МОСКОВСКИЙ ГОСУДАРСТВЕННЫЙ
МАШИНОСТРОИТЕЛЬНЫЙ УНИВЕРСИТЕТ (МАМИ)
УНИВЕРСИТЕТ МАШИНОСТРОЕНИЯ
________________________________________________
Кафедра «Стандартизация, метрология и сертификация»
РАЗРАБОТКА ТЕХНОЛОГИЧЕСКОГО ПРОЦЕССА
ИЗГОТОВЛЕНИЯ ДЕТАЛИ
Методические указания
Москва 2015
В.И. Колчков
Различные виды механической обработки и примеры получения заготовок можно посмотреть .
Методические указания предназначены студентам машиностроительных специальностей для выполнения курсовой работы по дисциплине "Технология машиностроения отрасли".
Рассмотрен порядок выполнения и защиты курсовой работы, содержание и объем её графической части и пояснительной записки, приводится необходимый библиографический и справочный материал. Даны примеры расчета режимов обработки и оформления операционных эскизов.
1. Цель и задачи курсового проектирования
Курсовое проектирование является необходимым этапом практического применения студентом совокупности теоретических знаний для решения профессиональных технологических и конструкторских задач и подготовки к дипломному проектированию. Курсовое проектирование включает курсовую работу, целью которой является приобретение студентами практических навыков самостоятельного проектирования технологических процессов (ТП) изготовления типовых, средней сложности, содержащих не менее пяти основных операций, деталей отраслевого машиностроения. При этом решаются следующие задачи:
- анализ ТУ на изготовление детали;
- технологический контроль рабочего чертежа;
- выбор способа получения исходной заготовки;
- выбор технологических баз;
- разработка маршрута обработки, по каждой операции указать элементы СПИД. Схемы обработки можно посмотреть
- таблицы отражающие взаимосвязь шероховатости поверхности и точности обработки
- разработка операционной технологии, включая составление последовательности переходов в операции, расчет припусков и операционных размеров для ряда технологических переходов, выбор оборудования и технологической оснастки, расчет режимов обработки, расчет основного (машинного) времени, информация .
В курсовой работе возникает ряд задач, которые могут быть решены с применением ПК в системах автоматизированного проектирования (САПР). Наиболее типичные из них:
- оптимизация операционных режимов;
- составление программ для станков с ЧПУ;
- оптимальный раскрой листовых заготовок;
- технико-экономическое обоснование технологического процесса.
2. Тематика и объект курсовой работы
Темы курсовых работ (КР) соответствуют разработке прогрессивных ТП на детали заготовительного и механического производства машиностроения. Предусматривается возможность выполнения технологических, метрологических, конструкторских и других научных исследований.
Объектом курсовой работы служат чертежи деталей, являющиеся типовыми для машин или агрегатов. Это валы, втулки, зубчатые колеса, обечайки, днища, фланцы различных конструктивных разновидностей и др.
Курсовая работа состоит из пояснительной записки и графической части - листа маршрутно-операционной технологии.
3. Общее содержание и объем работы
В пояснительной записке студент должен разработать следующие вопросы:
- самостоятельно выбрать масштаб производства (индивидуальное, серийное, массовое), используя при этом представление о своей будущей специальности;
- провести анализ точности обработки детали и при необходимости уточнить требования чертежа, обозначение шероховатости и допусков формы можно посмотреть ; таблицы значений основных отклонений и допусков ;
- оценить технологичность детали;
- выбрать и обосновать способ получения заготовки;
- выбрать технологические базы и сопоставить их с конструкторскими и метрологическими базами, сделать заключение о соблюдении принципа единства баз;
- составить 2-3 размерные цепи (РЦ), определяющие наиболее точные (ответственные) размеры детали, сделать заключение о соблюдении принципа наикратчайшей размерной цепи;
- составить рациональный маршрут обработки детали;
- подробно описать не менее 3х различных операций: а) выбрать средства технологического оснащения (станки, приспособления, инструменты, в т.ч. контрольные); б) наметить число переходов на каждой операции;
- выбрать ответственную операцию и разработать элементы операционной технологии: а) для 2х-3х переходов провести расчёт режимов обработки; б) рассчитать припуски и технологические размеры; в) рассчитать основное (машинное) время;
- выполнить пояснения к технологическим эскизам и 2-3м приспособлениям.
Графическая часть представляет собой маршрутно-операционную карту, оформленную по установленной форме.
Подробно дается описание только основных формообразующих и отделочных операций, т.е. таких, при выполнении которых происходит изменение размеров, формы или качества отдельных поверхностей детали. Остальные операции, например, термическая, транспортная, балансировка, правка и другие только обозначаются в общем маршруте. Им дают порядковый номер, наименование и указывают их краткое содержание. Например: 10.Копировальная. Проверить размеры по чертежу; 15. Термическая. Закалить до HRC 35-45.
Студент разрабатывает единичный технологический процесс (ТП), взяв за основу типовой или групповой ТП.
4. Разработка и оформление пояснительной записки
4.1. Анализ технологичности детали
Понятие «технологичность детали» содержится в комплексе стандартов ЕСТПП, можно посмотреть также с.197-198 в /1/.
Технологичность детали – совокупность свойств и показателей, определяющих возможность её изготовления с наименьшими затратами при достижении требований к точности, указанных в чертеже. Технологичность детали можно предварительно оценить, сравнивая деталь с имеющимися аналогами. Окончательное решение о технологичности детали можно принять после разработки ТП и проведения технико-экономических расчётов.
Анализируя деталь, студент должен сопоставить её со стандартными унифицированными или оригинальными конструктивными решениями. При этом необходимо учитывать совокупность конструктивных элементов детали: образующих линий и поверхностей; взаимного расположения поверхностей, осей; наличие внутренних отверстий, полостей и др.; требования к точности; контролепригодность параметров точности и в итоге сделать предложения по методам и средствам формообразования поверхностей, а также методам и средствам контроля.
Оценка технологичности конструкции детали производится количественными и качественными показателями. Для количественной оценки технологичности конструкции изделия применяют показатели, предусмотренные ГОСТ 14.201-83. Основные из них: трудоемкость, материалоемкость, унификация элементов детали, требования к точности и качеству поверхностей.
Качественную оценку технологичности конструкции детали можно выразить словами. Необходимо дать предложения по улучшению технологичности детали и иллюстрировать их эскизами, схемами и привести в пояснительной записке.
4.2. Выбор вида заготовки и способа её получения
Правильный выбор заготовки – важнейший этап построения ТП изготовления изделия. Вид заготовки и способ её получения оказывает существенное влияние на характер технологического процесса, трудоемкость и экономичность обработки. Выбор способа получения заготовки непосредственно зависит от конструкции и материала детали, её размеров, требований к точности, объёма производства и других факторов. Исходя из необходимости максимального приближения формы и размеров заготовки к параметрам готовой детали, следует применять прогрессивные методы и средства получения заготовок. К ним например можно отнести литьё по выплавляемым моделям, литьё в оболочковые формы, литьё под давлением, штамповка в закрытых штампах, периодический прокат, профильный прокат и др. Прогрессивные виды получения заготовок обеспечивают снижение затрат на механическую обработку и повышают качество конечной продукции.
Способ получения заготовки можно выбрать, руководствуясь следующими рекомендациями:
- валы при разнице диаметров ступеней примерно до 10 мм целесообразно изготовлять из проката - круглой горячекатаной стали. При большей разнице заготовку следует выполнять ковкой в подкладных открытых штампах или горячей объемной штамповкой в закрепленных открытых штампах;
- заготовку чугунных втулок, фланцев, шестерен и других деталей, имеющих форму тел вращения с осевым отверстием, получают литьем.
- отверстия в чугунных деталей проливают, если его диаметр детали 30 мм и более.
- стальные детали диаметром до 60-70 мм изготавливают из горячекатаных прутков или заготовок, отрезанных от горячекатаного прутка, разрезку прутка на заготовки применяют, когда необходимый наружный диаметр прутка больше, чем отверстие в шпинделе токарного или револьверного станка;
- заготовки для деталей диаметром большем 60-70 мм, целесообразно получать ковкой, горячей объемной штамповкой с прошивкой отверстия диаметром 30 мм и более. В качестве заготовок также используются цельнотянутые трубы;
- заготовки для чугунных рычагов, вилок, кронштейнов, корпусных деталей получают литьем в т.ч. в земляные формы;
- заготовки для стальных деталей, указанных в предыдущем пункте, получают литьем или обычно свободной ковкой и штамповкой;
- фланцы сосудов и аппаратов изготавливают из поковок, штамповок, профильного проката, бандажных колец, плоские фланцы изготавливают из листового проката.
Широко применяются таже методы изготовления заготовок фланцев из листа: резка листа на прямые полосы с последующей их гибкой до необходимого радиуса, вырезка из листа секторов с последующей их сваркой /3/,с.103-106;
Обечайки, днища, элементы контактных устройств (тарелок), бортшайбы и другие изготавливают из листового проката (в отдельных случаях обечайки, бортшайбы, патрубки изготавливают из труб). Трубные решетки изготавливают из листового проката, поковок. Заготовки могут быть цельные и составные из 2, 3,4 частей, с последующей сваркой и 100% контролем.
Выбрав метод получения заготовки, необходимо нанести контур заготовки сплошными тонкими линиями на чертеж детали. В записке необходимо дать краткие сведения о заготовке и описание технологического способа её получения с указанием размеров и допусками на размеры.
При выборе технологических способов получения заготовок необходимо использовать /1/:
- заготовки отливки (с.116-134);
- кованые и штампованные заготовки (c.134-168);
- заготовки из проката (с.168-174);
- заготовки из листового проката можно найти в /3/, с.25-43.
4.3. Выбор технологических баз
Выбор технологических баз решается одновременно с выбором метода получения заготовки. Первые операции – создание чистовых баз для чего в заготовке предусматриваются черновые поверхности.
Выбор схемы базирования зависит от конструкторских и технологических требований. Выбранная схема в значительной степени предопределяет последовательность обработки, конструкцию приспособления, достижение заданной точности, производительность.
При разработке технологического процесса для каждой операции выбирается исходные (определенные) базы и проставляются исходные, (операционные) размеры. Это наиболее ответственный этап разработки технологического процесса и проектирования приспособлений.
При выборе баз руководствуются следующими рекомендациями: соблюдение принципа единства баз, т.е. по возможности обеспечивать совмещение технологической и конструкторской баз. Это значит задавать положение обрабатываемой поверхности по возможности теми же размерами, которые проставлены на чертеже детали.
Отступление от этих правил приводит к ужесточению допусков на исходные размеры, так как вместо конструкторских размеров приходится вводить технологические размеры, на которые назначаются меньшие допуски. Во-вторых, технологическая база, по возможности, должна обеспечивать неизменность положения заготовки в процессе её обработки, т.е. должна быть постоянной.
Способ базирования заготовки (детали) определяется, в основном, её формой. Используются типовые способы базирования заготовок, включающие в себя поверхности или совокупность поверхностей трех видов: плоскость, цилиндрическое отверстие и цилиндрическая наружная поверхность,
4.4. Разработка маршрутного технологического процесса
Построение маршрутной технологии зависит от конструктивно-технологических особенностей детали и требований точности.
Детали машин, как правило, получаются в результате механической обработки заготовок на металлорежущих станках /1/, с.224-452. Технология обработки деталей аппаратов приводится в литературе /3/.
При разработке технологического процесса изготовления детали, необходимо следовать рекомендациям и последовательности действий /1/, с.199-200:
- обработка базовых поверхностей;
- черновая обработка, при которой снимают наибольшую величину припуска;
- обработка тех поверхностей, которые не снижают жесткость обрабатываемой заготовки (детали);
- обработка поверхностей, которые не требуют высокой точности;
- отделочные операции следует выносить к концу технологического процесса обработки, за исключением тех случаев, когда поверхности служат базой для последующих операций;
- обрабатывать наибольшее количество поверхностей детали за одну установку и др.
После утверждения маршрутной технологии с руководителем-консультантом согласовываются и подробно разрабатываются операции с обоснованием выбора оборудования и технологической оснастки, обрабатывающего инструмента, межоперационных припусков, режимов обработки, расчеты основного (машинного) времени.
В дальнейшем в маршрутную технологию могут быть внесены необходимые уточнения.
Операционную технологию разрабатывают на основные операции, количество которых согласовывается с консультантом.
Проектирование операций связано с разработкой их структуры, выбором оборудования, приспособлений, с назначением режимов обработки, определением нормы времени.
ГОСТ 3.1702-79, ГОСТ З.170З-79. Примеры записи переходов приведены в табл.1.
В целях исключения текстовой записи вспомогательных переходов при базировании и закреплении следует применять условные обозначения опор и режимов, установленные стандартом /1/ , с.49-51.
В записке дается пояснение к выбору и методике построения операции. Исключается повторение полного содержания операций из маршрутно-операционной технологии в пояснительной записке.
Порядок переходов назначают так, чтобы обеспечить наибольшую экономичность и производительность выполнения операции.
4.5.1. Определение припусков и операционных размеров
Рекомендуется определить припуски общие и промежуточные на обработку одной поверхности: наружной поверхности вращения или отверстия. Общий припуск на обработку поверхности равен сумме промежуточных припусков по всем переходам обработки. Припуск на обработку поверхностей детали может быть назначен по соответствующим справочным таблицам, ГОСТам или на основе расчетно-аналитического метода определения припусков.
Расчет припусков на обработку и порядок определения предельных промежуточных размеров по технологическим переходам и окончательных размеров различных заготовок производится по справочнику технолога-машиностроителя /l/ , с.I75-I96.
4.5.2. Выбор технологического оборудования и технологической оснастки
Для условий единичного или мелкосерийного производства, обработку необходимо вести на универсальном оборудовании, стремясь к более полному использованию его возможностей. Чтобы избегать трудоемких переустановок крупногабаритных и тяжелых заготовок, черновую и чистовую обработку таких заготовок выполняют за одну операцию. Наиболее точные станки используют для чистовой и отделочной обработки, выделяемые в отдельные операции.
Типы металлорежущих станков и технические их характеристики приведены в справочнике /2/, с.5-65, оборудование для деталей аппаратов приведено в /3/.
Выбранное оборудование приводится в записке с краткой технологической характеристикой. Сведения о приспособлениях даны в литературе /2/, с.6З-80 и /3/, Сведения о режущем и другом обрабатывающем инструменте, а также измерительных средствах содержатся в /2/, с.111-259; 472-477 и /3/.
Режимы обработки и нормы времени рассчитываются и приводятся в записке для двух разнохарактерных переходов.
Режимы резания и основное время для механической обработки определяются в следующей последовательности:
- установить глубину резания;
- выбрать подачу инструмента;
- рассчитать скорость резания;
- проверить режимы резания по мощности станка;
- определить основное время на технологический переход.
При определении режимов обработки механического производства используют нормативные таблицы /2/, с.261-304, в заготовительном производстве режимы определяется по формулам для соответствующих типовых технологических процессов /3/.
Режимы обработки, полученные по расчетным формулам или назначенные по справочникам, корректируют по соответствующему оборудованию.
Основное (машинное) время (Т О) для отдельных видов работ приводится в справочной литературе. Для токарных, сверлильных работ Т О как каждый переход рассчитывается по формуле:
Где
Расчетная длина обрабатываемой поверхности, мм;
- число оборотов шпинделя в минуту;
- подача на один оборот шпинделя, мм/об;
- число проходов.
При сверлении припуск равен глубине резания. Так, например, при сверлении в сплошном материале на проход, глубина резания равна половине диаметра сверла.
Основное время на однослойную сварку 1 метра шва рассчитывается по формуле:
- сила тока, А;
- удельный вес наплавленного металла, г/мм 3 ;
- коэффициент наплавки, г/(А.ч);
- площадь поперечного сечения наплавленного металла, мм 2 ;
Для различных видов швов F определяется путем разделения его на простые геометрические фигуры и подсчета их площадей. При автоматической электросварке под слоем флюса по принятой скорости сварки (V с ) определяется скорость подачи электродной проволоки (V э )| обеспечивающая получение шва требуемого сечения F по формуле:
где F
э
- площадь поперечного сечения электродной проволоки, мм 2 .
При определении расчетной длины шва необходимо к длине по чертежу добавлять длину технологических заходных и выходных планок, равную 120 - 150 мм.
5. Оформление графической части
В действующем производстве оформление технологической документации предусматривает возможность снятия копий со всех видов документов и автоматизацию учета всех сведений, заносимых в каждую графy или строку документа. Поэтому стандартные формы бланков технологической документации по ЕСТПП предусматривают жесткий порядок расположения информации на поле каждой карты или ведомости и десятиразрядную структуру кодирования каждого заносимого в документ параметра или наименования.
Данная курсовая работа предназначена не для технологов, а для конструкторов, поэтому в учебных целях форма маршрутно-операционной карты значительно упрощена, а вся информация заносится в неё в естественном (раскодированном) виде. Это способствует максимальному сосредоточению внимания студентов на главном: на сущности разрабатываемого технологического процесса и на его взаимосвязи с конструкцией детали, её технологичностью, показателями качества. Упрощенная форма бланка маршрутно-операционной карты показана в приложении 1. В графе "Эскиз детали" выполняется рабочий чертеж детали с ТУ на изготовление. Общее число разделов, сечений, видов и размеров должно быть минимальным, но достаточным для изготовления и контроля детали. При нанесении контура детали, а также при выполнении операционных эскизов, масштаб изображения можно не соблюдать и не указывать. Необходимо лишь отчетливое изображение всех элементов детали, подлежащих обработке.
Для упрощения последующих записей операций и переходов рекомендуется на эскизе детали все обрабатываемые поверхности обозначить выносными линиями, на концах которых в окружностях диаметром 6-8 мм проставить их порядковые номера. Начало нумерации выбирается произвольно, последовательность нумерации должна производиться по часовой стрелке.
В правом угловом штампе карты студент проставляет номер своей группы, фамилию, наименование и материал детали, фамилию консультанта. В графе “Наименование и содержание операции” в последовательности сверху вниз заносятся названия всех операций полного маршрута изготовления заданной детали, а для основных операций подробно записываются все установы и переходы. При этом нумерацию операций ведут в виде трехразрядного числа через 5 или 10 единиц, нумерацию установов - прописными буквами русского алфавита, а переходов внутри каждого установа арабскими цифрами. При этом слово “Операция” не пишется.
Согласно технологическим стандартам ГОСТ 3.1702-79 и ГОСТ 3.1703-79 название операции формулируется в соответствии с используемым для её выполнения технологическим оборудованием. Наиболее употребимые операции для типовых технологических процессов перечислены в табл. 1.
Перечень типовых операций
Оборудование |
Операция |
Станки агрегатные Станки протяжные Станки долбёжные Станки вертикально-фрезерные Станки горизонтально-фрезерные Станки вертикально-сверлильные Станки горизонтально-расточные Станки токарно-винторезные Станки токарно-револьверные Станки токарные с программным управлением Станки токарно-карусельные Зуборезные полуавтоматы Полуавтоматы зубострогальные Полуавтоматы зубошевинговальные Станки плоскошлифовальные Станки бесцентрово-шлифовальные Станки круглошлифовальные Полуавтоматы хонинговальные Стол контролера Листогибочное Листоправильное Разметочное Оборудование для разделительной резки Развальцовочное Оборудование для очистки |
Агрегатная Протяжная Долбёжная Вертикально-фрезерная Горизонтально-фрезерная Вертикально-фрезерная Горизонтально-расточная Токарно-винторезная Токарно-револьверная Токарно-программная Токарно-карусельная Зубофрезерная Зубострогальная Зубошевинговальная Плоскошлифовальная Бесцентрово-шлифовальная Круглошлифовальная Хонинговальная Контрольная Разметка Разрезка Развальцовка |
При записи операции допускается применять обобщенное или конкретное наименование. Обобщенное наименование операций следует применять для операций, состоящих из нескольких переходов. Например, "Слесарная" - включающая выполнение таких переходов, как "Разметка", "Керновка", "Опиловка".
Основные операции записываются с полным указанием установов,
основных и вспомогательных переходов. Нумерация установов в каждой операции своя, переходы в каждом установе нумеруются, начиная с цифры 1. Например, "0С5. Заготовительная. Отрезать заготовку длиной 245 мм. 0I0. "Токарно-винторезная. Обработать деталь по чертежу, оставив припуски под шлифование. Установ А. Обточить правую сторону детали. 1-й переход. Закрепить заготовку в трехкулачковом патроне. 2 переход. Подрезать торец 5 и т.д. Последней должна быть контрольная операция с общим указанием:
"Проверить деталь по чертежу и техническим требованиям".
Примеры записи содержания переходов следует выполнять в соответствии с рекомендациями (табл.2).
Запись перехода
Сокращенная |
|
Гнуть деталь, выдерживая размеры 1 и 2 | Гнуть деталь согласно эскизу |
Нарезать резьбу, выдерживая размер 1 | Нарезать резьбу согласно чертежу |
Развернуть отверстие 2, выдерживая шероховатость | Развернуть отверстие 2 согласно чертежу |
Развальцевать поверхность 1, выдерживая размер 2 |
Развальцевать поверхность 1 согласно чертежу |
Установить деталь, выдерживая угол=15 градусам | Установить деталь согласно чертежу |
Сверлить отверстие, выдерживая размеры 1 и 2 | Сверлить отверстие согласно чертежу |
Опилить заготовку, выдерживая размеры 1, 2 и 3 |
Опилить заготовку согласно эскизу |
В графе "Технологический эскиз" заносят 5-7 операционных эскизов в порядке выполнения операций. Следует помнить, что операционный эскиз соответствует, строго говоря, не операции, а одному из её установов, т. е. на операционном эскизе изделие изображают в том виде, который оно приобретает после выполнения всех переходов данного останова. Таким образом, каждая операция может иллюстрироваться несколькими операционными эскизами (по числу установов).
На каждом операционном эскизе должно быть изображено:
- изделие (заготовка) с рабочими размерами и допусками, обрабатываемыми на данном установе;
- закрепление изделия на данном установе (схематично или условными символами);
- его основные и (или) вспомогательные движения (если они необходимы для обработки);
- шероховатость обработанных поверхностей. Обработанный контур выделяется утолщенной в 2-3 раза линией;
- все инструменты, необходимые для обработки изделия по данному установу, их закрепление (схематично или условно) и движения. Инструменты можно изображать упрощенно, не вырисовывая сложных контуров фасонных лезвий сверла или фрезы; инструменты следует располагать недалеко от обработанных поверхностей, но не вплотную к ним, чтобы инструмент не сливался с изделием.
Движения заготовки и инструмента указываются прямолинейной или дугообразной стрелкой и условным символом. На 2-3х эскизах должно быть показано схематичное (конструктивное) закрепление заготовки, а на остальных – условное. Примеры схематического и условного изображения наиболее употребительных приспособлений показаны в приложении 2.
Пользуясь свободой в выборе масштаба операционных эскизов, следует рационально использовать всю площадь отведенной для них графы маршрутно-операционной карты и наглядно изобразить отдельные обрабатываемые участки, избегая однообразного повторения контура всей детали на разных операциях. Расположение детали на каждом эскизе должно соответствовать её расположению на станке при выполнении соответствующей операции.
В графе "Оборудование" указывается тип и модель станка, пресса и другой единицы оборудования для каждой операции, приводятся его основные характеристики: мощность главного привода, диапазон рабочих чисел оборотов шпинделя и подач; максимальные размеры обрабатываемых изделий, максимальное усиление, развиваемого гидропрессом и так далее.
В графе "Приспособления" указываются приспособления универсального оборудования (станков): патроны, делительные головки, машинные тиски, магнитные столы, штампы, струбцины. Приспособления даются с указанием типов, ГОСТов, основных технических характеристик (габариты занимаемых изделий, рабочее усилие и так далее).
В графе "Инструменты" указываются типы стандартных режущих инструментов, материал режущей части, габаритные размеры (для сверл и фрез – диаметры), инструменты и приборы, применяемые для контроля.
В графах "Режим работ" указываются основные параметры режима резания, сварки, обработки для каждого перехода. Например, глубина резания t , мм; подача S , мм/об или мм/мин; скорость резания V , м/мин или м/с для лезвийной обработки. Для автоматической сварки под слоем флюса основными параметрами являются сила сварочного тока I , А, напряжение сварочной дуги U д , В, скорость сварки V с , м/ч, скорость подачи электродной проволоки V э , м/ч.
В графе "T o " даётся значение в минутах основного (машинного) расчетного времени для одного, двух переходов нескольких операций.
Заполнение маршрутно-операционной карты надо начинать с выполнения тонкими линиями операционных эскизов. После уточнения и одобрения их преподавателем эскизы оформляются окончательно, равномерно заполняя все поле отведенной для них графы.
Соответствующие эскизам установы и переходы должны располагаться слева от них. Если переходов очень много, то на карту допускается вносить лишь основные из них, остальные указать в пояснительной записке. Размещение переходов из соседнего установа рядом с операционным эскизом не допускается.
При оформлении пояснительной записки после каждого обращения к справочному материалу делать ссылку с указанием порядкового номера использованного источника, номеров таблиц, страниц или рисунков.
Записка заканчивается общим выводом, в котором оценивается эффективность разработанного варианта технологии, указывается её положительные и отрицательные стороны. В конце пояснительной записки приводится список использованной литературы с полным библиографическим описанием каждого источника.
Пример оформления пояснительной записки дан в приложении 3, а маршрутно-операционной карты – в приложении 4.
Текущий контроль за выполнением курсовой работы осуществляется преподавателем. При каждом посещении студента он делает отметку в кафедральном журнале о ходе работы и оценивает в процентах готовность маршрутно-операционной карты и пояснительной записки. По мере готовности работы каждый студент проходит индивидуальное собеседование у своего консультанта по проделанной работе. Защищенная работа сдаётся преподавателю с простановкой оценки в ведомость и зачетную книжку. Плановые сроки защиты курсовой работы – 11-12-я неделя семестра.
Литература
- Справочник технолога-машиностроителя. Под ред. А.Г. Косиловой и Р.К Мещерякова. М.:Машиностроение, 1985, т.1, 665 с.
- Справочник технолога-машиностроителя. Под ред.А.Г.Косиловой и Р.К.Мещерякова. М.:Машиностроение, 1985, т.2, 496 с.
- Никифоров А.Д., Беленький В.А., Поплавский Ю.В. Типовые технологические процессы изготовления аппаратов химических производств.М.: Машиностроение, 1979
Приложение 1
Маршрутно-операционная карта
Эскиз детали | Технические условия | ||||||||
МГУИЭ, кафедра ТМиМ |
|||||||||
Маршрутно-операционная карта |
|||||||||
Материал |
|||||||||
Группа, студент |
Подпись, дата |
||||||||
Консультант |
Подпись, дата |
||||||||
Наименование и содержание операции |
Технологический эскиз |
Оборудо-вание |
Приспосо-бления |
Инстру-мент |
Режим обработ-ки | ||||
Операция | Установка | Перехода | |||||||
* ширина колонки, мм
Приложение 2
Схематичное и условное изображение технологических эскизов
Способ установки |
Технологический эскиз |
Условное обозначение |
В трёхкулачковом самоцентри-рующем патроне с базированием по наружному диаметру подвижным люнетом, с поджатием вращающимся центром | ||
В кондукторе с неподвижной и подвижной призмами, с эксцентровым зажимом | ![]() |
|
Дорнование отверстий в трубной решетке. В подставке-опоре на столе пресса | ||
Двухпереходная штамповка днища. На вытяжную матрицу с фиксацией прижимным кольцом | ![]() |
Приложение 3
Пример оформления пояснительной записки
Разработка маршрута технологического процесса.
Технологический процесс изготовления детали включает в себя следующие операции:
Описание операций.
I. Токарная операция .
Установ А
Переходы
- Установить заготовку в обратных кулачках.
- Закрепить.
- Обработать поверхность 9 подрезным резцом 5 (два черновых хода и два чистовых) ГОСТ 18880-73 .
Схема снятия припуска.
Операцию осуществляем на токарно-револьверном станке 1365 ГОСТ 1770 .
Приложение 4
Пример оформления маршрутно-операционной карты
Наименование и содержание операции |
Технологический эскиз |
|||
Опе-рации | Уста-нова | Пере-хода | ||
Токарная
|
||||
А | 1 | Установить заготовку в обратных кулачках, закрепить | ||
2 | Обработать поверхность 1 | |||
3 | Обработать поверхность 10 | |||
4 | Обработать поверхность 7 | |||
5 | Обработать поверхность 11 | |||
6 | Обработать поверхность 3 | |||
7 | Обработать поверхность 2 | |||
8 | Расточить канавку 6 | |||
9 | Снять фаски 5 и 8 | |||
Б | 1 | Установить заготовку в оправку, закрепить | ||
2 | Обработать поверхность 4 | |||
3 | Обработать поверхность 12 |
Продолжение
Оборудование |
Приспо-собление |
Инструмент |
Режим обработки |
|
Станок токарно-револьверный 1365 ГОСТ 17-70 |
Оправка коническая ГОСТ 16211-70 | Резцы: |
Обработка поверхности подрезным резцом | |
Наибольший диаметр обрабатываемого прутка – 65 мм. | Фасонный резец | Черновое точение: |
1,6 | |
Наибольшая длина подачи прутка – 200 мм | Канавочный резец | Чистовое точение: |
2 | |
Наибольший диаметр изделия, устанавли-ваемого над стани-ной – 500 мм. | Расточный резец ГОСТ 18882-73 |
Обработка по-верхности рас-точным резцом |
0,06 | |
Частота вращения шпинделя 34 – 1500 об/мин. |
Подрезной резец ГОСТ 18880-73 |
Чистовое точение: |
0,04 | |
Продольная подача суппорта 0,09 – 2,7 мм/об. |
Фасонный резец | |||
Круговая подача револьверной головки 0,045-1,35 мм/об. | ||||
Габаритные размеры: длина – 5360 мм |
Приложение 5
Технические характеристики основных типов металлорежущих станков
а. Токарных:
Основные паспортные данные станка модели 16K20*
б. Фрезерных:
Основные паспортные данные станка модели 6Н13*
в. Сверлильных
Основные паспортные данные станка модели 2А135*
Введение |
1. Цель и задачи курсовой работы |
2. Тематика и объект курсовой работы |
3. Общее содержание и объем работы |
4. Разработка и оформление пояснительной записки |
4.1. Анализ технологичности детали |
4.2. Выбор вида заготовки и способа её получения |
4.3. Выбор технологических баз |
4.4. Разработка маршрутного технологического процесса |
4.5. Разработка операционной технологии |
4.5.1.Определение припусков и операционных размеров |
4.5.2. Выбор технологического оборудования и технологической оснастки |
4.5.3. Расчет режимов обработки и основного (машинного) времени |
5. Оформление графической части |
6. Контроль выполнения и защита курсовой работы |
Приложение 1. Маршрутно-операционная карта |
Приложение 2. Схематичное и условное изображение технологических эскизов |
Приложение 3. Пример оформления пояснительной записки |
Приложение 4. Пример оформление маршрутно-операционной карты |
Приложение 5. Технические характеристики основных типов металлорежущих станков |
Отправить свою хорошую работу в базу знаний просто. Используйте форму, расположенную ниже
Студенты, аспиранты, молодые ученые, использующие базу знаний в своей учебе и работе, будут вам очень благодарны.
Размещено на http://www.allbest.ru/
Министерство образования Московской области
ГБПОУ МО «Колледж» «Коломна»
КУРСОВОЙ ПРОЕКТ
Профессиональный модуль: Разработка технологических процессов изготовления деталей машин
Тема: Разработать технологический процесс изготовления детали
Данилин Д.Н.
Руководитель проекта
Кондюхов Д.П.
На курсовое проектирование по профессиональному модулю: Разработка технологических процессов изготовления деталей машин для студентов очной формы обучения III курса, группы 305 ТМ -13 _ _____Данилину Денису Николаев и чу __________________________________________
Тема: Разработать технологический процесс изготовления детали «Втулка»
Исходные данные:
1) Чертеж детали «Втулка» Д 49.78.49-1
2) Годовая программа выпуска N = 30000 штук _____________________
3) Работа двухсменная
Объем курсового проекта
Графическая часть:
1) Чертеж детали
2) Чертеж заготовки
3) Технологические наладки (карта наладки для станка с ЧПУ)
Пояснительная записка содержит 30-50 листов формата А4:
1) Титульный лист
2) Задание на курсовое проектирование
4) Введение
5) Технологический раздел (смотри на обороте)
6) Список используемой литературы
7) Приложения (смотри на обороте)
Дата выдачи задания «0 1 » октя бря 2015г.
Срок окончания «1 5 » июня 2016г.
Введение
1. Общий раздел
1.1 Назначение и конструкция детали
1.2 Анализ детали на технологичность
2. Технологический раздел
2.2 Анализ базового технологического процесса
Заключение
Список литературы
Введение
Машиностроение занимается производством машин и оборудования, различного рода механизмов для материального производства, науки, культуры, сферы услуг. Следовательно, продукция машиностроения потребляется всеми без исключения отраслями народного хозяйства.
Машиностроение - главная отрасль обрабатывающей промышленности. Именно эта отрасль отражает уровень научно-технического прогресса страны и определяет развитие других отраслей хозяйства. Современное машиностроение состоит из большого числа отраслей и производств. Предприятия отрасли тесно связаны между собой, а также с предприятиями других отраслей хозяйства. Машиностроение, как крупный потребитель металла имеет широкие связи, прежде всего, с черной металлургией. Территориальное сближение этих отраслей дает возможность металлургическим заводам использовать отходы машиностроения и специализироваться в соответствии с его потребностями. Машиностроение также тесно связанно с цветной металлургией, химической промышленностью и многими другими отраслями. Продукция машиностроения потребляется всеми, без исключения, отраслями народного хозяйства.
В настоящее время в структуре машиностроения насчитывается 19 самостоятельных отраслей, куда входят свыше 100 специализированных под отраслей и производств. К комплексным самостоятельным отраслям относятся: тяжелое, энергетическое и транспортное машиностроение; электротехническая промышленность; химическое и нефтяное машиностроение; станкостроение и инструментальная промышленность; приборостроение; тракторное и сельскохозяйственное машиностроение; машиностроение для легкой и пищевой промышленности и т.д.
Машиностроение является ведущей отраслью всей промышленности. Продукция предприятий машиностроения играет решающую роль в реализации достижений научно-технического прогресса во всех областях хозяйства.
Фрезерный станок с ЧПУ по металлу DMTG XD40A - аналог отеч е ственных станков моделей 6Т13Ф3 и 6Р13Ф3.
Обладает высокой скоростью вращения шпинделя, высокой скоростью обработки и быстрых перемещений. Вертикально-фрезерные станки по металлу с ЧПУ модели DMTG XD40A, разработанные с использованием последних мировых технологий, представляют новое поколение вертикально-фрезерных станков с ЧПУ, которые идеальны для мелкосерийных и единичных производств средних и небольших деталей.
На фрезерные станки с ЧПУ XD40A поставляется система ЧПУ "Siemens 0i-mate MC". Такие характеристики станка, высокоточная трех-осевая обработка, современное программирование (макро коды), графический дисплей, гарантируют превосходную точность исполнения команд и позволяет оператору быстро достичь желаемого результата. Сервопривода Siemens с цифровым управлением обеспечивают точные и быстрые перемещения по всем 3- м осям.
Большое количество операций, таких как фрезерование, растачивание, сверление, нарезание резьбы, можно осуществить за одну установку детали.
Стол и суппорт фрезерного станка по металлу с ЧПУ модели DMTG XD40A отливаются из специального высокопрочного чугуна, они компактны, имеют большую область загрузки, высокую жесткость и отличные антивибрационные характеристики, способные обеспечить самую высокую точность обработки на станках подобного типа.
Конструкция включает в себя мощный шпиндель и встроенную систему подачи СОЖ, что обеспечивает высокоскоростные режимы резания.
1. Общий раздел
1.1 Назначение и конструкция детали
Деталь «Втулка» Д 49.78.49-1 входит в гидротолкатель, который входит в крышку цилиндров дизель-генераторов 21-26 ДГ; 1-26 ДГ; 22 ДГМ.
Материал детали сталь ШХ 15 ГОСТ 801-78
Таблица 1 - Массовая доля элементов, % по ГОСТ 801-78
Массовая доля элементов, % |
С? кретич. точек |
|||||||||||||
? |
? |
? |
? |
|||||||||||
Сумма Cu и Ni ? 0,50% |
Таблица 2 - Механические свойства при комнатной температуре
Назначение - втулки плунжеров, нагнетательные клапаны, седла нагнетательных клапанов, корпусы распылителей, ролики толкателей, кулачки, накладные направляющие и другие детали, к которым предъявляются требования высокой твердости, износостойкости и компактной прочности, кольца подшипников с толщиной стенки до 14 мм, шарики диаметром до 150 мм, ролики диаметром до 23 мм.
1.2 Анализ детали на технологичность
Под технологичностью конструкции понимают ее соответствие к требованию минимальной трудоемкости и материалоемкостью.
Цель анализа на технологичность - выявление недостатков конструкции по сведениям, содержащимся в чертеже и технических требованиях, а также воз-можны улучшения технологичности рассматриваемой конструкции.
Отработка конструкции на технологичность - это комплекс мероприятий
по обеспечению необходимого уровня технологичности конструкции изделия по установленным показателям.
Качественная оценка технологичности производится по следующим параметрам:
- материал -ШХ 15 ГОСТ 801-78 - хорошо;
- форма и качество обрабатываемых поверхностей - хорошо;
- простановка размеров - хорошо;
- заготовка - прокат - допустимо.
Количественная оценка технологичности выполняется согласно ГОСТ 14.201-83
Таблица 3 - Количественный метод оценки технологичности конструкции
Наименование поверхности |
Количество поверхностей |
Количество унифицированных элементов |
Квалитет точности |
Параметры шероховатости, |
|
Наружная поверхность |
|||||
Внутренняя поверхность |
|||||
Коэффициент унификации конструктивных элементов детали:
,
где и - соответственно число унифицированных конструктивных элементов детали и общее.
Деталь технологична, если > 0,6.
Коэффициент использования материала:
где и - соответственно масса детали и заготовки, кг.
Деталь технологична, если Ким?0,65.
Коэффициент точности обработки:
,
Деталь технологична, если > 0,8.
Деталь технологична, если > 0,8.
Коэффициент шероховатости поверхности:
где - средняя шероховатость поверхности, определяемая в значениях параметра, мкм.
мкм
Кш = = 0,16
Деталь технологична, если Кш < 0,32.
Вывод: на основании выполненных расчетов можем считать деталь технологичной за исключением коэффициента использования материала, т.е. необходимо предложить более прогрессивный метод изготовления заготовки.
2. Технологический раздел
2.1 Определение типа производства
Тип производства представляет собой комплексную характеристику технических, организационных и экономических особенностей производства, обусловленных степенью специализации, сложностью и устойчивостью изготовляемой номенклатуры изделий, размером и повторяемостью выпуска продукции.
Основным показателем, характеризующим тип производства, является коэффициент закрепления операций, который определяется как отношение числа всех различных технологических операций, выполняемых или подлежащих выполнению в течение месяца, к числу рабочих мест.
В теории и практике различают три типа производства: единичное, серийное и массовое.
Единичное производство характеризуется малым объемом выпуска одинаковых изделий.
Серийное производство характеризуется производством нескольких однородных типов изделий, периодически повторяющимися партиями или сериями.
Массовое производство характеризуется большим объемом выпуска изделий, непрерывно изготовляемых продолжительное время, в течение которого на большинстве рабочих мест выполняется одна рабочая операция подетальной специализацией участков.
Для серийного производства определяем размер партии деталей:
==592штуки,
где N - годовая программа выпуска, штук;
б - количество дней запаса деталей на складе;
ф - количество рабочих дней в году.
Принимаем 600 штук.
2.2 Анализ базового технологического процесса
Таблица 4 - Базовый технологический процесс
№ операции |
Модель оборудования |
||
Отрезная |
|||
Контроль |
Стилоскоп СЛ-11А |
||
Токарно-винторезная |
|||
Плоскошлифовальная |
|||
Слесарная |
Верстак К3 7409А |
||
Токарная |
|||
Токарная |
п/а 1А240П-8 |
||
Токарно-винторезная |
|||
Токарно-винторезная |
|||
Токарно-винторезная |
|||
Калибровка |
|||
Вертикально-фрезерная |
|||
Слесарная |
|||
Контроль |
Плита ГОСТ 10905-86 |
||
Транспортирование |
Электрокар ЕП-011.2 |
||
Закалить 51…56 HRC |
|||
Транспортирование |
Электрокар ЕП-011.2 |
||
Доводочная |
Стол ТТ 7960-4174 |
||
Очистка ультразвуковая |
|||
Внутришлифовальная |
|||
Токарная с ЧПУ |
С ЧПУ 160НТ |
||
Круглошлифовальная |
|||
Доводочная |
Стол ТТ 7960-4174 |
||
Очистка ультразвуком |
|||
Доводочная |
Стол ТТ 7960-4174 |
||
Очистка ультразвуковая |
|||
Доводочная |
Стол ТТ 7906-4174 |
||
Очистка ультразвуковая |
|||
Контроль неразруш. магнитный |
|||
Контроль |
Плита ГОСТ 10905-86 |
||
Маркирование |
Электрограф |
2.3 Выбор заготовки и ее технико-экономическое обоснование
В машиностроении основным видом заготовки являются чугунные и стальные отливки из цветных металлов и сплавов, штамповки и всевозможные профили проката.
Для изготовления детали «Втулка» применяем 2 способа получения заготовки: из проката и методом горячей объемной штамповки.
Для выбора рационального метода получения заготовки производим экономическое сравнение их себестоимости.
Определение стоимости заготовки из проката
За основу расчета промежуточных припусков принимаем наружный диаметр детали? 32
Таблица 5 - Технологический маршрут обработки поверхности
Определяем припуски на обработку наружной поверхности:
2Z = 4,0 мм
Определяем припуски на подрезание торцевых поверхностей:
Z= 0,5 мм
Определяем промежуточные размеры обрабатываемых поверхностей согласно маршруту технологического процесса.
где - диаметр детали, мм;
2Z - припуск на обработку, мм.
= 32 + 4 = 36 мм
По ГОСТ 2590-2006 определяем размер горячекатаного проката обычной точности:
мм
Определяем общую длину заготовки:
,
где - длина детали, мм;
- припуск на подрезку торцов, мм.
= 27 + 2 · 0,5 = 28 мм, принимаем 28 мм.
Определяем объем заготовки с учетом плюсовых отклонений:
,
где р-3.14;
D- диаметр заготовки, см;
L- длина заготовки, см.
V= 29,1 см
Определяем массу заготовки по формуле:
,
где - плотность стали, кг/см3 .
m= 0,00785 · 29,1 = 0,23 кг
где - масса детали, кг;
- масса заготовки из проката, кг.
Ким = = 0,17
Определяем стоимость заготовки из проката:
где С- оптовые цены на сортовой материал, руб.;
С- 0,391 Ч 350 руб.
m- масса заготовки из проката, кг;
С- оптовые цены на лом и отходы углеродистых черных
металлов, руб.
С= 36,8 Ч 350 руб.
С= 136,85 · 0,23 12880 = 29,07 руб.
Определение стоимости заготовки изготовленной методом горячей объемной штамповки на горизонтально-ковочной машине (ГКМ)
Техническая характеристика заготовки:
Класс точности Т4;
Группа стали M3;
Степень сложности определяется путем вычисления отношения массы поковки к массе геометрической фигуры, в которую вписывается форма поковки
Определяем расчетную массу поковки:
где m- расчетная масса поковки, кг;
m- масса детали, кг;
К- расчетный коэффициент.
К= 1,7
m= 0,04 · l,7 = 0,068 кг
Определяем массу геометрической фигуры, в которую вписана форма поковки по формуле:
D- наибольший диаметр детали, см;
L- наибольшая длина детали, см;
Плотность стали кг/см3.
Определяем отношение, затем определяем степень сложности:
Степень сложности - С2
Определяем исходный индекс 10
Рисунок 1- Рабочий чертёж заготовки
Определяем основные припуски на размеры:
Таблица 6-Основные припуски на механическую обработку
Определяем размеры поковки, мм:
32+1,12 = 34,2; принимаем 34,5;
4+1,12 = 6,2; принимаем 6,5;
26+1,42 = 28,8; принимаем 29;
23+1,42 = 24,4; принимаем 24,5.
Определяем допускаемые отклонения размеров, мм:
Условно разбиваем фигуру заготовки на отдельные простые элементы, проставляем размеры с учетом плюсовых допусков:
Рисунок 2 - Элементы заготовки для определения объёма
Определяем объем заготовки штамповка на две фигуры:
где D - диаметр поверхности, см;
L - длина поверхности, см.
Определяем общий объем:
Vоб = 17,8+7,3 = 25,1 см
Определяем массу заготовки штамповка:
где с - плотность стали, кг/ см;
VЗШ - объем заготовки штамповка, см.
Определяем коэффициент использования материала:
где m- масса детали, кг;
m- масса заготовки штамповка, кг.
Определяем стоимость заготовки штамповка:
где С- оптовая цена за 1 кг горячештамповочных заготовок, руб.
С= 1,243 Ч 350=435,05 руб.
С- оптовые цены за 1 тонну на лом и отходы углеродистых черных металлов, руб.
С= 36,8 Ч 350 =12880 руб.
Определяем годовую экономию материала от выбранного варианта изготовления заготовки:
где m- масса заготовки прокат, кг;
m- масса заготовки штамповка, кг;
Э= (0,23- 0,2) Ч 30000 = 900 кг
Определяем экономический эффект по стоимости изготовления заготовки:
Э= (С- С)·N,
где С- стоимость заготовки штамповка, руб.;
С- стоимость заготовки прокат, руб.;
N - годовая программа выпуска, штук.
Э= (84,95 - 29,07) Ч 30000 = 2548587 руб.
Таблица 7 - Наиболее выгодный способ получения заготовки
Показатели |
Вид заготовки |
||
штамповка |
|||
1. Масса детали, кг |
|||
2. Масса заготовки, кг |
|||
3. Коэффициент использования материала |
|||
4. Стоимость заготовки, руб. |
|||
5. Экономический эффект от материала заготовки, кг |
|||
6. Экономический эффект от стоимости, руб. |
|||
7. Наиболее выгодный способ получения заготовки |
2.4 Разработка маршрута обработки детали
Таблица 8 - Маршрут обработки детали
операции |
Наименование и содержание операции |
Оборудование |
Режущий инструмент |
Приспособление |
|
Отрезная |
|||||
Зажим при станке |
|||||
2. Отрезать заготовку в размер 32-0,5 |
Пила 22570162 ГОСТ 4047-82 |
||||
Токарно -винторезная |
|||||
1. Установить деталь и закрепить |
Патрон 7100-0005 ГОСТ 2675-80 |
||||
2. Точить фаску 0,5х45? |
Резец 2102-0005 BK8 ГОСТ 18877-73 |
||||
Токарная |
|||||
1. Установить деталь и закрепить |
Патрон 7100-0005 ГОСТ 2675-80 |
||||
2. Подрезать торец в размер 28-0,5 |
Резец 2103-0057 Т15К6 ГОСТ 18879-73 |
||||
3. Центровать торец в размер 28-0,5 |
Сверло 2301-0060 ГОСТ 10903-77 |
||||
4. Сверлить отверстие Ш17,5Н9 |
Сверло 2300-7515 ГОСТ 10902-77 |
||||
5. Сверлить отверстие Ш3 |
Сверло 2300-7515 ГОСТ 10902-77 |
||||
6. Рассверлить фаску в размер 30? |
Сверло укороченное ТТ 2301-4232 |
||||
7. Сверлить отверстие предварительно Ш7,8и Ш17,5Н9 |
Сверло комбинированное ТТ 2310-4152 |
||||
8. Зенкеровать отверстие Ш7,8и Ш17,5Н9 и торец на длину 19,9 |
Зенковка КП 9347-589 |
||||
9. Развернуть отверстие Ш17,5Н9 |
Развертка ТТ 2363-4096 |
Расчет припусков (по округл енным нормативам)
Припуски определяются табличным и расчетно-аналитическим методом. шероховатость обработка деталь заготовка
Табличным методом определяются припуски на основании стандартов. Данный метод применяется в единичном и серийном производстве.
Таблица 9 - Табличный метод расчета припусков
Вид операции. |
Точность заготовки. |
Расчетные припуски, |
Расчетные размеры, |
Допуск,Тd, мм |
|||||
Наружная Поверхность |
|||||||||
Заготовка прокат |
|||||||||
Токарная черновая |
Проверка:
Zmax-Zmin= Тзаг.-Тдет
4,53 - 4 = 1,15 - 0,62
0,53мм = 0,53мм
Расчет режимов резания (на две операции по нормативам)
Разработка технологического процесса механической обработки заготовки обычно завершается установлением технологических норм времени для каждой операции.
Режимные параметры выбираются таким образом, чтобы была обеспечена наибольшая производительность труда при наименьшей себестоимости данной технологической операции. Эти условия удается выполнить при работе инструментом рациональной конструкции наивыгоднейшей геометрии с максимальным использованием всех эксплуатационных возможностей станка.
При определении режимов резания пользуемся табличным методом, как наиболее простым и дающим возможность ускорить разработку технологических процессов и сократить сроки подготовки к запуску изготовления данного изделия.
Расчёт режимов резания на операцию 020 - токарно-винторезная.
Переход 1
Установить деталь и закрепить;
Переход 2
Точить поверхность до Ш26,4h11 с подрезкой торца в размер
1.1) Выбор режущего инструмента:
Резец проходной отогнутый, материал режущей части Т15К6 ц=45°.
Выбираем номер эскиза резца 1, тип конструкции резца М.
Оценка в баллах 4.
Геометрические параметры лезвия инструментов: б = 6°; г = 10°; fo =1,2 мм.
где D - диаметр до обработки, мм;
d - диаметр после обработки, мм.
1.3) Определяем подачу S:
SТ = 0,60 мм/об;
Расчетная подача:
Sр=SТ*КS0*КS1*КS2*КS3*КS4*КS5*КS6=0,60*1,0*0,9*1,2*1,0*1,0*1,0*0,7=0,45 мм/об; (25)
где SТ - табличная подача, мм/об;
КS0 - поправочный коэффициент;
Корректируем подачу по паспортным данным:
Sn= 0,4 мм/об
1.4) Определяем скорость резания:
VТ= 200 м/мин;
Расчетная скорость резания:
Vр=VТ*Кv0*Кv1*Кv2*Кv3*Кv4*Кv5*Кv6=200*1,15*1,0*1,0*1,05*1,0*1,2*0,7=202,86м/мин;
где Vт - табличная скорость резания, м/мин;
Кv0 - поправочный коэффициент;
Кv1, Кv2, Кv3, Кv4, Кv5 - поправочные коэффициенты.
n= 1000* V ;
где V- расчетная скорость резания, м/мин;
D - диаметр до обработки, мм.
n = 1000*202,86 = 2019 мин -1
Корректируем частоту вращения по паспортным данным:
nn= 1000 мин -1
Vф= Dnn ,
где V - расчетная скорость резания, м/мин;
D - диаметр до обработки, мм;
nп - частота вращения шпинделя по паспорту, мин-1 .
Vф= 3,14* 32* 10 00 = 100,48 м/мин.
1.7) Определяем мощность, затрачиваемую на резание:
Nт=3,7 кВт.
где Nт-табличная мощность резания, кВт;
К- поправочный коэффициент на мощность резания.
Nр=3,7*1,0=3,7 кВт.
з -КПД станка.
3,7 кВт? 10*0,75=7,5 кВт.
1.8) Определяем основное время
Т0 = Lрез/(S*n)*I ,
Lрез.= L+ lвр.+ lпер,
lвр - врезание резца, мм;
lпер. - перебег резца, мм;
Sn - подача по паспорту, мм/об;
nп - частота вращения шпинделя по паспорту, мин-1;
i - количество проходов.
Lрез = 26,7+10=36,7
Т0 =36,7/0.4*1000=0.09мин.
Расчёт режимов резания на операцию 040 - вертикально-фрезерная.
Переход 1
Установить деталь и закрепить
Переход 2
Фрезеровать паз 3Н14 в размер 26Н14.
1) Нормирование основного времени.
1.1) Выбор режущего инструмента.
Фреза дисковая пазовая шириной 3Н14 и 26Н14
Материал режущей части Т5К10
Геометрические параметры лезвия инструмента:
б= 12° , г = 0 , ц = 60 , z=1.
1.2) Определяем глубину резания:
Определяем подачу на зуб:
SZ = 0,05 мм/зуб.
1.3) Расчетная подача:
SZP=SZT*КS1*КS2*КS3*КS4*КS5*КS6=0,05*1,0*1,25*1,1*1,0*0,5*1,0*=0,034мм/об,
где SZT - табличная подача;
КS1КS2, КS3, КS4, КS5, КS6 - поправочные коэффициенты.
Определяем подачу на 1 оборот фрезы:
Где SZ - расчетная подача;
Z - число зубьев.
SO = 0,034*5 = 0,17 мм/об.
1.4) Определяем скорость резания
VT = 187 м/мин.
Расчетная скорость резания:
VP=VT*Кv1*Кv2*Кv3*Кv4*Кv5*Кv6*Кv7=187*0,8*1,0*1,0*0,65*1,0*1,0*1,5=145,86 м/мин,
где VT - табличная скорость резания, м/мин;
Кv1, Кv2, Кv3, Кv4, Кv5, Кv6, Кv7- поправочные коэффициенты.
1.5) Определяем частоту вращения:
n = 1000* V ;
где р - 3,14;
V- расчетная скорость резания, м/мин;
D - диаметр до обработки, мм.
n = 1000*145,86 = 1451,63 мин -1
Корректируем частоту вращения по паспортным данным n= 800мин-1
1.6) Определяем фактическую скорость резания:
Vф = Dnn ;
V - расчетная скорость резания, м/мин;
D - диаметр до обработки, мм;
nп - частота вращения шпинделя по паспорту, мин-1.
Vф =3,14* 3 2* 800 = 80,4 м/мин.
1.7) Определяем минутную подачу:
где SO - подача на 1 оборот фрезы, мм/об;
SФ = 0,17*800 = 136 мм/мин.
Корректируем минутную подачу по паспортным данным:
SMn = 133,3 мм/мин.
Определяем фактическую подачу на зуб:
SZCC = SMn / Z*nn ;
где SMn - минутная подачу по паспортным данным;
Z - число зубьев;
nn - частота вращения шпинделя по паспорту, мин-1.
SZCC = 133,3 = 0,03 мм/зуб.
1.8) Определяем мощность, затрачиваемую на резание:
NT = 9,1 кВт
Расчетная мощность, затрачиваемая на резание:
NP= NT*КN1*КN2*КN3*КN4*КN5*КN6*КN7*КN8 = 9,1*1,0*1,0*1,0*0,65*1,0*1,0*1,5*0,5 = 4,4 кВт,
где NT - мощность, затрачиваемую на резание, кВт;
КN1, КN2, КN3, КN4, КN5, КN6, КN7, КN8 - поправочные коэффициенты.
Проверяем станок по мощности:
где Nдв- мощность двигателя, кВт;
з -КПД станка.
4,4 кВт? 11*0,8=8,8 кВт.
В связи с тем, что Nр меньше допустимой, то обработка возможна на всех переходах.
1.9) Определяем основное время:
Т0 = Lрез/SMn*i ,
где Lрез. - длина рабочего хода инструмента, мм;
Lрез.= L+ евр.+ епер.+ еподв.;
где L - длина обрабатываемой поверхности, мм;
евр., епер., еподв - врезание, перебег, подвод, мм;
SMn - минутная подачу по паспортным данным;
i - количество проходов.
Lрез = 4+11=15
Т0 =15/133,3*1=0.11 мин.
Таблица 10 - Сводная таблица режимов резания
№ операции |
Наименование и содержание операции |
Модель станка |
||||||
Токарно-винторезная |
||||||||
1.Установить деталь и закрепить |
||||||||
2.Точить поверхность Ш26,4h11 с подрезкой торца в размер 4,1 |
||||||||
Вертикально-фрезерная |
||||||||
1. Установить деталь и закрепить |
||||||||
2.Фрезеровать паз 3Н14 в размер 26Н14 |
Расчет норм времени (на две операции по таблицам)
Расчёт норм времени на операцию 020 Токарно-винторезная
1) Определяем основное время:
Тосн = 0,09 мин.
Твсп=Туст=Тв.оп+Тизм,
где Туст - время на установку детали, мин.;
Тв.оп - время, связанное с операцией, мин.;
Тизм - время на контрольные измерения, мин.
Туст=0,10 мин.
Тв.оп=0,10+0,08+0,06+0,03= 0,28 мин.;
Тизм=0,08 мин.;
Твсп=0,10+0,28+0,08= 0,46 мин.
Топер=Тосн+Твсп= 0,09+0,46= 0,55 мин.
4) Определяем штучное время
Тшт=(Т0+Ктв*ТТвсп)*(1+(аобсл+аотл)/100)
где Т0-основное время, мин.;
Ктв- коэффициент на вспомогательное время;
Тшт= (0,09+0,76*0,46)*(1+8/100) = 0,475 мин.
Нормирование подготовительно-заключительного времени:
Позиция 1,2,3,4,5,13,16,25,34.
Тпз= 4+9+2+2+4+6,8+0,8+0,3=28,9 мин. (46)
5) Определяем штучно-калькуляционное время
Тшт.к.=Тшт+Тпз/n,
где Тшт- штучное время, мин.;
Тпз- подготовительно-заключительное время, мин.;
n- количество деталей в партии, штук.
Тшт.к=0,475+28,9/600=0,523 мин.
Расчёт норм времени на операцию 040 Вертикально-фрезерная
1) Определяем основное время:
Тосн=0,11мин.
2) Нормирование вспомогательного времени:
Твсп=Туст=Тв.оп+Тизм,
где Туст - время на установку детали, мин.;
Тв.оп - время связанное с операцией, мин.;
Тизм - время на контрольные измерения, мин.
Туст=0,09мин.
Тв.оп=0,12+0,06+0,05=0,23мин.
Тизм=0,06+0,06=0,12 мин.
Твсп=0,09+0,23+0,12=0,44 мин.
3) Определяем оперативное время:
Топер=Тосн+Твсп=0,11+0,44=0,55 мин.
4) Определяем штучное время:
Тшт=(Т0+Ктв*ТТвсп)*(1+(аобсл+аотл)/100))
где Т0-основное время, мин.;
Ктв- коэффициент на вспомогательное время;
(аобсл + аотл) - время на обслуживание рабочего места, отдых и личные потребности.
Тшт= (0,11+0,76*0,44)*(1+8/100)=0,479 мин.
5) Нормирование подготовительно-заключительного времени:
Позиция 1,2,3,4,7,15,21,22,31.
Тпз=4+10+2+2+2+0,8+0,3+0,15+0,2=29,45мин. (51)
6) Определяем штучно-калькуляционное время
Тшт.к.=Тшт+(Тпз/n) , (52)
где Тшт- штучное время мин;
Тпз- подготовительно-заключительное время мин;
n- количество деталей в партии шт.
Тшт.к=0,479+29,45/600=0,528 мин.
Таблица 11 - Сводная таблица норм времени
2.5 Экономическое обоснование принятого варианта техпроцесса
Все расчеты выполняются с использованием цен и тарифных ставок, действующих на предприятии.
Расчет себестоимости производится на две операции: 020 и 040
Токарно-винторезная и вертикально-фрезерная. При оценке эффективности рассчитываются следующие технико-экономические показатели:
Основная заработная плата;
Затраты на силовую электроэнергию;
Расходы по эксплуатации режущих инструментов.
Определяем основную заработную плату производственных рабочих:
Зоп=Тст*К*Тшт/60,
где Тст- часовая тарифная ставка станочника 1 разряда в рублях;
Тст=74 руб.
К- тарифный коэффициент, 1,44;
Тшт- норма штучного времени на операцию, мин.
Зоп=Зоп.ток+Зоп.фрез
Зоп.ток= 74*1,44*0,475/60=0,84 руб.
Зоп.фрез= 74*1,44*0,479/60=0,85 руб.
Зоп.разр.= 0,84+0,85=1,69 руб.
Зоп.ток=74*1,44*0,475*1,05/60=0,88 руб.
Зоп.фрез=74*1,44*0,479*1,05/60=0,90 руб.
Зоп.баз=0,88+0,90=1,78 руб.
2) Определяем расходы на заработную плату:
Ф=Зоп.*Кпрем.*Котп.*Ксоц,.
где Кпрем.- коэффициент премирования = 1,2;
Котп- коэффициент учитывающий оплату отпусков = 1,2;
Ксоц- коэффициент учитывающий отчисления на социальные страхования = 1,077.
Разработанный технологический процесс:
Фразр.= 1,69*1,2*1,2*1,077=2,63 руб.
Базовый технологический процесс:
Фбаз.=1,78*1,2*1,2*1,077=2,76 руб.
3) Определяем расходы силовой электроэнергии:
Э=Сэ*Ng* з м*Тосн/60* з с* з д,
где Сэ - стоимость 1кВт/ч. = 4,54 руб.;
Ng - установленная мощность эл. двигателя станка = 7,5 кВт/час.;
з м-коэффициент загруженности двигателя станка по мощности 0,5;
Тосн - основное время на операцию, мин;
з с - коэффициент потерь в сети =0,96;
з д - КПД электродвигателя.
Разработанный технологический процесс:
Эток=4,54*7,5*0,5*0,09/60*0,96*0,75=0,03 руб.
Эфрез=4,54*8,8*0,5*0,11/60*0,96*0,8=0,05 руб.
Эразр=0,03+0,05=0,08руб.
Базовый технологический процесс:
Эток=4,54*7,5*0,5*0,09/60*0,96*0,75*1,05=0,04 руб.
Эфрез=4,54*8,8*0,5*0,11/60*0,96*0,8*1,05=0,05 руб.
Эбаз.=0,04+0,05=0,09 руб.
4) Определяем расходы на эксплуатацию режущего инструмента:
Иоп.=Смин.*Тосн,
где Смин - стоимость эксплуатации режущего инструмента на одну станко-минуту (резец 2,55 ст/мин.; фреза дисковая 30,42 ст/мин.)
Разработанный технологический процесс:
Иоп.ток=2,55*0,09=0,23 руб.
Иоп.фрез=30,42*0,11=3,35 руб.
Иоп.разр.=0,23+3,35=3,58 руб.
Базовый технологический процесс:
Иоп.ток=2,55*0,09*1,05=0,24 руб.
Иоп.фрез=30,42*0,11*1,05=3,51 руб.
Иоп.баз.=0,24+3,51=3,75 руб.
5) Определяем затраты:
Эф= Ф+Э+Иоп.
Разработанный технологический процесс:
Эф.разр.=2,63+0,08+3,58=6,29 руб.
Базовый технологический процесс:
Эф.баз.=2,76+0,09+3,75=6,6 руб.
6) Определяем годовой экономический эффект:
Э=(Эф.баз.- Эф.разр.)*N,
где N- годовая программа выпуска, штук.
Э=(6,6- 6,29)*30000=9300 руб.
Из расчетов видно, что затраты в разработанном технологическом процессе меньше, чем в базовом.
2.6 Охрана труда и окружающей среды. Мероприятия по безопасности жизнедеятельности
Охрана труда представляет собой систему законодательных актов и соответствующих им экономических, технических, гигиенических и организационных мероприятий, обеспечивающих безопасность сохранения здоровья и работоспособность человека в процессе труда. Составными частями охраны руда является трудовое законодательство, техника безопасности и производственная санитария.
Задачами трудового законодательства являются регламентация правовых норм, непосредственно направленных на обеспечение здоровых и безопасных условий труда, норм, регулирующих организацию и планирование труда.
Задачей охраны окружающей среды является обеспечение равновесия человеческого общества и окружающей среды, сохранение и рациональное использование природных ресурсов.
Проблема окружающей среды и рационального использования природных ресурсов является одной из наиболее актуальных общечеловеческих проблем, так как от ее решения зависит жизнь на земле, здоровье и благосостояние человечества. Вокруг предприятия предусмотрена санитарно-защитная зона шириной 50 м. Эта зона озеленена и благоустроена. Зеленые насаждения обогащают воздух кислородом, поглощают углекислый газ, шум, очищают воздух от пыли и регулируют микроклимат. Загрязнение атмосферного воздуха и водоемов находся в пределах допустимых норм, так как с этой целью предусмотрены очистные сооружения.
После промывки оборудования и инвентаря вода, содержащая загрязнения сливается через отверстия в полу, которые связаны с канализацией, сточные воды обрабатываются на очистных сооружениях, а образовавшиеся осадки используются для реализации как удобрения в сельском хозяйстве. Очищенная вода на предприятии используется повторно, но только в бытовых целях.
Планировка и устройство территории предприятия предусматривает отвод атмосферных осадков от зданий к водостокам; хозяйственное и пожарное водоснабжение и канализацию. На территории устанавливают указатели проездов и проходов, специальные надписи и знаки мест стоянок. В производственных помещениях поддерживаются нормальные санитарно-гигиенические условия (, влажность, давление и чистота воздуха). Производственные, складские, вспомогательные, подсобные и бытовые помещения, лестничные площадки, проходы и рабочие места содержатся в чистоте, не допуская загромождения рабочих мест и проходов оборудованием, материалами и запасными частями.
Поверхность пола, стен и потолков является гладкой, удобной для очистки и удовлетворяющей гигиеническим и эксплуатационным требованиям. Для обеспечения безопасных условий труда, работоспособности человека, окружающая его на производстве воздушная среда должна соответствовать установленным санитарно-гигиеническим нормативам. В основу нормирования положены условия, при которых организм человека сохраняет нормальный тепловой баланс, то есть за счет физиологических процессов осуществляется терморегуляция, обеспечивающая сохранение постоянной температуры тела путем теплового обмена с внешней средой.
Средства индивидуальной защиты, обычно выполняющие роль дополнительного мероприятия, являются основным фактором предупреждения производственного травматизма. Они нужны для того, чтобы обеспечить комфортную работу работникам. В состав средств индивидуальной защиты входят: спецодежда, резиновые сапоги и технические перчатки, защитные каски, шлемы, наушники, защитные очки, тулупы, жилеты.
Перед запуском все станции, защитные приспособления должны функционировать. Руководство по эксплуатации станции необходимо хранить постоянно на месте производства. Дополнительно к инструкции по эксплуатации необходимо подготовить общепринятые, а также личные правила по предупреждению несчастных случаев и по защите окружающей среды. На станции может работать только обученный и проинструктированный персонал. Ни в коем случае не
проделывать изменения программы на электронных регуляторах. Только проинструктированному персоналу разрешено проводить действия управления.
При всех неполадках на станции и, которые указывают на электрические или механические дефекты, может ремонтировать только уполномоченный специалист. Запрещено проводить работы на частях под напряжением. Работы по электрическому обеспечению разрешено выполнять только специалисту электрику.
Комплексная механизация и автоматизация промышленности сопровождается значительным увеличением количества единиц электрооборудования. Электробезопасность - это система организационных и технических мероприятий и средств, обеспечивающих защиту от вредного и опасного воздействия электрического тока, электрической дуги, электромагнитного поля и статического электричества. Все производственные помещения по степени опасности поражения людей электрическим током разделяются на три группы: без повышенной опасности, с повышенной опасностью и слабо опасные.
При повреждении изоляции нетоковедущей части электроустановок оказывается под напряжением. Основными техническими мерами защиты людей от поражения электрическим током в этом случае являются защитные заземления, зануление и защитные отключения.
Ограждающие средства защиты предназначены для временного или постоянного ограждения токоведущих частей, для предупреждения ошибочных операций, временного заземления токоведущих частей с целью устранения опасности поражения.
Важное значение имеет профессиональная подготовка рабочих и инженерно-технических работников, чёткое знание ими всех организационных и технических мероприятий по обеспечению безопасности при работе с электрооборудованием.
Не допускается к работе персонал, который не прошёл инструктаж по технике безопасности, в алкогольном и наркотическом опьянении, дети до 18 лет.
Заключение
В процессе курсового проекта мной была проделана значительная исследовательская и учебно-методическая работа по совершенствованию технологического процесса обработки детали «Втулка», а так же разработан комплект документов на обработку.
Рассмотрел два вида изготовления заготовок: прокат и штамповка. По результатам расчетов получил, что заготовка-прокат более экономична по расходу материала и коэффициенту использования материала и дешевле по стоимости. Экономический эффект от выбранного вида изготовления заготовки составляет 2548587 рублей при годовой программе выпуска детали 30000 штук.
При разработке нового варианта технологического процесса я использовал концентрацию операций с целью повышения загрузки оборудования и произвел замену станков на более производительные, что позволило уменьшить затраты на заработную плату производительных рабочих, а это в свою очередь снизило себестоимость изготовления детали.
При разработке операций выполняющихся на токарно-винторезном 16К20 и вертикально-фрезерном 6Н11станках мной вычерчены карты наладки, наладка инструментальная, а также разработан комплект документов на обработку детали.
Список литературы
1 Добрыднев И.С. Курсовое проектирование по предмету «Технология машиностроения». М. Машиностроение. 1985.
2 Босинзон М.А. Современные системы ЧПУ и их эксплуатация. М. Академия. 2006.
3 Общемашиностроительные нормативы времени и режимов резания для нормирования работ, выполняемых на универсальных и многоцелевых станках с ЧПУ.В 2-х частях. Т1,Т.2. М. Экономика 1990
4 Локтев А.Д. Общемашиностроительные нормативы режимов резания. Справочник. В 2-х частях. Т1,Т.2. Машиностроение. 1991
6 Зубченко А.С. Марочник сталей и сплавов. 2-е издание. М. Машиностроение. 2003.
7 ГОСТ 7505-89. Поковки стальные штампованные. М. Машиностроение. 1990.
8 ГОСТ 14.209-85.
9 Стандарт СЭВ 144-75.
10 Нефедов Н.А., Осипов К.А. Сборник задач и примеров по резанию металлов и режущему инструменту. М. Машиностроение. 1990.
11 Панов А.А. Обработка металлов резанием. Справочник технолога. М. Машиностроение. 1988.
12 Под редакцией Косиловой А.Г., Мещерякова Р.К. Справочник технолога-машиностроителя. В 2-х частях. Т1, 2. М. Машиностроение. 1985.
13 Трудовой кодекс Российской Федерации от 10.10.2008.
14 Девисилов В.А. Охрана труда М. Форум-Инфра-М . 2003.
Размещено на Allbest.ru
...Подобные документы
Анализ формы точности, шероховатости, размеров материала и обработки детали, а также характера нагружения. Определение технологического маршрута обработки поверхности детали в зависимости от точности размеров и шероховатости поверхностей детали.
курсовая работа , добавлен 25.09.2012
Проведение анализа технологичности и разработка технологического процесса изготовления детали "Корпус разъема". Обоснование метода получения заготовки и выбор способов обработки поверхностей детали. Расчет технологического маршрута изготовления детали.
курсовая работа , добавлен 05.11.2011
Выбор способа получения заготовки. Анализ технологичности конструкции детали. Выбор методов обработки поверхности заготовки, схем базирования заготовки. Расчет припусков, промежуточных технологических размеров. Проектирование специальной оснастки.
курсовая работа , добавлен 04.02.2014
Разработка энергосберегающего технологического процесса изготовления детали. Методы оценки технологичности изделия. Выбор способа получения заготовки, ее технико-экономический анализ. Технология токарной и фрезовой обработки, контроль качества изделия.
курсовая работа , добавлен 23.06.2009
Анализ конструкции и размерный анализ детали типа "шатун". Химический состав и механические свойства стали. Резка, фрезерование, шлифование поверхности детали. Анализ технологичности конструкции шатуна, коэффициент точности обработки и шероховатости.
контрольная работа , добавлен 08.12.2013
Разработка технологического процесса изготовления корпуса. Выбор заготовки и способа её получения. Анализ технологичности конструкции детали. Разработка структуры и маршрута обработки детали. Выбор режимов резания, средств измерения и контроля.
дипломная работа , добавлен 09.12.2016
Анализ эксплуатационных свойств и технологичности конструкции детали. Разработка технологического процесса обработки детали, маршрут операций, расчет погрешностей базирования, рациональные режимы резания и нормы времени, расчет точности обработки.
курсовая работа , добавлен 24.10.2009
Анализ технологичности конструкции детали. Выбор стратегии производства и технологического оснащения. Используемое оборудование, схема базирования заготовки. Приборы контроля точности обработки поверхности детали "вал". Калибр-пробки, скобы, отверстия.
контрольная работа , добавлен 13.11.2013
Анализ служебного назначения и технологичности детали. Выбор способа получения заготовки. Обоснование схем базирования и установки. Разработка технологического маршрута обработки детали типа "вал". Расчет режимов резания и норм времени по операциям.
курсовая работа , добавлен 15.07.2012
Описание конструкции детали "Серьга", анализ ее технологичности. Выбор и технико-экономическое обоснование метода получения заготовки. Расчет и назначение промежуточных припусков на механическую обработку. Расчет и выбор режимов резания при обработке.
Технологический процесс (ТП) - это установленная соответствующими технологическими документами последовательность действий, взаимосвязанных между собой и направленных на объект процесса с целью получения требуемого результата. Технологические процессы состоят из рабочих операций, которые могут быть связаны друг с другом с помощью технологических переходов.
Принято различать три вида технологических процессов (ТП):
- единичный
- типовой
- групповой
Каждый ТП разрабатывается при подготовке производства изделий после отработки конструкции на технологичность (ГОСТ 14.201-83). Технологический процесс разрабатывается для изготовления нового изделия или совершенствования выпускаемого (в соответствии с достижениями науки и техники).
Основой для нового ТП обычно служит имеющийся типовой или групповой технологический процесс. Если таковые отсутствуют, то за основу берут действующие единичные технологические процессы изготовления аналогичных изделий.
Работа по разработке технологических процессов начинается с анализа исходных данных для разработки ТП (первый этап). Необходимо по имеющимся сведениям о программе выпуска и конструкторской документации на изделие ознакомиться с его назначением и конструкцией, требованиями к изготовлению и эксплуатации.
Затем последовательно выбирают действующий типовой, групповой ТП или аналог единичного процесса. Формируют технологический код изделия по технологическому классификатору, обрабатываемое изделие относится к соответствующей классификационной группе на основе кода и к действующему единичному или типовому процессу.
По классификатору заготовок, методике расчета и технико-экономической оценки выбора заготовок, стандартам и техническим условиям на заготовку и основной материал выбирают исходную заготовку и методы ее изготовления, дается технико-экономическое обоснование выбора заготовки.
Выбирают технологические базы, оценивают точность и надежность базирования (используют классификаторы способов базирования и существующую методику выбора технологических баз).
По документации типового, группового или единичного ТП составляют маршрут обработки, определяют последовательность технологических операций и состав технологического оснащения.
В основу построения маршрута обработки (плана операций) должны быть положены следующие принципы:
- в первую очередь необходимо назначать те операции, при выполнении которых в наименьшей степени уменьшается жесткость детали, а также те поверхности, при обработке которых легче выявляются дефекты заготовки и в наибольшей степени перераспределяются внутренние напряжения, в связи с чем уменьшается возможность деформации детали в последующих операциях
- операции, при выполнении которых можно ожидать повышенного брака, следует выполнять в начале технологического процесса
- в разрабатываемом технологическом процессе обработки детали необходимо предусмотреть раздельное выполнение черновых, чистовых и отделочных операций, в противном случае это может привести к снижению точности обработки
- точно скоординированные соосные отверстия необходимо обрабатывать с одной установки
- план операций механической обработки должен быть связан с термообработкой, так как последняя влияет не только на маршрут движения детали, но и на обрабатываемость металла и качество обработанных поверхностей
- отделочные операции обработки поверхностей следует выполнять в конце технологического процесса
Важный этап - разработка технологических операций и расчет режимов обработки. На основании документации типовых, групповых или единичных технологических процессов и классификатора технологических операций составляют последовательность переходов в каждой операции, выбирают средства технологического оснащения (СТО), в том числе средства контроля и испытаний (используют стандарты, каталоги, альбомы).
На этом же этапе выбирают средства механизации и автоматизации процесса и внутрицеховые средства транспортирования. Назначают и рассчитывают режимы обработки на основании тех-нологических нормативов.
Необходимо осуществить нормирование ТП: установить исходные данные для расчета норм времени и расхода материалов, рассчитать затраты труда и расход материалов, определить разряд работ и профессии исполнителей операций (используют нормативы времени и расхода материалов, классификаторы разрядов работ и профессий).
По методике расчета экономической эффективности процессов (просчитывается несколько вариантов) выбирают оптимальный ТП.
На заключительном этапе на основании стандартов ЕСТД технологический процесс оформляется документально, осуществляется нормоконтроль технической документации.
Выбор технологического оборудования. Этот этап начинают с анализа формирования типовых поверхностей деталей для определения наиболее эффективных методов их обработки, учитывая при этом назначение и параметры изделия. Результаты анализа представляют в виде отношений затрат основного и штучного времени и приведенных затрат на выполнение работ различными методами. Лучшим вариантом считается тот, значения показателей которого минимальные.
Выбор оборудования осуществляют по главному параметру, в наибольшей степени выявляющему его функциональное значение и технические возможности. Физическая величина, характеризующая главный параметр, устанавливает взаимосвязь оборудования с размером изготовляемого изделия.
При выборе оборудования учитывают также минимальный объем приведенных затрат на выполнение технологического процесса при максимальном сокращении периода окупаемости затрат на механизацию и автоматизацию. Годовая потребность в оборудовании определяется по годовому объему работ, устанавливаемому статистическим анализом затрат средств и времени на изготовление изделий. Годовые приведенные расходы на использование оборудования определяются размерами затрат на его эксплуатацию.
Производительность оборудования определяют на основании анализа времени изготовления изделия заданного качества.
Выбор технологической оснастки и средств контроля. При выборе технологической оснастки и средств контроля предусматривается проведение следующего комплекса работ:
- анализ конструктивных характеристик изготавливаемого изделия (габаритные размеры, материалы, точность, геометрия и шероховатость поверхностей и т. д.), организационных и технологических условий изготовления изделия (схема базирования и фиксации, вид технологической операции, организационная форма процесса изготовления и т. д.)
- группирование технологических операций для определения наиболее приемлемой системы технологической оснастки и повышения коэффициента ее использования
- определение исходных требований к технологической оснастке
- отбор номенклатуры оснастки, соответствующей установленным требованиям
- определение исходных расчетных данных для проектирования и изготовления новых конструкций оснастки
- выдача технического задания на разработку и изготовление технологической оснастки
Конструкцию оснастки определяют на основе стандартов и типовых решений для данного вида технологических операций с учетом габаритных размеров изделий, вида и материала заготовок, точности параметров и конструктивных характеристик обрабатываемых поверхностей, влияющих на конструкцию оснастки, технологических схем базирования и фиксации заготовок, характеристик оборудования и объемов производства.
При разработке процессов контроля выявляют характеристики объекта контроля; показатели процесса контроля, определяющие выбор средств; уточняют методы и схемы измерений, для чего требуется конструкторская документация на изделие, технологическая документация на его изготовление и контроль, методика расчета показателей контроля.
Состав средств контроля должен обеспечивать заданные показатели с учетом метрологических и эксплуатационных характеристик (используются государственные, отраслевые стандарты и стандарты предприятий на средства контроля, классификаторы и каталоги средств контроля). Произведенный выбор средств контроля обосновывается экономически выдаются исходные данные и технические задания для проектирования недостающих средств. Затем составляют ведомости отобранных средств. По результатам выбора средств контроля оформляют технологическую документацию согласно требованиям стандартов.
Формы организации технологических процессов. Форма организации технологических процессов изготовления изделия зависит от установленного порядка выполнения операций, расположения технологического оборудования, числа изделий и направления их движения в процессе изготовления.
Существуют две формы организации ТП - групповая и поточная:
- Групповая форма организации ТП характеризуется однородностью конструктивно-технологических признаков заготовок, единством средств технологического оснащения одной или нескольких технологических операций и специализацией рабочих мест. Группы заготовок для обработки в определенном структурном подразделении (цехе, участке и т. д.) должны устанавливаться с учетом трудоемкости обработки и объема выпуска. Окончательно номенклатуру групп заготовок, подлежащих обработке на конкретном участке (цехе), следует устанавливать после расчета загрузки оборудования.
- Поточную форму отличает специализация каждого рабочего места на определенной операции, согласованное и ритмичное выполнение всех операций технологического процесса на основе постоянства такта выпуска и размещение рабочих мест в последовательности, строго соответствующей ТП.
При рассмотрении факторов, определяющих форму организации ТП, сначала устанавливают виды изделий, затем их группируют по общности конструктивно-технологических признаков. Это позволяет в каждом случае определить тип производства изделий и их составных частей.
Учитывая заданную программу выпуска каждого изделия, намечают календарные сроки выполнения заданий на основе длительности производственных процессов. Одновременно определяют необходимое оборудование, коэффициент его загрузки, а также показатель относительной трудоемкости.
Организация ТП должна обеспечивать ритмичный выпуск изделий при условии их прохождения по всем операциям с наименьшими перерывами, т. е. максимально приближаться к поточной форме. Поточная форма организации ТП в зависимости от номенклатуры одновременно обрабатываемых заготовок может реализовываться на однономенклатурных и многономенклатурных поточных линиях. Первая поточная линия характеризуется обработкой заготовок одного наименования по закрепленному ТП в течение длительного периода времени. На многономенклатурных поточных линиях обрабатывается группа конструктивно подобных деталей с однородными операциями обработки, причем каждая деталь имеет серийный выпуск.
Разработка типовых и групповых технологических процессов. Типовой технологический процесс характеризуется единством содержания и последовательности большинства технологических операций для группы деталей, обладающих общими конструктивными признаками.
Типовые технологические процессы разрабатывают на основе анализа множества действующих и возможных технологических процессов на типовые представители групп деталей. Типизация обеспечивает устранение многообразия технологических процессов обоснованным сведением их к ограниченному числу типов. Типизация технологических процессов основана на классификации объектов производства, она заключается в разделении их по конструктивным признакам на отдельные группы, для которых возможна разработка общих технологических процессов или операций.
Начальным этапом разработки типовых технологических процессов является классификация объектов производства. Затем для каждого класса деталей разрабатывают основные маршруты изготовления, включая заготовительные процессы. Затем выбирают заготовку и методы ее изготовления. Руководствуясь классификатором способов базирования и методикой выбора технологических баз, выбирают схему базирования, оценивают точность и надежность базирования.
Составляют технологический маршрут в порядке последовательности операций, определяют группы оборудования для выполнения операций.
При разработке технологических операций — выбирают их структуру, последовательность переходов в операции, подбирают оборудование и оснастку, обеспечивающие оптимальную произво-дительность при заданном качестве, рассчитывают загрузку оборудования, определяют оптимальные режимы резания, припуски на обработку, а также нормы времени. Устанавливают разряд работ и профессии исполнителей операций.
Оценка вариантов типовых технологических процессов для выбора оптимального осуществляется по методикам расчета точности, производительности и экономической эффективности.
Заключительным этапом разработки типовых технологических процессов является оформление их согласно требованиям стандартов ЕСТД.
Групповой технологический процесс (ГТП) предназначен для совместного изготовления группы изделий различной конфигурации в конкретных условиях производства на специализированных рабочих местах. ГТП разрабатывается с целью экономически целесообразного применения методов и средств крупносерийного и массового производства в условиях единичного, мелкосерийного и серийного производства. Групповой технологический процесс состоит из комплекса групповых технологических операций, разрабатываемых для выполнения на специализированных рабочих местах согласно технологическому маршруту изготовления определенной группы изделий.
При разработке групповой технологической операции следует предусмотреть достаточную величину суммарной трудоемкости технологически однородных работ для обеспечения непрерывной загрузки средств технологического оснащения без их полной переналадки в течение экономически целесообразного периода. Основой разработки ГТП и выбора общих средств технологического оснащения для совместной обработки группы изделий является комплексное изделие.
При выборе комплексного изделия следует учитывать, что его конструкция должна содержать основные элементы всех изделий группы, подлежащие обработке. Комплексное изделие может быть одним из изделий группы, реально существующим или искусственно созданным (т. е. условным).
При значительном разнообразии конструкций, затрудняющих искусственное создание комплексного изделия, его заменяют двумя или несколькими характерными деталями группы. Групповые технологические процессы и операции разрабатывают для всех типов производства только на уровне предприятия в соответствии с требованиями стандарта.
МИНИСТЕРСТВО ОБРАЗОВАНИЯ РОССИЙСКОЙ ФЕДЕРАЦИИ
РЯЗАНСКАЯ ГОСУДАРСТВЕННАЯ РАДИОТЕХНИЧЕСКАЯ
АКАДЕМИЯ
Кафедра технологии РЭА
Пояснительная записка к курсовому проекту
по курсу "Технология машиностроительного производства"
на тему "Разработка технологического процесса изготовления детали
экран РГРА 745 561.002"
Проект выполнила
студентка гр. 070 А. А. Болтукова
Руководитель проекта
Задание………………………………………………………………………………………………………………..2
Чертеж детали………………………………………………………………………………………………………..3
Введение………………………………………………………………………………………………………………5
1.Проектирование технологического процесса с использованием типового……………….……..……..6
1.1 Анализ исходных данных…………………………………………………………………………...…….6
1.2 Определение конструкторско-технологического кода детали……………………………………..7
2. Оценка показателя технологичности конструкции детали………………………………………………8
3. Выбор метода изготовления детали………………………………………………………………………...9
4. Выбор заготовок и технологических баз…………………………………………………………………..10
5. Назначение режимов обработки…………………………………………………………………………....12
6. Выбор технологической оснастки…………………………………………………………………………..13
7. Техническое нормирование………………………………………………………………………………….14
7.1 Раскрой на гильотинных ножницах……………………………………………………………………14
7.2 Холодная штамповка…………………………………………………………………………………….15
8. Определение типа производства…………………………………………………………………………...17
9. Технико-экономические показатели разработанного технологического процесса………………...18
10. Расчет размера партии деталей, заготовок………………………………………………………………21
12. Мероприятия по безопасности труда………………………………………………………………………23
13. Заключение……………………………………………………………………………………………………..24
14. Библиографический список………………………………………………………………………………….25
Приложение 1………………………………………………………………………………………………..…26
Приложение 2………………………………………………………………………………………………..…27
Приложение 3………………………………………………………………………………………………..…28
Приложение 4………………………………………………………………………………………………..…29
В настоящее время в нашей стране сложилась такая ситуация, что развитие промышленности является самой приоритетной из всех поставленных задач. Для того, чтобы Россия заняла прочное место среди ведущих мировых держав, в ней должна существовать развитая сфера промышленного производства, которая должна основываться не только на восстановлении основанных в советский период заводов, но и на новых, более современно оборудованных, предприятиях.
Одним из важнейших шагов на пути к экономическому процветанию является подготовка специалистов, которые имели бы не строго ограниченные рамками своей профессии знания, а могли комплексно оценить выполняемую ими работу и ее результат. Такими специалистами являются инженеры-экономисты, разбирающиеся не только во всех тонкостях экономических аспектов функционирования предприятия, но и в сущности производственного процесса, который и обуславливает это функционирование.
Целью данного курсового проекта является ознакомление непосредственно с процессом производства, а также оценка и сравнение его эффективности не только с экономической, но и с технологической точек зрения.
Производство изделия, его сущность и методы оказывают наиболее весомое влияние на технологические, эксплуатационные, эргономические, эстетические и, конечно, функциональные характеристики этой продукции, а, следовательно, на его себестоимость, от которой в прямой зависимости находятся цена изделия, спрос на него со стороны пользователей, объемы продаж, прибыль от реализации, а, следовательно, все экономические показатели, которые и определяют финансовую устойчивость предприятия, его рентабельность, долю рынка и т.д. Таким образом, то, как изготовляется продукция, оказывает влияние на весь жизненный цикл товара.
Сегодня, когда конкурентный рынок вынуждает производителей переходить к наиболее качественным и дешевым продуктам, особенно важно оценить все аспекты производства, распространения и потребления изделия еще на стадии его разработки, чтобы избежать неэффективного использования ресурсов предприятия. Это помогает также в совершенствовании технологических процессов, которые разрабатываются часто не только исходя из потребностей рынка в изготовлении новый продукции, но и принимая во внимание стремление производителей к более дешевому и быстрому способу получения уже существующей продукции, что сокращает производственный цикл, уменьшает величину связанных в производстве оборотных средств, а, следовательно, стимулирует рост инвестиций в новые проекты.
Итак, проектирование технологического процесса является важнейшим этапом производства продукции, который влияет на весь жизненный цикл товара и способен стать определяющим при принятии решения о производстве того или иного продукта.
Технологический процесс - главная часть производственного процесса, включающая действия по изменению размеров, формы, свойств и качества поверхностей детали, их взаимного расположению с целью получения нужного изделия.
Типовой технологический процесс является унифицированным для наиболее типичных деталей, обладающих сходными технико-конструктивными параметрами. Инженерами высокого класса разрабатывается технологический процесс для типовых деталей, а затем, с их помощью, составляют рабочие технологические процессы для конкретной детали. Использование типового технологического процесса позволяет упростить разработку тех. процессов, повысить качество этих разработок, сэкономить время и сократить затраты на технологическую подготовку производства.
Разработка технологического процесса включает в себя следующие этапы :
Определение технологической классификационной группы детали;
Выбор по коду типового технологического процесса (выбор метода получения детали);
Выбор заготовок и технологических баз;
Уточнение состава и последовательности операций;
Уточнение выбранных средств технологического оснащения.
Для определения технологической классификационной группы детали необходимо изучить исходные данные, в которых содержится информация о детали и располагаемом для ее изготовлению оборудовании.
Исходные данные содержат:
· чертеж детали
· сборочный чертеж штампа
· спецификация
В результате изучения этих данных, получаем:
Деталь - экран - представляет собой плоскую деталь с конструкторским кодом:
РГРА. 755561.002.
Материал: Сталь 10 ГОСТ 914- 56 - качественная низкоуглеродистая сталь с содержанием углерода 0,2 %. Этот сплав хорошо сваривается и обрабатывается резанием, а также давлением в холодном состоянии. Эти свойства доказывают целесообразность использования холодной штамповки для изготовления этой детали.
Сортамент: лист толщиной 1 мм. Из данного материала обычно изготавливают горячекатаные листы.
Шероховатость: для всей поверхности детали высота неровностей профиля по десяти точкам R z =40 мкм, среднеарифметическое отклонение профиля R a =10 мкм. Класс шероховатости 4. Поверхность детали образуется без удаления верхнего слоя.
Степень точности: наибольший квалитет 8
Технологический процесс: в данном случае наиболее целесообразно применять холодную штамповку.
Холодная штамповка - это процесс формообразования поковок или готовых изделий в штампах при комнатной температуре.
Масса детали:
M = S*H*r, где S – площадь детали, мм 2 ; H – толщина, мм; r - плотность, г/мм 3

Штамп последовательный
Штамп - деформирующий инструмент, под воздействием которого материал или заготовка приобретает форму и размеры, соответствующие поверхности или контуру этого инструмента . Основными элементами штампа являются пуансон и матрица.
Конструкция данного штампа включает пуансон для пробивки отверстия диаметром 18 мм, а также пуансон для вырубки наружного контура детали.
Этот штамп является последовательным многооперационным штампом, который предназначен для штамповки деталей из листового материала. Изготовление заготовки проходит в 2 этапа: сначала пробиваются отверстие диаметром 18 мм, затем получение наружного контура детали.
При нахождении технологической классификационной группы детали необходимо к уже имеющемуся конструкторскому коду детали добавить технологический код детали.
МИНИСТЕРСТВО ОБРАЗОВАНИЯ РОССИЙСКОЙ ФЕДЕРАЦИИ
РЯЗАНСКАЯ ГОСУДАРСТВЕННАЯ РАДИОТЕХНИЧЕСКАЯ
АКАДЕМИЯ
Кафедра технологии РЭА
Пояснительная записка к курсовому проекту
по курсу «Технология машиностроительного производства»
на тему «Разработка технологического процесса изготовления детали
экран РГРА 745 561.002»
Проект выполнила
студентка гр. 070 А. А. Болтукова
Руководитель проекта
Задание………………………………………………………………………………………………………………..2
Чертеж детали………………………………………………………………………………………………………..3
Введение………………………………………………………………………………………………………………5
1.Проектирование технологического процесса с использованием типового……………….……..……..6
1.1 Анализ исходных данных…………………………………………………………………………...…….6
1.2 Определение конструкторско-технологического кода детали……………………………………..7
2. Оценка показателя технологичности конструкции детали………………………………………………8
3. Выбор метода изготовления детали………………………………………………………………………...9
4. Выбор заготовок и технологических баз…………………………………………………………………..10
5. Назначение режимов обработки…………………………………………………………………………....12
6. Выбор технологической оснастки…………………………………………………………………………..13
7. Техническое нормирование………………………………………………………………………………….14
7.1 Раскрой на гильотинных ножницах……………………………………………………………………14
7.2 Холодная штамповка…………………………………………………………………………………….15
8. Определение типа производства…………………………………………………………………………...17
9. Технико-экономические показатели разработанного технологического процесса………………...18
10. Расчет размера партии деталей, заготовок………………………………………………………………21
12. Мероприятия по безопасности труда………………………………………………………………………23
13. Заключение……………………………………………………………………………………………………..24
14. Библиографический список………………………………………………………………………………….25
Приложение 1………………………………………………………………………………………………..…26
Приложение 2………………………………………………………………………………………………..…27
Приложение 3………………………………………………………………………………………………..…28
Приложение 4………………………………………………………………………………………………..…29
В настоящее время в нашей стране сложилась такая ситуация, что развитие промышленности является самой приоритетной из всех поставленных задач. Для того, чтобы Россия заняла прочное место среди ведущих мировых держав, в ней должна существовать развитая сфера промышленного производства, которая должна основываться не только на восстановлении основанных в советский период заводов, но и на новых, более современно оборудованных, предприятиях.
Одним из важнейших шагов на пути к экономическому процветанию является подготовка специалистов, которые имели бы не строго ограниченные рамками своей профессии знания, а могли комплексно оценить выполняемую ими работу и ее результат. Такими специалистами являются инженеры-экономисты, разбирающиеся не только во всех тонкостях экономических аспектов функционирования предприятия, но и в сущности производственного процесса, который и обуславливает это функционирование.
Целью данного курсового проекта является ознакомление непосредственно с процессом производства, а также оценка и сравнение его эффективности не только с экономической, но и с технологической точек зрения.
Производство изделия, его сущность и методы оказывают наиболее весомое влияние на технологические, эксплуатационные, эргономические, эстетические и, конечно, функциональные характеристики этой продукции, а, следовательно, на его себестоимость, от которой в прямой зависимости находятся цена изделия, спрос на него со стороны пользователей, объемы продаж, прибыль от реализации, а, следовательно, все экономические показатели, которые и определяют финансовую устойчивость предприятия, его рентабельность, долю рынка и т.д. Таким образом, то, как изготовляется продукция, оказывает влияние на весь жизненный цикл товара.
Сегодня, когда конкурентный рынок вынуждает производителей переходить к наиболее качественным и дешевым продуктам, особенно важно оценить все аспекты производства, распространения и потребления изделия еще на стадии его разработки, чтобы избежать неэффективного использования ресурсов предприятия. Это помогает также в совершенствовании технологических процессов, которые разрабатываются часто не только исходя из потребностей рынка в изготовлении новый продукции, но и принимая во внимание стремление производителей к более дешевому и быстрому способу получения уже существующей продукции, что сокращает производственный цикл, уменьшает величину связанных в производстве оборотных средств, а, следовательно, стимулирует рост инвестиций в новые проекты.
Итак, проектирование технологического процесса является важнейшим этапом производства продукции, который влияет на весь жизненный цикл товара и способен стать определяющим при принятии решения о производстве того или иного продукта.
Технологический процесс - главная часть производственного процесса, включающая действия по изменению размеров, формы, свойств и качества поверхностей детали, их взаимного расположению с целью получения нужного изделия.
Типовой технологический процесс является унифицированным для наиболее типичных деталей, обладающих сходными технико-конструктивными параметрами. Инженерами высокого класса разрабатывается технологический процесс для типовых деталей, а затем, с их помощью, составляют рабочие технологические процессы для конкретной детали. Использование типового технологического процесса позволяет упростить разработку тех. процессов, повысить качество этих разработок, сэкономить время и сократить затраты на технологическую подготовку производства.
Разработка технологического процесса включает в себя следующие этапы :
Определение технологической классификационной группы детали;
Выбор по коду типового технологического процесса (выбор метода получения детали);
Выбор заготовок и технологических баз;
Уточнение состава и последовательности операций;
Уточнение выбранных средств технологического оснащения.
Для определения технологической классификационной группы детали необходимо изучить исходные данные, в которых содержится информация о детали и располагаемом для ее изготовлению оборудовании.
Исходные данные содержат:
· чертеж детали
· сборочный чертеж штампа
· спецификация
В результате изучения этих данных, получаем:
Деталь - экран - представляет собой плоскую деталь с конструкторским кодом:
РГРА. 755561.002.
Материал: Сталь 10 ГОСТ 914- 56 - качественная низкоуглеродистая сталь с содержанием углерода 0,2 %. Этот сплав хорошо сваривается и обрабатывается резанием, а также давлением в холодном состоянии. Эти свойства доказывают целесообразность использования холодной штамповки для изготовления этой детали.
Сортамент: лист толщиной 1 мм. Из данного материала обычно изготавливают горячекатаные листы.
Шероховатость: для всей поверхности детали высота неровностей профиля по десяти точкам Rz =40 мкм, среднеарифметическое отклонение профиля Ra =10 мкм. Класс шероховатости 4. Поверхность детали образуется без удаления верхнего слоя.
Степень точности: наибольший квалитет 8
Технологический процесс: в данном случае наиболее целесообразно применять холодную штамповку.
Холодная штамповка - это процесс формообразования поковок или готовых изделий в штампах при комнатной температуре.
Масса детали:
M = S*H*r, где S – площадь детали, мм2 ; H – толщина, мм; r - плотность, г/мм3
Штамп последовательный
Штамп - деформирующий инструмент, под воздействием которого материал или заготовка приобретает форму и размеры, соответствующие поверхности или контуру этого инструмента . Основными элементами штампа являются пуансон и матрица.
Конструкция данного штампа включает пуансон для пробивки отверстия диаметром 18 мм, а также пуансон для вырубки наружного контура детали.
Этот штамп является последовательным многооперационным штампом, который предназначен для штамповки деталей из листового материала. Изготовление заготовки проходит в 2 этапа: сначала пробиваются отверстие диаметром 18 мм, затем получение наружного контура детали.
При нахождении технологической классификационной группы детали необходимо к уже имеющемуся конструкторскому коду детали добавить технологический код детали.
Для определения технологического кода детали по имеющимся данным определим ряд признаков, а затем найдем их код по «Конструкторско-технологическому классификатору деталей» :
Таблица 1.
№ | Признак | Значение | Код |
1 | Метод изготовления | Холодная штамповка | 5 |
2 | Вид материала | Углеродистая сталь | У |
3 | Объемно-габаритные характеристики | Толщина 1 мм | 6 |
4 | Вид дополнительной обработки | С заданной шероховатостью | 1 |
5 | Уточнение вида дополнит. обработки | галтовка | 1 |
6 | Вид контролируемых параметров | Шероховатость, точность | М |
7 | Количество исполнительных размеров | 3 | 1 |
8 | Количество констр. элементов, получаемых дополнит. Обработкой | 1 | 1 |
9 | Количество типоразмеров | 4 | 2 |
10 | Сортамент материала | лист горячекатаный | 5 |
11 | Марка материала | Сталь 10КП лист 1,0-II-H ГОСТ 914-56 | Д |
12 | Масса | 6 г | 4 |
13 | Точность | квалитет-8, Rz=40, Ra=10 | П |
14 | Система простановка размеров | прямоугольная система координат последовательно от одной базы | 3 |
Таким образом, полный конструкторско-технологический код детали имеет вид:
РГРА. 745561.002 5У611М.1125Д4П3
Технологичность - это свойство конструкции изделия, обеспечивающее возможность его выпуска с наименьшими затратами времени, труда и материальных средств при сохранении заданных потребительных качеств .
Значение показателя технологичности определяется как комплексное через значения частных показателей в соответствии с ОСТ 107.15.2011-91 по формуле:
ki - нормированное значение частного показателя технологичности детали
Конструкция детали является технологичной, если рассчитанное значение показателя технологичности не меньше его нормативного значения. В противном случае конструкция детали должна быть доработана конструктором.
Оценка технологичности детали 5У611М.1125Д4П3
Таблица 2
Наименование и обозначение частного показателя технологичности | Наименование классификационного признака | Код градации признака | Нормированное значение показателя технологичности |
Показатель прогрессивности формообразования Кф | Технологический метод получения, определяющий конфигурацию (1-й разряд технологического кода) | 5 | 0,99 |
Показатель многономенклатурности видов обработки Ко | Вид дополнительной обработки (4-й разряд технологического кода) | 1 | 0,98 |
Показатель многономенклатурности видов контроля Кк | Вид контролируемых параметров (6-й разряд технологического кода) | М | 0,99 |
Показатель унификации конструктивных элементов Ку | Количество типоразмеров конструктивных элементов (9-й разряд технологического кода) | 2 | 0,99 |
Показатель точности обработки Кт | Точность обработки (13-й разряд технологического кода) | П | 0,96 |
Показатель рациональности размерных баз Кб | Система простановки размеров (14-й разряд технологического кода) | 3 | 0,99 |
Нормативное значение показателя технологичности равно 0,88. Рассчитанный. Следовательно, конструкция детали технологична.
Технологическому процессу сопутствует ряд вспомогательных процессов: складирование заготовок и готовых изделий, ремонт оборудования, изготовление инструмента и оснастки.
Технологический процесс условно состоит из трех стадий:
1. Получение заготовок.
2. Обработка заготовок и получение готовых деталей.
3. Сборка готовых деталей в изделие, их настройка и регулировка.
В зависимости от требований, предъявляемых к точности размеров, формы, относительного положения и шероховатости поверхностей детали с учетом ее размеров, массы, свойств материала, типа производства, выбираем один или несколько возможных методов обработки и тип соответствующего оборудования .
Деталь представляет собой плоскую фигуру, поэтому она может быть изготовлена из листового материала с помощью штампа.
Маршрут изготовления изделия:
1) подготовительная операция:
1.1) выбор заготовок;
1.2) составление карт раскроя материала;
1.3) расчет режимов обработки;
2) заготовительная операция - на гильотинных ножницах разрезают листы на полосы согласно карте раскроя; эта операция выполняется низко квалифицированным (1…2 разряд) резчиком с помощью гильотинных ножниц.
3) штамповочная операция - придание заготовке формы, размеров и качества поверхности, заданных чертежом; эта операция исполняется более квалифицированным (2…3 разряд) рабочим - штамповщиком, с применением штампа, оснащенного прессом.
4) галтовочная операция - снятие заусенцев; эту операцию выполняет слесарь 2…3 разряда на вибрационной машине
5) контрольная операция - контроль после каждой операции (визуальный), выборочный контроль на соответствие чертежу. Контроль размеров проводится с помощью штангенциркуля - для контура детали, и с помощью пробок - для отверстий.
Заготовки необходимо подбирать таким образом, чтобы обеспечить наиболее рациональное использование материала, минимальную трудоемкость получения заготовок и возможность снижения трудоемкости изготовления самой детали.
Так как деталь изготавливается из плоского материала, то в виде исходных материалов целесообразно использовать листы. Вследствие того, что деталь изготавливается методом холодной штамповки в последовательном штампе, то листы для подачи в штамп нужно разрезать на полосы. Необходимо найти как можно более рациональный способ раскройки материла, который определяется с помощью формулы:
где А - наибольший размер детали, мм
δ - допуск на ширину полосы, нарезанной на гильотинных ножницах, мм
Zн - гарантийный наименьший зазор между направляющими планками и полосой, мм
δ" - допуск на расстояние между направляющими планками и полосой, мм
а - боковая перемычка, мм
С помощью таблиц определяем для данной детали:
Для данной детали подойдут круглые заготовки.
Наибольший размер детали А = 36 мм.
Перемычки а=1,2 мм; в=0,8 мм
Допуск на ширину полосы, нарезанной на гильотинных ножницах δ=0,4 мм
Гарантийный наименьший зазор между направляющими планками и полосой Zн=0,50 мм
Допуск на расстояние между направляющими планками и полосой δ"=0,25
Продольный раскрой:
Получаем коэффициент использования материала:
Где SА - площадь детали, мм2 ;
SЛ - площадь листа, мм2 ;
n - количество деталей, полученных из листа.
В результате получаем:
Проанализируем поперечный раскрой:
Таким образом, продольный раскрой более экономичен, так как при этом раскрое коэффициент использования материала больше, чем при поперечном.
Приведем схемы раскрой для продольного раскроя материала (рис. 1, 2)
а=1,2 t=D+в=36,8
Рис. 1. Раскрой полосы
Рис. 2. Раскрой листа.
Исходя из конструкции штампа, базирование заготовки осуществляется с помощью упора и направляющих планок штампа, а базирование пуансонов - по геометрическому центру пуансона матрицы (по контору детали).
Наибольшую точность обеспечивает совпадение конструкторской и технологической баз. В данном случае будет трудно обеспечить высокую точность, так как последовательный штамп предполагает движение заготовки от пуансона к пуансону, что, естественно, увеличивает погрешность изготовления детали.
Режимы обработки представляют собой совокупность параметров, определяющих условия, при которых изготавливаются изделия.
Штамп последовательного действия предполагает сначала - пробивка отверстий, а затем - вырубка по контуру. Вырубка и пробивка являются операциями отделения части листа по замкнутому контуру в штампе, после которых готовая деталь и отход проталкиваются в матрицу.
Для детали, получаемой штамповкой, расчет режимов заключается в определении усилий штамповки. Полное усилие штамповки складывается из усилий пробивки, вырубки, снятия и проталкивания детали.
Условие пробивки определяется по формуле:
где L - периметр пробиваемого отверстия, мм;
h - толщина детали, мм;
σср - сопротивление срезу, МПа.
Из таблицы находим: σср =270 МПа.
Таким образом,
Усилие вырубки детали по контуру определяется по той же формуле:
Определение требуемых усилий проталкивания детали (отхода) сквозь матрицу производится по формуле:
где Кпр - коэффициент проталкивания. Для стали Kпр =0,04
Аналогично определяется усилие снятия отхода (детали) с пуансона:
где Kсн - коэффициент проталкивания. Для стали Kсн =0,035
Полное усилие штамповки найдем по формуле:
где 1,3 - коэффициент запаса на усиление пресса.
Для данной детали получим полное усилие штамповки:
Технологическая оснастка представляет собой дополнительные устройства, применяемые для повышения производительности труда, улучшения качества.
Для изготовления детали сепаратор, исходя из имеющегося оборудования, целесообразно применять штамп последовательного действия, когда вырубка отверстий и контура детали производится последовательно, что позволяет использовать простую конструкцию штампа, а в качестве оборудования по технологическому процессу требуются гильотинные ножницы и механический пресс.
Гильотинные ножницы представляют собой станок для резки бумажных кип, металлический листов и т.д., в котором один нож неподвижно закреплен в станине, а другой, поставленный наклонно, получает возвратно-поступательное движение.
Главными параметрами, который является наиболее показательным для выбираемого оборудования и который обеспечивает выполнение режимов, предусмотренных технологическим процессом, для пресса является усилия штамповки, прессования, а для гильотинных ножниц - наибольшая толщина разрезаемого листа и его ширина.
Таблица 3
Характеристики ножниц Н475
Рассчитанное усилие штамповки Рп =63,978 кН выбираем [по приложению 5, 3051] пресс таким образом, чтобы его номинальное усилие превышало значение требуемого усилия штамповки.
Таблица 4
Характеристики пресса КД2118А
Нормирование технологического процесса состоит в определении величины штучного времени Тш для каждой операции (при массовом производстве) и штучно-калькуляционного времени Тшт (при серийном производстве). В последнем случае рассчитывается подготовительно-заключительное время Тпз.
Величины и Тшк определяют по формулам:
; Тшк = Тш + Тпз /n,
где То - основное технологическое время, мин;
Тв - вспомогательное время, мин
Тоб - время обслуживания рабочего места, мин;
Тд - время перерывов на отдых и личные надобности, мин;
Тпз – подготовительно-заключительное время, мин;
n – количество деталей в партии.
Основное (технологическое) время затрачивается непосредственно на изменение форм и размеров детали.
Вспомогательное время расходуется на установку и снятие детали, управление станком (прессом) и изменение размеров детали.
Сумма основного и вспомогательного времени называется оперативным временем.
Время обслуживания рабочего места складывается из времени технического обслуживания (смена инструмента, подналадка станка) и времени на организационное обслуживание рабочего места (подготовка рабочего места, смазка станка и т.д.)
Подготовительно-заключительное время нормируется на партию деталей (на смену). Оно расходуется на ознакомление с работой, настройку оборудования, консультации с технологом и т.д.
Рассчитаем нормирование технологического процесса нарезки листа материала на полосы.
Так как в последовательный штамп подаются полосы материала, то требуется разрезать листы стали 10 на полосы, ширина которых равна ширине заготовок. Для этого используем гильотинные ножницы
Операция - резка полос из стального листа 710 х 2 000;
шаг - 38,75 мм;
18 полос из листа;
18 х 54 = 972 шт. -заготовок из листа;
ручной способ подачи и установки листа;
ручной способ удаления отхода;
оборудование - гильотинные ножницы Н475;
40 ходов ножа в минуту;
способ включения ножной педалью;
муфта включения фрикционная;
положение рабочего - стоя.
1. Расчет нормы штучного времени на резку стального листа
1.1. Взять лист из стопы, положить на стол ножниц, установить по заднему упору. Время на эти операции зависит от площади листа и обычно указывается в расчете на 100 листов.
При площадь листа время на 100 листов- 5,7 мин.
Следуя указаниям по расчетам:
1.1.1) при подсчете нормы штучного времени на заготовку, время по нормативам делим на число заготовок, получаемых из листа;
1.1.2) при установке листа по заднему упору, время по нормативам принимаем с коэффициентом, равным 0,9;
1.1.3) поправочный коэффициент при толщине листа стали 1 мм - 1,09.
1.2. Включить ножницы 18 раз. Так как требуется получить 18 полос: 17 включений ножниц для того, чтобы отделить полосы одну от другой и еще одно - чтобы отделить последнюю полосу от остатка листа. Время, затрачиваемое на это, зависит от способа включения гильотинных ножниц.
При нажатии педали сидя - 0,01 мин на полосу.
1.3. Отрезать заготовки 18 раз. Длительность этой операции зависит от возможностей ножниц
При 40 ходов в минуту и фрикционной муфты выключения - 0,026 мин на полосу.
1.4.Продвинуть лист до упора 18 раз (так как лист делится на полосы с остатком, поэтому необходимо отделить последнюю полосу от отхода). Продолжительность данного действия зависит от длины листа и шага.
При длине листа по линии реза 2000 мм и шаге продвижения листа 38,75 < 50 мм время - 1,4 мин на полосу.
1.5.Взять отход со стола ножниц, уложить в стопу.
При площади заготовки время 0,83 мин.
Таблица 5.
Расчет нормы штучного времени на резку стального листа
* - см. пункт 1.1.2.
Норма штучного времени рассчитывается по формуле:
То – основное время резки;
Тв – вспомогательное время;
nд – число деталей в листе.
на 100 деталей;
Операция - вырубка детали по контуру, отверстий в детали из полосы;
штамп с открытым упором;
ручной способ подачи и установки заготовки;
ручной способ удаления отходов;
положение рабочего - сидя;
кривошипный пресс с усилием 63 Н;
150 ходов ползуна в минуту;
фрикционная муфта включения;
способ включения - педалью.
2. Расчет нормы штучного времени на штамповку детали из полосы.
1.1. Взять полосу, смазать с одной стороны. Необходимыми операциями подготовки заготовок к холодной штамповке являются удаление окалины, загрязнений, дефектов, покрытий-смазок. Затрачиваемое на это время зависит от площади заготовки.
При такой площади время на 100 полос равно 5,04 мин.
2.2. Установить полосу в штамп до упора. Эта операция необходима для обеспечения условия базирования, ее продолжительность зависит от вида штампа, длины и ширины полосы, а также толщины материала.
При ширине полосы 38,75 мм исходное время равно 5,04 мин на 100 полос.
При полосе длиной 2 м коэффициент равен 1,08;
для закрытого штампа - 1,1;
для стали толщиной 1 мм - 1,09.
2.3. Включить пресс. Длительность данного действия зависит от положения рабочего и способы управления прессом.
Для включения пресса педалью сидя - 0,01 мин на полосу;
2.4. Штамповать. Время, занимаемое штамповкой зависит от используемого оборудования.
Для пресса с числом ходов ползуна равным 150 и фрикционной муфтой - 0,026 мин на полосу.
2.5. Время, затрачиваемое на продвижение полосы на шаг, зависит от ширины и длины полосы и вида штампа.
Для полосы шириной 38,75 мм основное время равно 0,7 мин на 100 полос;
для закрытого штампа - коэффициент 1,1;
коэффициент для полосы длиной 2 м - 1,08.
2.6. Длительность операции удаления отхода полосы (решетки) определяется, исходя из полосы материала.
При полосе 38,75 х 2 000 - 3,28;
для закрытого штампа - 1,1;
коэффициент для стали толщиной 1 мм - 1,09.
Таблица 6.
Расчет нормы штучного времени на штамповку детали
Норма штучного времени:
nд - количество деталей, получаемых из полосы;
Кпр - коэффициент, учитывающий положение рабочего (сидя - 0,8);
аобс - время на организационно-техническое обслуживание рабочего места, для кривошипного пресса с усилием прессования до 100 кН, равно 5 % от оперативного времени;
аот.л. - время, затрачиваемое рабочими на отдых и личные надобности, при массе заготовки до 3 кг принимается как 5 % от оперативного времени.
Согласно ГОСТ 3.1108 - 74 ЕСТД тип производства характеризуется коэффициентом закрепления операций. На стадии проектирования технологических процессов используется следующая методика расчета коэффициента закрепления операций (серийности) за рабочим местом (станком) :
где Тт - такт выпуска, мин;
Т ш. ср. - среднее штучное время для выполнения операции, мин.
Такт выпуска рассчитывается по формуле:
Ф - действительный годовой фонд времени работы станка или рабочего места, ч (примем Ф=2000 ч).
N - годовая программа выпуска изделий, шт.
Среднее штучное время определяется как среднее арифметическое по операциям процесса. Будем считать, что время в основном затрачивается на нарезку и штамповку.
n - число операций (при указанном допущении k=2)
Дано, что годовая программа выпуска экрана равна 1000 тыс. шт.
Такт выпуска мин.
Штучное время мин.
Среднее штучное время мин.
Коэффициент закрепления операций.
В зависимости от величины Кзо выбираем тип производства: при 1< Кзо <10 крупносерийный тип производства.
Крупносерийное производство характеризуется изготовлением изделий периодически повторяющимся партиями. В таком производстве применяют специальное, специализированное и универсальное оборудование и приспособления.
Для экономической оценки используют в основном две характеристики: себестоимость и трудоемкость.
Трудоемкость - количество времени (в часах), затрачиваемое на изготовление одной единицы изделия. Трудоемкость процесса составляет сумма трудоемкости по всем операциям.
Трудоемкость операций складывается из подготовительно-заключительного времени Тпз, приходящегося на единицы продукции, и штучного времени Тш, затрачиваемого на выполнение данной операции. Численно трудоемкость операции Т равна штучно-калькуляционному времени Тшк, которое может быть рассчитано по формуле:
где n - количество деталей в партии, определяется по формуле:
где 480 мин - продолжительность одной рабочей сметы в минутах;
Подготовительно-заключительное время за смену складывается, в основном, из длительности подготовительно-заключительных операций для резки и штамповки. Примем:
мин в смену;
мин в смену.
Рассчитаем трудоемкость операции резки:
Штучное время резки:резки;
Трудоемкость операции резки: мин;
Рассчитаем трудоемкость операции штамповки:
Штучное время резки:резки;
Количество деталей в партии: шт;
Трудоемкость операции штамповки: мин;
Величина, обратная технологической норме времени Т, называется нормой выработки Q:
Согласно полученному значению трудоемкости, нормы выработки:
Производительность технологического процесса определяется количеством деталей, изготавливаемых за единицу времени(час, смена):
где Ф - фонд рабочего времени, мин;
Сумма трудоемкости по всем операциям процесса (в данном случае по двум: резке и штамповке).
Производительность технологического процесса: деталей в смену.
При экономической оценке варианта изготовления отдельной детали достаточно определить его технологическую себестоимость . Она отличается от полной тем, что в нее входят прямые затраты на основные материалы и производственная заработная плата, а также расходы, связанные с содержанием и эксплуатацией оборудования и инструмента.
где См - стоимость основных материалов или заготовок, руб./шт.;
З - заработная плата производственных рабочих, руб./шт.;
1,87 - коэффициент, учитывающий затраты на возмещение изношенного инструмента, оснастки и расходы на содержание и эксплуатацию оборудования, вместе взятые, составляют 87 % от заработной платы.
Стоимость основного материала определяется по формуле:
где М н. р. - норма расхода материала или масса заготовки, кг/шт.;
С м.о. - оптовая цена материала или заготовки, руб./кг;
mо - масса реализуемых отходов, кг/шт.;
Со - стоимость отходов, принимается в размере 10 % от стоимости основного материла, руб./кг.
Масса реализуемых отходов определяется по формуле:
где Мз - масса заготовки детали, кг/шт.;
Мд - масса детали, кг/шт.
Масса заготовки вычисляется по формуле:
где V - объем заготовки детали;
ρ- плотность материала заготовки, г/см3 ;
Sл –площадь листа;
tл - толщина листа;
n – число деталей из листа.
Масса заготовки: кг.
Масса детали уже рассчитана ранее: Мз =0,006 кг.
Масса реализуемых отходов: кг.
Оптовая цена стали 10: С м.о. = 1100 руб.·т=1,1 руб.·кг.
Тогда цена отходов: Со =0,1·1,1=0,11 руб.·кг.
Стоимость основного материала: руб. на деталь.
Заработная плата в зависимости от конкретных условий изготовления детали может быть выражена следующим образом:
где Кз - коэффициент, учитывающий доплаты к заработной плате рабочим (на отпуска, за ночные смены), а также отчисления на социальное страхование;
ti - норма штучного времени на выполнение технологической операции, мин./шт.;
Si - ставка квалификационного разряда рабочего, руб./ч;
n - число технологических операций.
В данном случае примем во внимание 2 операции: резку полос на гильотинных ножницах и штамповку детали. По уже рассчитанным значениях:
t1 =0,0015 мин.;
t2 =0,034 мин.;
Квалификационный разряд рабочего, выполняющего операцию резки - II; а операцию штамповки - III.
Тарифная ставка первого квалификационного разряда рабочего принимается - 4,5 руб./ч. Тарифная ставка каждого последующего квалификационного разряда рабочего увеличивается в 1,2 раза.
Для рабочих механических цехов доплаты к заработной плате составляют около 4,5 %, а отчисления на социальные нужды - 7,8 %, т.е. Кз =1,13.
В результате получаем заработную плату, приходящуюся на одну единицу изделия:
Окончательно получаем технологическую себестоимость единицы продукции:
10. Расчет размера партии деталей
Программа выпуска: N=1000 тыс.шт
Действительный годовой фонд времени: Ф=2000 час.
Тогда ритм производства должен быть: дет/час
Если Тш штамповки =0,034 мин, то дет/час
Из время на установку и снятие штампа t=30+10=40 мин, а зарплата рабочего 3 разряда Зр = 4,5 руб/час *1,44 = 6,48 руб/час.
Тогда руб
- Пусть с2 ’ = 0,01*10-3 руб. Тогда размер партии деталей
- Пусть с2 ’’ = 0,001 руб. Тогда размер партии деталей
Расчет размера партии заготовок
Из наладка упоров гильотинных ножниц 3,5мин, установка зазора между ножами пусть будет 16,5 мин, тогда tп.з. = 3,5+16,5 = 20мин, а затраты на наладку рабочего II разряда рубполос/час.
Если Тш резки = 0,0015мин, то полос/час.
Пусть с2 ’ = 0,01*10-3 руб, тогдаполос.
11. Рекомендации по наладке ножниц
Зазор между ножами регулируют в зависимости от толщины и прочности разрезаемого материала передвижением стола, для чего необходимо отпустить гайки болтов крепления стола к станине и при помощи 2 регулировочных винтов установить необходимый зазор, после чего гайки надо затянуть. Для установки ножей после переточки рекомендуется применять прокладки из фольги или другого тонкого листового материала.
Величину зазора определяем по табл. 11 в .
Наладка упоров . Для обрезки полос различной ширины применяются задний, передний и боковой упоры, упоры-угольники и упоры-кронштейны. Наладку заднего упора производят путем его перемещения с помощью маховичков по линейка или шаблонам. Если наладку производят по шаблону, то последний устанавливают кромкой в упор к нижнему ножу, а ко второй его кромке вплотную придвигают задний упор и закрепляют винтами. Наладку переднего упора производят по шаблону, уложенному на стол. Упоры –угольники, упоры-кронштейны и боковые упоры крепят к столу в различных положениях в зависимости от необходимости.
Задний упор
Ножи38,75 38,75
Нижний нож
Верхний нож
Нижний нож
Рис. 3. Наладка ножниц.
12. Безопасность труда
Основной задачей техники безопасности является обеспечение безопасных и здоровых условий труда без снижения его производительности . Для этого проводится большой комплекс мероприятий по созданию таких условий.
С целью предупреждения производственного травматизма подвижные части станков, рабочие зоны оборудования, технологической оснастки снабжаются оградительными устройствами (барьеры, решетки, кожухи, щитки и т. д.). Для обеспечения воздушной среды на рабочем месте, соответствующей санитарным нормам, станки, другое технологическое оборудование снабжаются индивидуальными или групповыми отсасывающими устройствами.
Большое значение имеет охрана окружающей среды. Для уменьшения загрязнений необходимо применение безотходных технологий, создание очистных сооружений, позволяющих многократно использовать одни и те же объемы воды, воздуха в защитных системах.
При разработке технологических процессов изготовления деталей необходимо предусматривать конкретные меры, обеспечивающие безопасные условия труда, охрану окружающей среды при изготовлении рассматриваемой детали.
Для обеспечения безопасности труда на операции резки с помощью гильотинных ножниц, помимо безопасной конструкции инструмента, рабочий должен использовать тканевые рукавицы для подачи листа материала внутрь ножниц, чтобы не поранить руки, а также халат, чтобы избежать порчи одежды при смазке листа.
Охрана окружающей среды при резке осуществляется по средством утилизации отходов, остающихся после нарезки листа на полосы, а при работе со смазкой следует аккуратно наносить ее на лист материла.
При штамповке рабочему необходимо быть предельно внимательным при включении штампа, так как он не снабжен ограждениями, а также использовать тканевые рукавицы для подачи полосы материала в штамп.
Отходы от штамповки должны утилизироваться, не нанося вреда окружающей среде.
Таким образом, использование типового технологического процесса облегчает проектирование, конструирование детали, ее изготовление и контроль.
Благодаря экономии не только времени, которое было бы затрачено на разработку в случае отсутствия такого «прототипа», но и сокращение затрат, требующихся на исправление и утилизацию брака при использовании неотработанных технологии, оборудования и оснастки, удается получить хорошие экономические показатели технологического процесса изготовления и сборки даже для небольших партий продукции и оборудования.
Наибольшее время при использовании типового процесса приходится затрачивать на технологическую подготовку производства, которая необходима для подгонки «прототипа» для конкретной детали. Учитывая, что многие операции из ТПП являются стандартными и вполне могли бы выполняться с помощью вычислительной техники, в настоящее время преобладающим является тенденция к поной или хотя бы частичной автоматизации процесса технологической подготовки производства.
Приложения Библиографический список
1. Дриц М. Е., Москалев М. А. «Технология конструкционных материалов и материаловедение: Учеб. для вузов. - М. Высш. шк., 1990. - 447 с.: ил.
2. Зубцов М. Е. „Листовая штамповка“. Л.: Машиностроение, 1980, 432 с.
3. Конструкторско-технологический классификатор деталей.
4. Лекции по курсу „Технология машиностроительного производства“ Лобанова С. А., 2001 г.
5. Мансуров И. З., Подрабинник И. М. Специальные кузнечно-прессовые машины и автоматизированные комплексы кузнечно-штампового производства: Справочник. М.: Машиностроение, 1990. 344 с.
6. Справочник нормировщика / Под общей ред. А. В. Ахумова. Л.: Машиностроение, 1987. 458 с.
7. Технология машиностроительного производства. Методические указания к курсовому проектированию/ Рязан. гос. радиотехн. акад; Сост.: А. С. Кирсов, С. Ф. Стрепетов, В. В. Коваленко; Под ред. С. А. Лобанова. Рязань, 2000. 36 с.
8. Правила оформления технологических документов: Методические указания к курсовому и ди пломному проектированию/ Рязан. гос. радиотехн. акад; Сост. А. С. Кирсов, Л. М. Мокров, В. И. Рязанов, 1997. 36 с.
Трудовые отношения
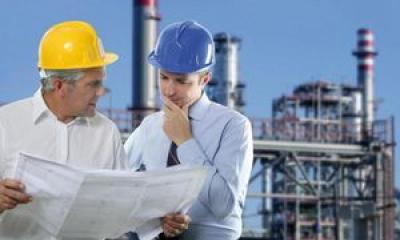
Должностная инструкция главного инженера, должностные обязанности главного инженера, образец должностной инструкции главного инженера Должностная инструкция главного инженера рэс
Открытие бизнеса
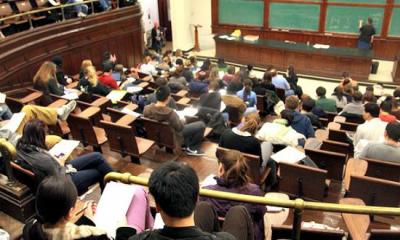
Где можно и где нельзя работать после туберкулеза Где можно работать после
Форекс
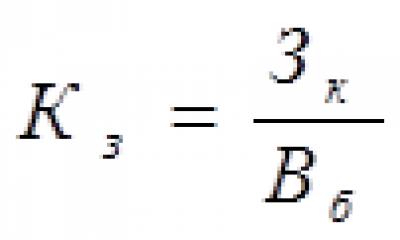