Выполняются заказы по лазерной резке широкого круга материалов, конфигураций и размеров.
Сфокусированное лазерное излучение позволяет резать практически любые металлы и сплавы, независимо от их теплофизических свойств. При лазерной резке отсутствует механическое воздействие на обрабатываемый материал и возникают незначительные деформации. Вследствие этого можно осуществлять лазерную резку с высокой точностью, в том числе и легкодеформируемых и нежестких деталей. Благодаря большой мощности лазерного излучения обеспечивается высокая производительность процесса реза. При этом достигается такое высокое качество реза, что в полученных отверстиях можно нарезать резьбу.
Широко применяется в заготовительном производстве. Основное преимущество лазерной резки - она позволяет переходить с одного типа деталей любой геометрической сложности на другой тип практически без затрат времени. По сравнению с традиционными методами резки и механообработки скорость различается в несколько раз. Из-за отсутствия теплового и силового воздействия на изготавливаемую деталь, она не претерпевает деформаций в процессе изготовления. Качество изготавливаемой продукции позволяет совершать сварку встык без смещений кромок среза и предварительной обработки соединяемых сторон.
Твердотельные лазеры неметаллические материалы режут значительно хуже газовых, однако имеют преимущество при резке металлов - по той причине, что волна длиной 1 мкм отражается хуже, чем волна длиной 10 мкм. Медь и алюминий для волны длиной 10 мкм - почти идеально отражающая среда. Но, с другой стороны, сделать CО2-лазер проще и дешевле, чем твердотельный.
Точность лазерной резки достигает 0,1 мм при повторяемости +0,05 мм, причем качество реза стабильно высокое, поскольку зависит только от постоянства скорости перемещения лазерного луча, параметры которого остаются неизменными.
Краткая характеристика реза: окалина обычно отсутствует, небольшая конусность (завист от толщина), получаемые отверстия круглые и чистые, возможно получение совсем небольших деталей, ширина реза 0,2-0,375 мм, прижоги незаметны, тепловое воздействие очень мало, имеется возможность резки неметаллических материалов.
Прошивка отверстий
Немаловажным фактором для лазерной резки является прошивка первоначального отверстия для ее начала. У некоторых лазерных установок имеется возможность с помощью процесса так называемой летающей прошивки в холоднокатаной стали толщиной 2 мм получать до 4 отверстий в секунду. Получение одного отверстия в более толстых (до 19,1 мм) листах из горячекатаной стали при лазерной резке осуществляют с помощью силовой прошивки примерно за 2 с. Применение обоих этих методов позволяет увеличить производительность лазерной резки до уровня, достигаемого на вырубных прессах с ЧПУ.
Пробивка отверстий
С помощью этого метода можно получать отверстия диаметром 0,2-1,2 мм при толщине материала до 3 мм. При соотношении высоты отверстий к их диаметру 16:1 лазерная пробивка превосходит по экономичности почти все другие методы. Объектами применения этой технологии являются: сита, ушки игл, форсунки, фильтры, ювелирные изделия (подвески, четки, камни). В промышленности с помощью лазеров осуществляется пробивка отверстий в часовых камнях и в волочильных фильерах, причем производительность достигает 700 тыс. отверстий в смену.
Скрайбирование
Часто используемым является режим несквозной резки, так называемое скрайбирование. Оно широко используется в промышленности, в частности, в микроэлектронике, для разделения кремниевых шайб на отдельные элементы (фрагменты) по заданному контуру. В этом процессе также оказывается существенным взаимная ориентация проекции вектора электрического поля падающего излучения и направления сканирования для обеспечения высокой эффективности и качества процесса.
Скрайбирование широко используется в промышленности (микроэлектроника, часовая промышленность и др.) для разделения тонких пластин поликора и сапфира, реже для разделения кремниевых шайб. При этом для осуществления дальнейшего механического разделения достаточно скрайбирования на глубину около трети от полной толщины разделяемой пластины.
Процессы микрообработки
Высокая степень автоматизации в последние годы позволила вновь на новой стадии использовать на практике такие процессы, как подгонка номиналов резисторов и пьезоэлементов, отжиг имплантированных покрытий на поверхности полупроводников, напыление тонких пленок, зонная очистка и выращивание кристаллов. Возможности многих процессов к настоящему моменту еще не до конца раскрыты.
Одним из направлений развития авиадвигателестроения является увеличение температуры газов перед турбиной. При этом, однако, происходит рост термомеханической напряженности лопаток газовых турбин и, как следствие, дальнейшее усложнение их конструкции. От надежности этих элементов двигателя в наибольшей степени зависит надежность и ресурс газотурбинных двигателей, и, соответственно, безопасность полетов. Эту проблему можно решить только путем разработки и внедрения качественно новых технологий, в том числе прошивки охлаждающих отверстий в лопатках. При этом во избежание горячих точек на поверхности лопаток плотность отверстий должна быть до ~200 отверстий/см?. К тому же, сложная структура жаропрочного кристаллического Niсплава, подобного CMSX4, требует процесса сверления, не меняющего его матрицу.
Сверление отверстий, которые являются каналами охлаждения компонентов турбинных двигателей, – один из наиболее распространенных процессов лазерной обработки. Однако до сих пор нет лазерных систем, позволяющих эффективно сверлить в турбинных лопатках из жаропрочного Niсплава высокоаспектные микроотверстия Ж100500 мкм и глубиной t
Ј 56 мм с малой величиной перегретой зоны (, где a » 1см 2 /с).
В случае обычного лазерного сверления (импульсы миллисекундного диапазона t имп
?0,5 мс, плотность мощности ~10 6 Вт/cм 2) на поверхности отверстия формируется переплавленный слой h
(рис. 1
) толщиной свыше 50 мкм, в котором изза быстрого затвердевания происходит формирование микротрещин, уменьшающих ресурс детали.
Эту проблему помогает решить использование коротких наносекундных импульсов с высокой плотностью мощности (10 8 10 9 Вт/cм 2) и более короткой длиной волны (выше порог поглощения излучения в плазме). Переплавленный слой значительно уменьшается, так как удаление материала происходит в основном в газообразной фазе . Для импульсов длительностью 10 8 сек пороговая плотность энергии для быстрого удаления материала составляет ~10 Дж/cм 2 при скорости абляции V сверл ? 1 мкм/импульс. Однако с увеличением толщины материала свыше 1 мм скорость абляции значительно падает (V сверл? 0,1 мкм/импульс) (рис. 2 ). Увеличение плотности энергии более чем на порядок лишь незначительно увеличивает скорость абляции.
Одним из механизмов, ограничивающих скорость абляции, является поглощение и рассеяние лазерного излучения в плазме, парах металла и капельках расплава. Другим ограничивающим фактором является более сильное ослабление лазерного излучения внутри глубокого канала одномерно расширяющейся плазмой в противоположность поверхностному двумерному случаю. В результате минимальная плотность энергии, необходимая для сверления образца толщиной ~0,4 мм, повышается до 30 Дж/cм 2 , а для образца толщиной ~0,9 мм до 100 Дж/cм 2 . Высокочастотному Nd:YAG лазеру (30 Вт, 10 кГц, 15 нс) требуется несколько секунд при плотности энергии ~500 Дж/cм 2 , чтобы просверлить отверстие Ж<30 мкм в 1,5 мм жаропрочном сплаве Inconel 718. При этом благодаря практически квазинепрерывной абляции наблюдается формирование значительного переплавленного слоя на боковых стенках отверстий и микротрещин, которые распространяются в основной материал, уменьшая ресурс детали. К тому же конусность отверстия может достигать значений 510 о (обычно конусность отверстия при сверлении Nd:YAG лазером оценивается как 0,02 t , где t толщина металла в мм).
Для сверления в турбинных лопатках глубоких отверстий Ж150350 мкм с той же эффективностью абляции требуются энергии в импульсе уже ~50100 мДж и, соответственно, кВтная средняя мощность лазера в TEM 00 моде. Другой подход – кольцевое сверление (trepanning drilling) – на порядок более длительный (по времени сравним с электроэрозионной прошивкой), хотя и требует менее мощного лазера.
Экспериментальная установка
Решение проблемы сверления глубоких микроотверстий представляется в использовании пачек относительно длинных (300500 нс) импульсов (длительность пачки несколько миллисекунд с интервалом между ними? 20мкс), с дополнительным профилированием их интенсивности в процессе сверления отверстия. Вопервых, относительно большая длительность импульсов позволяет обеспечить обработку материала при плотности энергии, более чем на порядок превосходящей плотность энергии для импульсов длительностью 1015 нс (при той же интенсивности), и, следовательно, сверление менее критично к толщине материала. Вовторых, имеется возможность повышения энергии импульса к концу пачки (профилирование) для увеличения эффективности удаления испаряемого материала. Втретьих, за счет использования пачек импульсов можно снизить среднюю мощность лазера до 1020 Вт, существенно уменьшив тем самым его стоимость.
Лазерная установка для сверления высокоаспектных микроотверстий включает в себя задающий генератор и двухпроходовый Nd:YAG усилитель (рис. 3 ). Задающий генератор – Nd:YAG лазер с непрерывной накачкой и акустооптическим затвором – генерирует 150 ё 550 нс импульсы с частотой повторения 3,5ё50 кГц со средней мощностью до 1 Вт. Двухпроходовый Nd:YAG усилитель вырезает из непрерывной последовательности импульсов и усиливает пачку импульсов длительностью 1 ё 6 мс (зависит от глубины отверстия). После усилителя энергия пачки импульсов достигает 1 Дж. Частота повторения пачек 10 Гц.
Фокусирующая линза f =150 мм обеспечивает на поверхности образца плотность мощности і10 8 Вт/cм 2 для диаметра пучка 100 мкм. Вспомогательные газы O 2 , N 2 или Ar (в зависимости от обрабатываемого материала) используются для выталкивания расплава из зоны обработки.
Результаты и обсуждения
Сверление микроотверстий (Ж100 мкм) проводилось на Ni сплаве IC10, Ni монокристалле DD6, конструкционной и нержавеющей сталях. На рис. 4 представлены результаты сверления микроотверстий в Ni сплаве IC10 (толщина 1,6 мм) с различными длительностями импульсов (энергия одиночного импульса E=18,5 мДж, частота повторения импульсов в пачке F=30 кГц, длительность пачки импульсов 0,9 мс, плотность энергии на образце 170 Дж/cм 2). Большая длительность импульсов дает лучшее качество отверстий. Для импульсов длительностью 550 нс толщина переплавленного слоя для большинства отверстий меньше чем 20 мкм, или даже 10 мкм (рис. 4 в ). Для более коротких импульсов существует больший разброс в толщине переплавленного слоя. Результат сверления сильно зависит от типа материала. Ni монокристалл DD6 показывает противоположный результат по сравнению с IC10: толщина переплавленного слоя отверстий, сделанных в DD6 с O 2 , намного тоньше, чем у отверстий, сделанных без газа.
Таблица 1
представляет результаты скорости сверления отверстий в материале IC10 импульсами с различной частотой повторения в пачке (энергия импульсов 18,5 мДж).
Как видно из таблицы 1, эффективность сверления возрастает с увеличением длительности импульса. При частоте повторения импульсов >30 кГц возрастает поглощение и рассеяние лазерного излучения в плазменном факеле, что снижает эффективность сверления. Как ожидалось, увеличение аспектного отношения приводит к резкому снижению скорости абляции, так как с увеличением глубины отверстия усиливается диссипация лазерного излучения. На большей глубине и при частоте повторения импульсов в пачке <30 кГц (граничная частота сильного поглощения излучения плазмой) плазма перестает подогревать расплав и большее его количество не удаляется, а застывает на боковых стенках отверстий.
Конусность отверстия также зависит от частоты повторения импульсов в пачке. Для частоты следования импульсов 50 кГц различие входных и выходных диаметров отверстий не более 10%, но при этом мы получаем снижение скорости абляции, а следовательно, и эффективности сверления.
иллюстрирует зависимость эффективности сверления микроотверстий от их глубины. Исследования проводились на образцах из конструкционной и нержавеющей стали толщиной до 5 мм. Скорость абляции, а следовательно, и эффективность сверления микроотверстий резко снижаются при увеличении толщины образца более 2 мм (рис. 5б ). В снижении скорости сверления с толщиной ключевую роль играет плазма и переотражение лазерного излучения от боковых стенок. Однако эффективность сверления и в этом случае более чем на два порядка превосходит эффективность сверления короткими 1015 нс импульсами той же интенсивности.
Улучшение геометрии микроотверстий
Дальнейшее повышение производительности сверления и улучшение формы отверстия (уменьшение воронки на входе, снижение конусности) возможно при программировании энергии в последовательных пачках импульсов (рис. 6 ) и преобразованиипространственного профиля пучка в зоне взаимодействия из гауссова в пучок с равномерным супергауссовым распределением или даже с интенсивностью излучения минимальной в центре пучка (рис. 7 ). Естественно, что при этом предпочтительно использовать лазеры с высоким качеством луча.
Пространственный профиль излучения в зоне обработки значительно влияет на скорость сверления и конусность микроотверстий, топологию поверхности материала около отверстия. При прямой фокусировке излучения(гауссов профиль) вокруг отверстия формируется значительный валик расплава и входная воронка, а типичные углы конусности для NiAl толщиной 2,5 мм составляют 0,3 о 0,5 о. При переносе изображения супергауссова пучка эти негативные эффекты резко снижаются (рис. 8 ), а конусность отверстия составляет?0,25 о.
Для образца из конструкционной стали толщиной 5 мм конусность оказалась 0,31 0 и 0,23 0 для прямой фокусировки и передачи изображения, соответственно. Фактически для частоты следования импульсов в пачке 30 кГц система передачи изображения уменьшает конусность отверстия в 1,52 раза (см. также таблицу 1 ). В тоже время пространственный профиль излучения практически не влиял на скорость сверления отверстия при толщинах образцов от 1 мм и выше. Заметное влияние наблюдалось лишь на малых толщинах 50 мкм и 100 мкм. В таблице 2 приведены данные по сверлению микроотверстий в фольге.
Таким образом, передача изображения на входную плоскость образца является эффективным способом для уменьшения конусности отверстий и минимизации входной воронки с валиком расплава.
Фокусирующая система
(«Световая» трубка)
Очень трудно сохранить небольшую конусность отверстия для большой толщины (56 мм) образца. Ограниченная фокальная длина фокусирующей линзы становится основной проблемой для достижения малой конусности. Возможным решением может быть использование фокусирующей системы, передающей заданный профиль лазерного луча с выходной апертуры усилителя с последующей фокусировкой на образец в виде длинной "световой" трубки, длина которой может быть гораздо больше, чем обычная конфокальная длина объектива. Для лазера с выходной апертурой ~ 45 мм разработана компактная афокальная система, которая создает "световую" трубку? 100 мкм и длиной? 3 мм, рис. 9 . Будущие эксперименты должны ответить за последствия такого подхода.
Специалисты разработали немало способов обработки бриллиантов для улучшения качеств этих камней. Самым проверенным способом повышения качества бриллиантов считается лазерное сверление.
Такой вид обработки алмазов впервые применили в коммерческой практике в 70-х годах прошлого века. Темные включения такие, как магнетиты, пирротины и углеродные включения не улучшают оптические характеристики камня и тем более не привлекают покупателей. В процессе лазерного сверления эти включения выжигают , растворяют с помощью азотной или серной кислот или же осветляют.
Лазерный луч специального аппарата, квантового генератора ИК-диапазона с длиной волн около 1060 нм, высверливает микроотверстие диаметром не более 20-60 мкм. 20 мкм равно 0,02 мм, такова толщина человеческого волоса. Сверление алмаза проводится на глубину не более 1,6 мм. Этот процесс занимает в среднем от 30 минут и более.
Существует способ осветления темных включений. Через отверстие, высверленное лазерным лучом, поступает воздух, под воздействием которого окраска включения может стать значительно светлее. Еще один способ осветления заключается в том, что в канал лазерного отверстия в вакуумной среде вводят реактив, который осветляет или полностью растворяет включение. Конечный результат зависит от химического состава данного включения.
При десятикратном увеличении под микроскопом или под лупой рассмотреть каналы лазерных отверстий нетрудно, даже если их запломбировали. Они имеют вид воронкообразных выемок на поверхности и прямых линий беловатого цвета внутри. Для заполнения каналов с недавнего времени используются такие вещества, как синтетическая смола или воск из-за высокого коэффициента преломления. После заполнения канала соответствующим веществом канал пломбируют. Хотя запломбированные отверстия менее заметны на поверхности и в меньшей степени подвержены загрязнению, в отраженном свете можно увидеть «кратер» в месте сверления. Выемки круглой формы на поверхности можно нащупать и острием иглы. Следует учитывать, что если в процессе сверления отверстия лазерный луч попал в зону сильного внутреннего напряжения, то вокруг канала образуются легко различимые трещинки напряжения и спайности.
При оценке подобных камней возникают трудности. Конечно, визуальные геммологические характеристики заметно улучшаются, но сверление создает искусственные дефекты в виде мелких трещинок.
Бриллианты относят к определенной группе чистоты с учетом их внешнего вида и наличия просверленных отверстий. Следует отметить, что целью лазерного сверления является не повышение степени чистоты бриллианта, а осветление темных включений. Это приводит к улучшению внешнего вида камня и больше привлекает покупателей.
В соответствующих сертификатах качества, накладных и других документах в обязательном порядке должна содержаться информация о результатах вмешательства со стороны человека и наличии отверстий лазерного сверления.
Недавно был разработан новый метод лазерной обработки алмазов, при котором канал не выводится на поверхность. Этот вид обработки подходит для алмазов с темными включениями, расположенными недалеко от поверхности. Но применение этого метода все же не гарантирует отсутствия новых трещин спайности и напряжения, «перьев» и микротрещин вокруг включений. Дефекты подобного рода, существовавшие до обработки, после применения данного метода могут усилиться. С другой стороны, новые трещинки, достигая поверхности, могут сыграть роль каналов. При введении кислот в эти каналы включения осветляются. Данный метод подходит не для всех камней, но бриллианты с темными включениями , находящимися около поверхности, с мелкими трещинками - идеальный материал для этого способа облагораживания.
Суть данного метода лазерной обработки заключается в том, что лазеры в пульсирующем режиме фокусируют точно на место включения. В результате процесса выделяется значительное количество тепла, которое способствует распространению трещинок до поверхности камня. Таким образом, отпадает необходимость сверлить канал с образованием воронки на поверхности. Растворитель, легко проникающий по новым трещинкам к включению, либо осветляет его, либо растворяет. Но и этот способ может привести к образованию ямок и каверн на поверхности камня с тем отличием, что их форма будет не такой идеально круглой, а размеры будут незначительно меньше.
Еще один метод лазерной обработки разработали израильские специалисты в начале 2000-х годов. Его назвали КМ(сокращение от слов«КидуахМеухад» ), что в переводе с иврита означает «специальное сверление». Способ, ставший популярным в Антверпене, применяется для осветления темных включений с микротрещинами с помощью кислоты при соблюдении особых условий. На ближайший к поверхности дефект направляют лазерный луч, в результате чего дефект распространяется до поверхности.
После лазерноговоздействия алмаз опускают в концентрированную кислоту и нагревают до высокой температуры под давлением. Благодаря созданным условиям, кислота проникает внутрь до включения и растворяет его.
Алмазы после обработки методом КМ можно идентифицировать по наличию голубовато-коричневатых оттенков в отраженном свете в местах искусственно созданных трещин , особенно при перекатывании камня. Чего нельзя сказать об алмазах, которые обрабатываются по традиционной технологии лазерного сверления с образованием заметных отверстий на поверхности. Более того, в алмазах, обработанных методом КМ, иногда можно заметить незначительные остатки веществачерноватого цвета в виде неправильных линий на поверхности трещин напряжения, которые образовались в процессе лазерного воздействия.
Вид механической обработки черных металлов путем резания отверстий вращающимися механизмами называют сверлением.
Различают простое и глубокое сверление.
Во втором случае глубина отверстия должна быть более 10 см., или размером вглубь более 5 исходных диаметров (5*d). При помощи сверл получают отверстия различной глубины и диаметра или многогранного сечения.
Обработка заготовки с целью ее сверления может производиться несколькими способами:
- Заготовка вращается, при этом одновременно производится продольная подача не вращающегося сверлильного инструмента;
- Заготовка не вращается, зафиксирована;
- Одновременное вращение заготовки и инструмента.
Все эти способы широко применяются на практике. Наибольший спрос на процесс глубокого сверления есть в следующих сферах: металлургия, производство труб, нефтегазовая и аэрокосмическая промышленность, выпуск плит теплообменников и бойлеров и многие другие. Наиболее часто применяют следующие детали с глубокими отверстиями: роторы, валы, оси, втулки, гильзы, цилиндры, бандажи, металлические скорлупы и многое другое.
Выполним полный комплекс работ по механической обработке металла:
Разновидности глубокого сверления
- По схеме удаления высверливаемого материала (стружки) различают: сплошное и кольцевое глубокое сверление. В первом варианте высверливаемый материал удаляется в виде стружки, во втором - часть кольцевой плоскости удаляется в виде стержня, остальное - также в виде стружки;
- По способу резания различают следующие виды:
- Одноштанговая система (система STS). Данный метод оптимально подходит для обработки деталей на высокопроизводительном или серийном производстве. Сложность процесса состоит в том, что требуется применять маслоприемник с многочисленными подающими шлангами, при этом заготовка вращается. Одноштанговая система считается самой эффективной для получения высококачественных отверстий;
- Эжекторная система. Метод глубокого сверления со средними параметрами выпуска заготовок. Позволяет осуществлять сверление на многофункциональных станках (например, токарных или сверлильных), систему дополняют стационарной или мобильной насосной станцией. Эжекторный метод подходит для получения отверстий d=20-60 мм. и глубиной до 1200 мм., не исключая получение прерывистых отверстий;
- Система сверления ружейными или трубчато-лопаточными сверлами с внутренней подачей смазочно-охлаждающего материала. Этот метод подходит для малых предприятий, где по условиям технологии требуется получить глубокие отверстия небольшого диаметра. Однорезцовые сверла легко встраиваются в универсальные станки. Резец изготавливается из твердых сплавов и по всей длине сверлильного стержня имеет V-образную канавку, угол кривизны которой может составлять от 110 до 1200 градусов. Рекомендуемый dотв.=35-40 мм., длиной до 50*d. При данном методе отпадает надобность проводить такие операции как зенкерование и развертывание.
- В зависимости от степени автоматизации управления процессом сверления различают глубокое сверление с автоматическим изменением одного или нескольких параметров режима (например, скорость вращения, подача смазочного материала).
Подача жидкости является обязательным этапом технологического процесса, так как:
- Обеспечивается эффективный отвод стружки из зоны резания по отводным каналам;
- Уменьшается сила трения между трущимися частями;
- Производится отвод тепла, которое образуется в процессе длительного сверления, обеспечивая тем самым сохранности сверла от прогорания;
- Осуществляется дополнительная обработка отверстия.
С увеличением глубины сверления возрастают трудности с обработкой отверстия.
Для глубокого сверления применяют специальный инструмент, оборудование и способы обработки.
Простые сверла и дрели для этого не подходят, так как не удастся достичь точности сверления по всему диаметру, заданной шероховатости поверхности, прямолинейность отверстия.
Важным параметром также является сохранение поверхности углубления с минимальным отклонением от округлости.
Применение традиционного инструмента делает процесс глубокого сверления низкопроизводительным, трудоемким, а в некоторых случаях (зависит от глубины отверстий) - невозможным.
На практике в машиностроительной сфере используют специализированное оборудование с технической оснасткой, с дополнительным применением специальных режущих и прочих вспомогательных инструментов.
Нередко требуются нестандартные приспособления для выполнения технологических приемов.
Особенности глубокого сверления
При глубоком сверлении очень важно соблюдать главные принципы технологии. Во-первых, производится подбор скорости вращения сверлильной части инструмента или оптимальная скорость резания (подачи свергла). Во-вторых, должно быть обеспечено нормальное дробление стружки, а также полный отвод отходов из канала. Важным моментом во время измельчения отходов сверления является сохранность режущей части инструмента, не должно быть повреждений сверла, образования на нем заусениц или иных дефектов. Далее, ключевым фактором качественной обработки поверхностей заготовок или деталей является эффективная и грамотная подача смазочно-охлаждающей жидкости.
Процесс сверления проходит с обязательной подачей смазочно-охлаждающей жидкости под давлением и с определенным расходом.
Для этого в системе работает насосное оборудование - маслонасосы или насосы для перекачки вязких жидкостей.
Производительность системы выбирается в соответствии с расходом жидкости и требуемым давлением подачи смазочного материала.
ВОЗМОЖНО ВАМ БУДЕТ ИНТЕРЕСНО

Трудовые отношения
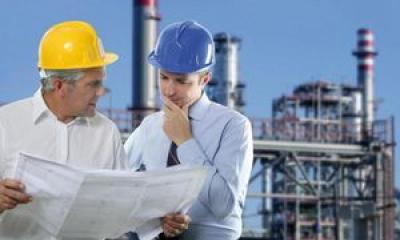
Должностная инструкция главного инженера, должностные обязанности главного инженера, образец должностной инструкции главного инженера Должностная инструкция главного инженера рэс
Открытие бизнеса
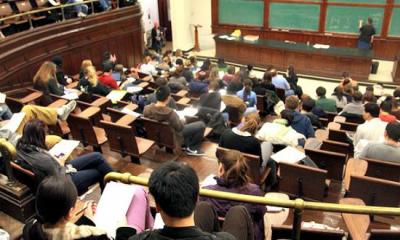
Где можно и где нельзя работать после туберкулеза Где можно работать после
Форекс
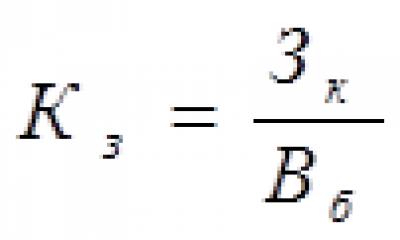