, ТС, Т и не использующиеся для коксования Г, ГЖО,КС, КСН).
4. Транспортная инфраструктура отрасли. Цемент является сыпучим продуктом и перевозится всеми видами транспорта. Ключевая роль в данном направлении принадлежит железнодорожному транспорту (табл.7) , на долю которого приходится более 85% перевозок (рис.2).
Таблица 7. Объемы перевозок цемента на транспорте, млн. т.
1991 | 1995 | 2000 | 2005 | 2006 | 2007 | 2008 | |
---|---|---|---|---|---|---|---|
Всего | 70,43 | 32,10 | 27,43 | 42,25 | 47,53 | 53,55 | - |
Ж/Д | 63,00 | 26,80 | 22,40 | 34,30 | 38,30 | 41,90 | 36,0 |
Морской транспорт | 0,58 | 0,20 | 0,20 | 0,05 | 0,08 | 0,08 | н/д |
Внутренний водный | 0,70 | 0,13 | 0,05 | 0,13 | 0,08 | 0,33 | н/д |
Прочие виды транспорта | 6,18 | 5,00 | 4,80 | 7,78 | 9,10 | 11,28 | н/д |
Средняя дальность перевозок на ж/д транспорте, км | |||||||
н/д | 503 | 528 | 603 | 645 | 738 | 1143 |
За анализируемый период средняя дальность перевозок увеличилась в 2 раза, что, в частности, отражает географию потребителей данной продукции – крупные города, мегаполисы, в которых строительный сектор снизил объемы строительства, но не остановился; развитие сектора жилищного строительства происходит по большей части за счет реализации проектов, сформированных еще в докризисный период и находящихся в стадии завершения. (Справочно: средняя дальность перевозок цемента в странах Евросоюза составляет менее 250 км.)
Рис.2. Средняя дальность и объемы перевозок цемента ж/д транспортом.
Достижение данного показателя возможно посредством формирования “зональных” перевозок, ориентированных на доставку продукции потребителю внутри субъекта РФ. Все это требует развития не только Федеральных целевых программ, выполняемых преимущественно в региональных центрах, но и ориентированных на снижение доли аварийного/ветхого жилого фонда в крупных и средних муниципальных образованиях субъекта РФ, где строительный сектор ориентирован преимущество на развитие многоэтажного строительства. Одним из сдерживающих факторов в выполнении данного направления является фактор неравномерного расположения минерально-сырьевой базы отрасли, определяющей географию развития/размещения предприятий цементной промышленности.
Объемы перевозок цемента на железнодорожном транспорте зависят как от пропускной способности, так и подвижного состава, его качества. Цемент перевозится в хоппер-вагонах: срок эксплуатации большей части их фонда составляет более 20 лет, прошедших не один раз капитальный ремонт. При устойчивом росте внутреннего потребления на цемент в 2000-2007 гг. фиксировалась нехватка тоннажа как для перевозки цемента от отечественных производителей до потребителей, так и со стороны импортеров. Активный выпуск вагонов данного типа предприятиями машиностроительного комплекса позволил в короткие сроки провести обновление одной из неотъемлемой части фондов данной отрасли, но не решить саму проблему в целом. Из-за дефицита хоппер-вагонов в 2007 г. не было вывезено с российских цементных заводов несколько млн. т произведенного цемента. В дальнейшем, после прохождения периода стагнации на рынке цемента и роста внутреннего потребления на цемент, аналогичная ситуация может повториться.
В докризисный период, в условиях опережения предложения над спросом, компенсация дефицита на рынке происходила посредством импорта цемента как из стран СНГ, в первую очередь, с Украины и из Белоруссии, так и вне СНГ – Турции и Китая. Если со стороны стран СНГ цемент доставляется преимущественно ж/д транспортом, то из Китая и Турции – морским. Эти страны близко расположены к основным перевалочным пунктам: черноморским (Новороссийск) и дальневосточным (Находка, Владивосток) морским портам. Цемент там значительно дешевле, чем у нас: в Турции - около 100 долларов за тонну, в Китае - около 50–60 долларов (по состоянию на 01.07.2010).
Российские порты не могут принимать цемент навалом (то есть засыпать его с судов в железнодорожные вагоны), так как отсутствуют специальные терминалы. По этой причине морские поставки осуществляются в специальных мешках - биг-бэгах емкостью полторы-две тонны. Перевалочные работы из биг-бэгов являются трудоемкими и высокозатратными, учитывая отсутствие отлаженной механизированной перегрузки, т.е. фактически грузы обрабатываются вручную.
В полувагоне умещается 60–70 таких мешков. Поскольку вагоны металлические, то существует риск разрыва биг-бэгов, а значит и уровень потерь цемента с 1 импортируемой тонны морским транспортом возрастает в разы по отношению к требованиям, используемым при составлении финансовой отчетности – норм естественной убыли (НЕУ) при транспортировке и погрузочно-разгрузочных работах (ПРР).
Комплексные потери при транспортировке и разгрузке цемента в биг-бэгах доходят до 5–10% против 0,25% при самой транспортировке и 1-2% при ПРР.
По экспертным оценкам, страны-экспортеры способны производить для России не менее 10–12 млн. тонн цемента в год. Флот в состоянии осуществлять транспортировку таких объемов цемента, а инфраструктура портов позволяет ежегодно принимать не более 7–8 млн. тонн цемента в год.
“Ахиллесовой пятой” морских портов остается железнодорожная инфраструктура, перегруженная и работающая на пределе своих возможностей. Китай в случае сворачивания/переноса на неопределенный срок инвестиционных программ по вводу производственных мощностей в РФ может занять первое место среди стран-импортеров цемента в нашу страну.
Неразвитость логистической инфраструктуры портов Дальнего Востока оказывает существенное влияние на объемы их поставок – максимально не более 400 тыс. тонн в год.
Другой аспект связан с качеством получаемой конечным потребителем продукции: если цемент пролежал на хранении месяц, то он теряет одну единицу в марочности. Таким образом, купив в Китае марку 500ДО, московские потребители, до которых цемент идет в лучшем случае месяц, рискуют получить марку 400ДО.
Все это требует пересмотра подходов к формированию транспортно-логистических коридоров и инвестиций в развитие транспортной инфраструктуры морских портов.
5. Спрос на продукцию. Интенсивность потребления цемента в регионах зависит от объемов строительства жилого и производственного фонда, дорог специального назначения, транспортной и торгово-посреднической наценки на цемент, скорости его доставки, определяющей удаленность потребителя от поставщика (завода). Возникновение профицита/дефицита цемента во внутреннем потреблении на уровне регионов должно рассматриваться как один из ключевых факторов развития производственной структуры данной отрасли в регионах и федеральных округах (табл.8) .
Таблица 8. Производство и потребление цемента в федеральных округах, тыс. т.
Федеральные округа | Производство | Потребление | ||||
---|---|---|---|---|---|---|
2006 | 2007 | 2008 | 2006 | 2007 | 2008 | |
Центральный | 54,73 | 59,93 | 53,48 | 53,25 | 61,07 | 60,93 |
Северо-Западный | 15,38 | 15,31 | 11,42 | 18,47 | 19,99 | 16,83 |
Южный | 3 ,45 | 4,34 | 3,37 | 3,86 | 4,29 | 4,28 |
Приволжский | 9,62 | 9,93 | 9,86 | 7,77 | 8,96 | 7,88 |
Уральский | 6,23 | 6,63 | 5,78 | 5,17 | 6,20 | 6,40 |
Сибирский | 7,07 | 8,53 | 8,99 | 6,06 | 7,35 | 6,35 |
Дальневосточный | 1,42 | 2,01 | 2,92 | 1,43 | 1,54 | 1,62 |
Импорт | 0,79 | 2,75 | 8,13 | |||
Экспорт | 3,20 | 1,86 | 0,80 |
Анализ производства и потребления цемента по федеральным округам показывает, что завозным регионом является ЦФО и вывозными – Южный и Приволжский федеральные округа, поэтому и производственные мощности должны располагаться на минимальном удалении от их основных потребителей для минимизации транспортных и других затрат, влияющих на цену конечного потребителя.
Организация межрегиональных поставок зависит не только от наличия транспорта и подвижного состава, существующих логистических коридоров для осуществления поставок, но и от объемов внутреннего потребления в регионах, где расположены сами производства. В данном случае нельзя не учитывать и нюанс приграничного расположения заводов, ориентирующих их на формирование направления поставок, в том числе и в близлежащие регионы (табл.9). Исходя из данных табл.9, можно сделать выводы о наличии или отсутствии возможностей цементных заводов покрывать внутренний спрос и целесообразности развития дополнительных производственных мощностей в регионах.
Завод | Доля | |
---|---|---|
Евроцемент | 14,29 | 93% |
Белгородский цемент | 1,41 | 95% |
Жигулевские стройматериалы | 0,53 | 93% |
Кавказцемент | 1,95 | 96% |
Катавский цемент | 0,38 | 78% |
Липецкцемент | 0,95 | 92% |
Мальцовский портландцемент | 2,16 | 94% |
Михайловцемент | 1,18 | 99% |
Невьянский ЦЗ | 0,77 | 92% |
Осколцемент | 2,16 | 91% |
Пикалевский ЦЗ | 1,24 | 99% |
Подгоренский цементник | 0,09 | 55% |
Савинский цемзавод | 0,52 | 92% |
Ульяновскцемент | 0,91 | 86% |
Таблица 9. Потребление цемента в регионе его производства в 2008 г.
Завод | Потребление цемента в регионе его производства, млн. т. | Доля |
---|---|---|
Сибирский цемент | 3,90 | 78% |
Ангарскцемент | 0,83 | 85% |
Каменский ЦЗ (Тимлюйцемент) | 0,40 | 96% |
Красноярский ЦЗ | 0,92 | 100% |
Топкинский цемент | 1,74 | 65% |
Новоросцемент | 3,26 | 81% |
Новоросцемент | 3,26 | 81% |
Мордовцемент | 2,00 | 55% |
Мордовцемент | 2,00 | 55% |
Себряковцемент | 1,97 | 59% |
Себряковцемент | 1,97 | 59% |
Lafarge | 2,86 | 87% |
Воскресенскцемент | 1,81 | 100% |
Уралцемент | 1,06 | 71% |
Holcim | 2,11 | 68% |
Вольскцемент | 1,23 | 56% |
Щуровский цемент | 0,88 | 98% |
Полное использование мощностей цементных заводов для покрытия внутреннего спроса в субъектах РФ их нахождения продуцирует ввоз цемента из других, в свою очередь, увеличивая среднюю дальность перевозки этой продукции до потребителя и рост транспортной составляющей в конечной его стоимости.
Отсутствие ввода новых, рост уровня износа фондов (ОПФ) привели к сокращению мощностей на 15-18 млн. т. Ежегодное выбытие производственных мощностей составляет около 1,2-1,5 млн. т. Износ производственных фондов достиг уровня 70%.
Мощность цементных заводов России по состоянию на 01.01.2008 составила 76 млн. т, уровень загрузки – 65-70%. Данного фонда мощностей достаточно для покрытия спроса на внутреннем рынке в объеме 60 млн. т. По оптимистичному сценарию, производственные мощности отрасли к 2015 г. возрастут до 100 млн. т, к 2020 г. – до 125-140 млн. т.
Таким образом, ввод в эксплуатацию мощностей по производству цемента может составить ежегодно, начиная с 2012 г., от 4 до 7 млн. т. Фактически будет введено 50-60 млн. т производственных мощностей, работающих по сухому способу производства. Одновременно с вводом производственных мощностей необходимо проведение ежегодной реконструкции технологических линий мокрого способа производства мощностью в 2-3 млн. т, ориентированных на комбинированный вариант использования топливно-энергетических ресурсов (уголь и мазут; газ и мазут, сланцы).
6. Выводы и предложение. Цементная промышленность является ключевой отраслью комплекса конструкционных материалов. В условиях отсутствия финансирования на реконструкцию и развитие данного сектора экономики его производственные мощности сократились на 15-18 млн. т и составили 70 млн. т, а уровень их износа до 75%. При таких условиях максимальные (пиковые) объемы производства цемента составляют 55-60 млн. т.
Развитие федеральных программ, требующих привлечения большого количества ресурсов, в том числе и продукции данной отрасли, нашли свое отражение в росте импорта цемента, преимущественно из стран СНГ (Украины, Белоруссии): с 2000 по 2007 гг. импорт цемента увеличился с 0,1 до 2,4 млн. т. В докризисный период объемы производства цемента достигли уровня 71% от объема производства в 1990 г. и выросли с 2000 по 2007 гг. с 35,3 до 59,7 млн. т, т.е. на 24,4 млн. т.
Правовое регулирование, направленное на снижение стоимости цемента для конечного потребителя, проявившееся в отмене таможенных пошлин на импортируемый цемент, привело к созданию “искусственного дефицита” со стороны российских производителей, сокративших объемы его производства на 8,8 млн. т в 2008 г. Аналогичная ситуация повторилась и в 2009 г.
Дальнейшее развитие отрасли определяется возможностями обновления и наращивания мощностей для покрытия внутреннего потребления за счет “цемента российских производителей”. Объем заявленного ввода/реконструкции мощностей в отрасли до 2015 г. холдингами составил 50% от имеющихся мощностей (около 35 млн. т).
До 85% цемента в отрасли производится мокрым способом, являющимся энергоемким, при котором затраты топливно-энергетических ресурсов превышают в 2 раза международные, где основным является сухой способ. Актуальным для РФ является использование опыта США по переводу с мокрого на сухой способ производства (процесс перевода мощностей США составил около 25 лет). Естественно, технологическое реформирование данного сектора не может быть ориентировано на данный срок. По нашему мнению, технологическая модернизация данного сектора должна составить около 10 лет, т.е. до 2020 г.
Снижение объемов жилищного строительства и цен на продукцию привело в большинстве случае к переносу большей части инвестиционных проектов на неопределенный срок. В лучшем случае проводятся подготовительные работы по формированию инфраструктуры, разработке карьеров для поставки сырья на завод, а также реконструкция действующих линий.
Все это при условии оживления строительной отрасли может сгенерировать рост импорта цемента, ограничениями на который является дефицит подвижного состава (хоппер-вагонов) и неразвитость инфраструктуры портов, через которые возможно наращивание поставок дешевого цемента, в первую очередь из Китая. Неравномерное расположение ключевых потребителей данной продукции приводит к росту дальности ее перевозок и сроков доставки конечному потребителю, что напрямую отражается на качестве цемента (его марочности). Одним из решений данного вопроса является налаживание операций реимпорта цемента из стран СНГ, закупающих его в Китае. Белоруссию в данном случае следует рассматривать как одну из основных стран-участниц этой модели внешних закупок. Логика модели реимпорта достаточно прозрачна: предприятия Белоруссии для формирования необходимых стабильных финансовых результатов импортируют его в РФ, а строительные организации Белоруссии, как основные потребители, решают вопрос его импорта из Китая. Частично такого рода модель поставок была реализована в 2006-2007 гг.
Литература
- Данные сайта ФСГС www.gks.ru .
- Данные НИЦ “Гипроцемент-наука”.
- USA Bureau of Mines/ Mineral yearbook 1990.
- USA Bureau of Mines/ Mineral yearbook 1992.
- USA Bureau of Mines/ Mineral yearbook 1994.
- USA Bureau of Mines/ Mineral yearbook 1996.
- USA Bureau of Mines/ Mineral yearbook 1994.
- USA Bureau of Mines/ Mineral yearbook 1996.
- USA Bureau of Mines/ Mineral yearbook 1996.
- USA Bureau of Mines/ Mineral yearbook 1998.
- USA Bureau of Mines/ Mineral yearbook 2000.
- USA Bureau of Mines/ Mineral yearbook 2002.
- USA Bureau of Mines/ Mineral yearbook 2004.
- USA Bureau of Mines/ Mineral yearbook 2006.
- USA Bureau of Mines/ Mineral yearbook 2008.
- Данные Европейской ассоциации производителей цемента (www.cembureaux.org).
- материалы ООО «СМПро».
Открытие бизнеса
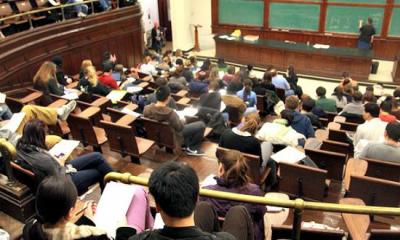
Где можно и где нельзя работать после туберкулеза Где можно работать после
Форекс
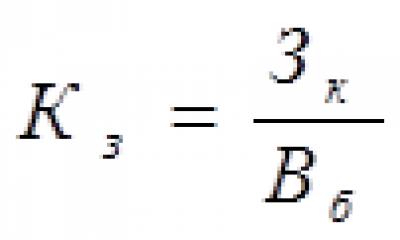
Направления повышения эффективности использования собственного капитала На базе двигателя с плоским печатным якорем разработаны изделия для автомобильной промышленности
Банки
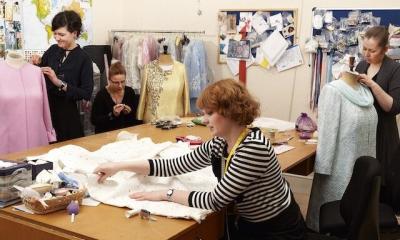