Организация серийного выпуска изделий потребовала сокращения вложенного в них овеществленного труда. Добиться снижения себестоимости изделий можно было за счет упрощения конструкции (в первую очередь отказа от излишеств – дорогих материалов, трудоемких украшений, нетехнологичных деталей и сборочных единиц) и изменения технологии (обеспечения разделения труда и кооперации производства).
Разделение труда в предельной форме можно представить, как членение технологического процесса изготовления изделия на операции – простейшие действия, каждое из которых выполняется одним работником (оператором). Научиться выполнению такой операции можно в течение нескольких минут, а достаточные навыки работы приобрести за 2...3 рабочие смены. Выигрыш от такой организации труда – высокая производительность при минимальных требованиях к квалификации работника.
Для обеспечения определенного уровня качества серийно выпускаемых изделий необходимо, чтобы все обработанные детали одного назначения (номенклатуры, типоразмера) были практически одинаковыми. Различия между деталями должны быть столь незначительны, чтобы любая из них собиралась с ответными, а собранные вместе они составляли изделие, неотличимое в работе от других. Детали, и более сложные изделия, если они отвечают поставленным требованиям, называются взаимозаменяемыми.
В бытовом смысле взаимозаменяемость можно рассматривать как одинаковость изделий, но поскольку абсолютно одинаковых изделий не существует, очевидно, что при изготовлении следует всего лишь не допустить таких различий, которые выходят за оговоренные нормы. Эти нормы фиксируют в документации (конструкторская документация, технические описания, паспорта и др.). Для придания наиболее часто употребляемым нормам официального статуса широко используется стандартизация. Стандартизуют сложные изделия и процессы, их составные части, вплоть до элементарных. Всем известны не только стандартные дома и машины, но и стандартное напряжение электрической сети, стандартные размеры магнитной ленты, магнитных и оптических дисков, скорости записи и воспроизведения информации.
Для получения стандартных изделий заданного уровня качества приходится организовывать разветвленную нормативную базу. Стандартизация является нормативной базой взаимозаменяемости серийно выпускаемых изделий и многократно воспроизводимых процессов.
В технике взаимозаменяемость изделий подразумевает возможность равноценной (с точки зрения оговоренных условий) замены одного другим в процессе изготовления или ремонта. Чем более подробно и жестко нормированы параметры изделий, тем проще реализуется замена, но тем сложнее обеспечить взаимозаменяемость.
Взаимозаменяемость изделий и их составных частей (узлов, деталей, элементов) следует рассматривать как единственную возможность обеспечения экономичного серийного и массового производства изделий заданного уровня качества. Одинаковый (колеблющийся в пределах пренебрежимых для потребителя различий) уровень качества конечных изделий конкретного производства обеспечивается выполнением определенного набора требований. Требования предъявляются ко всем элементам деталей и сопряжений, которые обеспечивают нормальную работу изделия. Обеспечение взаимозаменяемости, а значит и заданного уровня качества изделий подразумевает:
Установление комплекса требований ко всем параметрам, оказывающим влияние на взаимозаменяемость и качество изделий (нормирование номинальных значений и точности параметров);
Соблюдение при изготовлении установленных норм, единых для одинаковых объектов, и эффективный контроль нормируемых параметров.
При этом пробелы при назначении норм или неправильный, нечетко определенный выбор их границ могут привести к нарушению взаимозаменяемости изготавливаемых изделий, следовательно, к несоблюдению заданного уровня качества изделий. Неправильный или неполный набор при нормировании номенклатуры параметров или их предельных значений приведет к нарушению взаимозаменяемости (вплоть до издевательства над заказчиком: ...за время пути собака могла подрасти), при котором изготовитель формально не может быть обвинен в несоблюдении норм.
Итак, высшим достижением нормирования параметров изделия будет обеспечение полной взаимозаменяемости однотипных изделий в любой изготавливаемой партии. Полная взаимозаменяемость подразумевает взаимозаменяемость изделий по всем нормируемым параметрам. Параметры и свойства, не имеющие принципиального значения для функционирования изделий, не нормируются. Например, домохозяйку мало интересуют размеры частиц сахара-песка, который продается на вес, в то время как для макаронных изделий форма и размеры могут быть достаточно значимыми свойствами, поскольку лапша и вермишель развариваются неодинаково. Взаимозаменяемость (полная взаимозаменяемость) подразумевает соблюдение в процессе изготовления изделия всех его нормируемых параметров в заданных пределах. В число нормируемых параметров изделий могут входить:
Геометрические (размеры, форма, расположение и шероховатость поверхностей);
Физико-механические (твердость, масса, отражательная способность и т.д.);
Экономические (себестоимость, лимитная цена, производительность и др.);
Прочие (эргономические, эстетические, экологические и др.).
Можно отказаться от взаимозаменяемости еще в процессе проектирования, заложив в конструкцию компенсатор, который обеспечивает изменение в определенных пределах (регулирование) нормируемого параметра. Всем известны регулируемые опоры (ножки) приборов и мебели, которые позволяют компенсировать не только неточности изготовления самих изделий, но и несовершенство базовых поверхностей (стола, пола).
Функциональная взаимозаменяемость – аналог полной взаимозаменяемости, которая понимается не в буквальном смысле (одинаковость параметров), а ограничивается необходимым и достаточным набором требований к работе (выполнению функций) изделия. Например, функционально взаимозаменяемыми могут оказаться карандаш, шариковая или перьевая ручка, кусок мела, пишущая машинка, компьютер если необходимо записать краткое сообщение (перечень составлен без учета экономических затрат и квалификации). Наложение экономических ограничений может резко укоротить такой список. Особенностью, которую подчеркивает термин функциональная взаимозаменяемость, является приоритет выполняемых изделием функций (карандашом, мелом, ручкой...пишут) при возможных существенных технических отличиях используемых объектов. Функционально взаимозаменяемыми при определенной постановке задачи (своевременная явка на работу) могут быть признаны такие транспортные средства, как трамвай, троллейбус, автобус, такси, велосипед или собственные ноги.
Функционально взаимозаменяемыми по содержанию зафиксированной информации для владельца компьютера могут быть файлы, записанные на жестком диске, гибких дисках, компакт-дисках (при наличии соответствующих дисководов), а также твердая копия соответствующего файла, хотя параметрические отличия между носителями информации весьма существенны. В частности, распечаткой можно воспользоваться и тогда, когда компьютер перестал работать из-за временного отсутствия электроэнергии, технической неисправности, завирусованности.
Из рассмотренных примеров вытекают две акцентированных особенности функциональной взаимозаменяемости: нацеленность на результат при практически безразличном отношении к процессу (целеобеспечивающая взаимозаменяемость), либо гарантирующая результат за счет воспроизведения функций (процессуальная взаимозаменяемость). В частности, нам бывает безразлично, откуда и как получить необходимую текстовую информацию, если обеспечена ее полнота и доступность. С другой стороны, если эта информация подлежит редактированию или другому видоизменению (частичному заимствованию, объединению с дополнительной информацией и т.д.), для нас становится весьма важными свойствами не только форма ее представления (распечатка или электронная копия на дискете), но и система ее кодирования. Электронная копия текста становится бесполезной, если у нас в компьютере нет соответствующей среды (так называемый текстовый процессор, версия которого совместима с использованной). В данном случае речь идет о процессуальной взаимозаменяемости, поскольку принципиально описанные операции можно реализовать с помощью машинописи, но без компьютера здесь происходит скатывание к неполной взаимозаменяемости из-за затруднений в использовании шрифтов, математических знаков и прочих символов. Нарисованную картину можно продолжить до возврата к индивидуальному переписыванию текстов гусиными перьями.
Детали для изделий машиностроения (в отличие от ряда радиоэлектронных, оптических и др.) держат первый экзамен на взаимозаменяемость в процессе сборки. Неточно изготовленные детали могут не собраться друг с другом или сломаться при попытке собрать их силой, поэтому для механических деталей и узлов в первую очередь рассматривается такой аспект как геометрическая взаимозаменяемость.
Используемые для нормирования массивы значений геометрических параметров, как правило, оформлены в виде стандартов. Например, можно воспользоваться стандартами параметров макрогеометрии поверхностей (размеры, форма, расположение) и микрогеометрии (шероховатость). Стандарты пригодны для нормирования геометрических параметров любых типовых деталей и поверхностей в весьма широком диапазоне.
Годность изделия по данному параметру Q оценивают сравнением действительного значения параметра Qдств с его предельными допускаемыми значениями. Определение годности называется контролем параметра, и если при этом используются средства измерений, то контроль называют измерительным. Измерительный контроль обычно осуществляется в два этапа:
Определение действительного значения параметра;
Сравнение действительного значения параметра с нормированными значениями и определение годности объекта по контролируемому параметру.
Чтобы получить действительное значение контролируемого параметра заданного физической величиной, необходимо сравнить его реальное значение с единицей соответствующей физической величины – в этом и заключается суть любого измерения. Единицы физических величин стандартизованы, они воспроизводятся с помощью стандартных эталонов, а от них передаются стандартным и нестандартизованным рабочим средствам измерений.
1.1 Расчет допусков и посадок гладких цилиндрических сопряжений
1.2 Калибры для контороля гладких цилиндрических соединений
2. Расчет и выбор посадок подшипника качения
3. Шероховатость, отклонение формы и расположения поверхностей
4. Допуски и посадки шпоночных и шлицевых соединений
4.1 Шпоночное соединение
4.2 Прямобочное шлицевое соединение
4.3 Эвольвентное шлицевое соединение
Литература
1. Гладкие сопряжения и калибры
1.Задана посадка Æ56H6/k5.
Посадка с переходная.
Предельные отклонения отверстия Æ56H6: верхнее ES=+19мкм; нижнее EI=0.
Предельные отклонения вала Æ56k5: верхнее es=14 мкм; нижнее ei=+1 мкм.
Dmax = D + ES = 56 + 0,019 = 56,019 мм;
Dmin = D + EI = 56 + 0 = 56 мм;
dmax = d + es = 56 +0.014 = 56,014 мм;
dmin = d + ei = 56 + 0.001 = 56,001 мм;
TD = IT6 = 19 мкм;
Td = IT5 = 13 мкм;
Smax = ES - ei = 19- 1 = 18 мкм;
Smin = EI - es = 0 - 14 = -14 мкм;
TS = Smax - Smin = 18 + 14 = 32 мкм.
Проверка: TS = Td+TD 32= 19 + 13
2.Задана посадка Æ70S6/h7.
Посадка с зазором.
Предельные отклонения отверстия Æ70S6: верхнее ES=-59мкм; нижнее EI=-78.
Предельные отклонения вала Æ70h7: верхнее es=0 мкм; нижнее ei=-30 мкм.
Предельные размеры отверстия и вала:
Dmax = D + ES = 70 + (-0.059) = 69.941 мм;
Dmin = D + EI = 70 + (-78) = 69.922 мм;
dmax = d + es = 70 + 0 = 70 мм;
dmin = d + ei = 70 + (0.030) = 69.970 мм;
Допуски размеров отверстия и вала:
TD = IT6 = 19 мкм;
Td = IT7 = 30 мкм;
Параметры посадки (с зазором).
Nmax = dmax - Dmin = = -0,078 мм;
Nmin = dmin - Dmax = = -0,029 мм;
TN = Nmax - Nmin = -0,0678 + 0,029 = -0,049 мм.
Проверка: TN = Td+TD 0,049 = 0,019 + 0,030
3.Задана посадка Æ105F7/h7.
Посадка c зазором.
Предельные отклонения отверстия Æ53H7: верхнее ES=+30мкм; нижнее EI=0.
Предельные отклонения вала Æ53k5: верхнее es=+15 мкм; нижнее ei=+2 мкм.
Предельные размеры отверстия и вала:
Dmax = D + ES = 53 + 0,030 = 53,030 мм;
Dmin = D + EI = 53 + 0 = 53 мм;
dmax = d + es = 53 + 0,015 = 53,015 мм;
dmin = d + ei = 53 + 0,002 = 53,002 мм;
Допуски размеров отверстия и вала:
TD = IT7 = 30 мкм;
Td = IT5 = 13 мкм;
Параметры посадки (переходная).
Smax = Dmax - dmin = 53,030 - 53,002 = 0,028 мм;
Nmax = dmax - Dmin = 53,015 - 53 = 0,015 мм;
Smin = -Nmax = -0,015 мм;
Nmin = -Smax = -0,028 мм;
TS(N) = Smax + Nmax = 0,028 - 0,015 = 0,043 мм.
Проверка: TS(N) = Td+TD 0,043 = 0,013 + 0,030
4.Задана посадка Æ21H8/h7.
Посадка с зазором.
Предельные отклонения отверстия Æ21H8: верхнее ES=+33мкм; нижнее EI=0.
Предельные отклонения вала Æ21h7: верхнее es=0 мкм; нижнее ei=-21 мкм.
Предельные размеры отверстия и вала:
Dmax = D + ES = 21 + 0,033 = 21,033 мм;
Dmin = D + EI = 21 + 0 = 21 мм;
dmax = d + es = 21 + 0 = 21 мм;
dmin = d + ei = 21 + (-0,021) = 20,979 мм;
Допуски размеров отверстия и вала:
TD = IT8 = 33 мкм;
Td = IT7 = 21 мкм;
Параметры посадки (c зазором).
Smax = Dmax - dmin = 21,033 - 20,979 = 0,054 мм;
Smin = Dmin - dmax = 21 - 21 = 0;
TS = Smax - Smin = 0,054 - 0 = 0,054 мм.
Проверка: TS = Td+TD 0,054 = 0,021 + 0,033
Полученные данные для всех посадок заносим в таблицу 1.1.
Таблица 1.1 Типы и параметры посадок
Обозначение Посадки | Предельные размеры | Предельные размеры | Тип посадки | Допуск посадки | ||||||
Отверстия | Вала | зазор | натяг | |||||||
Æ19H9/c8 | 19,052 | 19 | 18,890 | 18,857 | 0,195 | 0,110 | - | - | зазор | 0,085 |
Æ34H7/s7 | 34,025 | 34 | 34,068 | 34,043 | - | - | 0,068 | 0,018 | натяг | 0,050 |
Æ53H7/k5 | 53,030 | 53 | 53,015 | 53,002 | 0,028 | -0,015 | 0,015 | -0,028 | переходная | 0,043 |
Æ21H8/h7 | 21,033 | 21 | 21 | 20,979 | 0,054 | 0 | - | - | зазор | 0,054 |
Нормирование точности размеров в машиностроении
Основные понятия о размерах, отклонениях и посадках
Создатели механизмов и машин, исходя из назначений деталей, на основе расчетов различного характера и результатов экспериментальных исследований, определяют геометрические параметры элементов деталей. Степень возможных, с точки зрения работоспособности каждой детали, отклонений ее геометрических параметров от заданных определяет конструктор. Естественно, что одни элементы деталей требуется выполнить более точно, чем другие в соответствии с их назначением.
В то же время известно, что абсолютно точно изготовить геометрические элементы детали невозможно вследствие целого ряда причин, свойственных любому технологическому процессу.
1. Размер – числовое значение линейной величины (диаметра, длины ит.п.) в выбранных единицах измерения. Другими словами, размер элемента детали – расстояние между двумя характерными точками этого элемента.
2. Размер элемента, установленный измерением с допускаемой погрешностью, называют действительным размером . Действительный размер выявляется экспериментальным путем (измерением) с допустимой погрешностью, которая определена какими–либо нормативными документами. Действительный размер находят в случаях, когда требуется определить соответствие размеров элементов детали установленным требованиям. Когда же такие требования не установлены и измерения проводят не с целью приемки продукции, то возможно использование термина измеренный размер, т. е. размер, полученный в результате измерений.
3. Истинный размер – размер, полученный в результате изготовления и значение которого нам неизвестно, хотя оно и существует. К значению истинного размера мы приближаемся по мере повышения точности измерений, поэтому понятие «истинный размер» часто заменяют понятием «действительный размер», который близок к истинному в условиях поставленной цели.
4. Номинальный размер – размер, относительно которого определяются отклонения. Для деталей, составляющих соединение, номинальный размер является общим для отверстия и вала. Номинальный размер определяется конструктором в результате расчетов на прочность, жесткость, при определении габаритов и т.д. или с учетом конструктивных и технологических соображений. Этот размер указывают на чертеже.
5. Учитывая погрешность обработки, конструктор указывает не один размер, а два предельно допустимых размера элемента, между которыми должен находиться (или быть им равным) действительный размер. Эти два размера называют наибольшим предельным размером (наибольший допустимый размер элемента детали) и наименьшим предельным размером (наименьший допустимый размер элемента детали). Разность между наибольшим и наименьшим предельными размерами называется допуском на обработку или допуском, обозначаемым Т d:
;
.
Допуск – это существенно положительная величина, он не может быть отрицательным. Это интервал значений размеров, между которыми должен находиться размер годного элемента детали.
;
.
Следовательно, допуск показывает как бы разрешенную погрешность обработки, заранее предусмотренную и отраженную в чертеже детали. В этом случае годными и взаимозаменяемыми будут такие детали, у которых размер, получившийся после обработки, находится в пределах допуска.
Чем меньше допуск, тем точнее должен быть изготовлен нормируемый элемент детали и тем труднее, сложнее и потому дороже его изготовление. Чем больше допуск, тем грубее требования к элементу детали и тем проще и дешевле его изготовление.
Таким образом, устанавливать (нормировать) точность размера – это значит указать два его возможных (допускаемых) предельных значения.
Правильность получения размеров при обработке проверяется их измерением.
Измерить размер – значит сравнить его значение с величиной, принятой за единицу (для линейных размеров единицей измерения является метр).
Все инструменты и приборы, применяемые для измерений, имеют общее название – измерительные средства. При измерениях возможны погрешности, и поэтому абсолютно точно определить размер детали невозможно.
Погрешностью измерения называется отклонение результата измерения от истинного значения измеряемой вёличины. Погрешность измерения могут вызвать: погрешности, вносимые установочными мерами и образцами; неточности СИ или изношенность его отдельных частей; температурные влияния; ошибки, связанные с опытом и навыками человека, который проводит измерение и т.д.
Федеральное государственное бюджетное образовательное учреждение
высшего профессионального образования
«Алтайский государственный технический университет
имени И.И. Ползунова»
В.А. Вагнер,
В.П. Звездаков,
В.В. Собачкин
НОРМИРОВАНИЕ ТОЧНОСТИ В МАШИНОСТРОЕНИИ
Учебное пособие
по дисциплине "Метрология, стандартизация и сертификация"
Допущено Учебно-методическим объединением вузов по университетскому политехническому образованию в качестве пособия для студентов высших учебных заведений, обучающихся по машиностроительным направлениям подготовки
Из-во АлтГТУ
Барнаул – 2011
Вагнер В.А. Нормирование точности в машиностроении. Учебное пособие по дисциплине «Метрология, стандартизация и сертификация»/ В.А. Вагнер, В.П. Звездаков, В.В. Собачкин. - Барнаул: Изд-во Алт.гос.техн. ун-т им. И.И.Ползунова.- 2011, 84 с.: ил.
В учебном пособии представлены сведения о нормировании точности в машиностроении при разработке деталей и узлов машин.
Целью работы является изучение теоретических вопросов по разделу «взаимозаменяемость» дисциплины «Метрология, стандартизация и сертификация», развитие навыков самостоятельной деятельности студентов по практическому закреплению рассмотренных в теоретической части курса задач, а также работы со справочной литературой и стандартами.
Учебное пособие предназначено для студентов высших учебных заведений всех специальностей, обучающихся по машиностроительным направлениям подготовки очной, очно-заочной и заочной форм обучения , изучающих курс «Метрология, стандартизация и сертификация».
Рецензенты:
Профессор кафедры «Метрология и взаимозаменяемость» МГТУ им. Н.Э.Баумана,
д.т.н. Пронякин В.И.
Профессор кафедры «Детали машин» Уральского федерального университета,
д.т.н. Чечулин Ю.Б.
1 Определение номинальных размеров деталей сборочной единицы. . . . . . . . . . . . . . . . . . . . . . . . . . . . . . .
2 Общие сведения о размерах, допусках, посадках и предельных отклонениях. . . . . . . . . . . . . . . . . . . . . .
3 Допуски и посадки в «Единой системе допусков и посадок» . . . . . . . . . . . . . . . . . . . . . . . . . . . . . . . . . . . .
4 Выбор посадок при проектировании конструкций. . . . . . . . . . . . . . . . . . . . . . . . . . . . . . . . . . . . . . . . . . . . .
4.1 Посадки с зазором. . . . . . . . . . . . . . . . . . . . . . . . . . . . . . . . . . . . . . . . . . . . . . . . . . . . . . . . . . . . . . . . . . . . . .
4.2 Переходные посадки. . . . . . . . . . . . . . . . . . . . . . . . . . . . . . . . . . . . . . . . . . . . . . . . . . . . . . . . . . . . . . . . . . . .
4.3 Посадки с натягом. . . . . . . . . . . . . . . . . . . . . . . . . . . . . . . . . . . . . . . . . . . . . . . . . . . . . . . . . . . . . . . . . . . . . .
5 Расчет посадки с натягом. . . . . . . . . . . . . . . . . . . . . . . . . . . . . . . . . . . . . . . . . . . . . . . . . . . . . . . . . . . . . . . . .
6 Допуски и посадки шпоночных соединений. . . . . . . . . . . . . . . . . . . . . . . . . . . . . . . . . . . . . . . . . . . . . . . . . .
6.1 Соединения с призматическими шпонками. . . . . . . . . . . . . . . . . . . . . . . . . . . . . . . . . . . . . . . . . . . . . . . . .
6.2 Соединения с сегментными шпонками. . . . . . . . . . . . . . . . . . . . . . . . . . . . . . . . . . . . . . . . . . . . . . . . . . . . .
7 Допуски и посадки зубчатых (шлицевых) соединений. . . . . . . . . . . . . . . . . . . . . . . . . . . . . . . . . . . . . . . . .
7.1 Зубчатое соединение с прямобочными шлицами. . . . . . . . . . . . . . . . . . . . . . . . . . . . . . . . . . . . . . . . . . . .
7.2 Зубчатое соединение с эвольвентными шлицами. . . . . . . . . . . . . . . . . . . . . . . . . . . . . . . . . . . . . . . . . . . . .
8 Посадки подшипников качения. . . . . . . . . . . . . . . . . . . . . . . . . . . . . . . . . . . . . . . . . . . . . . . . . . . . . . . . . . . . .
9 Размерные цепи. . . . . . . . . . . . . . . . . . . . . . . . . . . . . . . . . . . . . . . . . . . . . . . . . . . . . . . . . . . . . . . . . . . . . . . . .
10 Нормирование точности формы и расположения поверхностей типовых деталей машин, определение требуемой шероховатости поверхности. . . . . . . . . . . . . . . . . . . . . . . . . . . . . . . . . . . . . . . . . . . . . . . .
10.1 Допуски формы и взаимного расположения поверхностей. . . . . . . . . . . . . . . . . . . . . . . . . . . . . . . . . . . .
10.2 Шероховатость поверхностей деталей. . . . . . . . . . . . . . . . . . . . . . . . . . . . . . . . . . . . . . . . . . . . . . . . . . . .
11 Допуски расположения осей отверстий для крепежных деталей. . . . . . . . . . . . . . . . . . . . . . . . . . . . . . . .
12 Обоснование технических требований на чертеж сборочной единицы. . . . . . . . . . . . . . . . . . . . . . . . . . .
12.1 Общие положения. . . . . . . . . . . . . . . . . . . . . . . . . . . . . . . . . . . . . . . . . . . . . . . . . . . . . . . . . . . . . . . . . . . . .
12.2 Определение величин технических требований. . . . . . . . . . . . . . . . . . . . . . . . . . . . . . . . . . . . . . . . . . . .
12.2.1 Определение величин боковых зазоров в зацеплении. . . . . . . . . . . . . . . . . . . . . . . . . . . . . . . . . . . . . .
12.2.2 Определение полноты контакта сопряженных боковых поверхностей зубьев. . . . . . . . . . . . . . . . . .
13 Указания по составлению технических требований и оформлению рабочего чертежа зубчатого колеса. . . . . . . . . . . . . . . . . . . . . . . . . . . . . . . . . . . . . . . . . . . . . . . . . . . . . . . . . . . . . . . . . . . . . . . . . . . . . . . . . . . .
13.2 Рекомендации по составлению технических требований для цилиндрического и конического зубчатых колес. . . . . . . . . . . . . . . . . . . . . . . . . . . . . . . . . . . . . . . . . . . . . . . . . . . . . . . . . . . . . . . . . . . . . . . . . .
14 Указания по составлению технических требований и оформлению рабочего чертежа вала редуктора
15 Рекомендации по составлению технических требований, разработке и оформлению чертежа крышки подшипника и стакана. . . . . . . . . . . . . . . . . . . . . . . . . . . . . . . . . . . . . . . . . . . . . . . . . . . . . . . . . . . . . . . . . . .
Список литературы. . . . . . . . . . . . . . . . . . . . . . . . . . . . . . . . . . . . . . . . . . . . . . . . . . . . . . . . . . . . . . . . . . . . .
Приложение А. . . . . . . . . . . . . . . . . . . . . . . . . . . . . . . . . . . . . . . . . . . . . . . . . . . . . . . . . . . . . . . . . . . . . . . . .
Приложение Б. . . . . . . . . . . . . . . . . . . . . . . . . . . . . . . . . . . . . . . . . . . . . . . . . . . . . . . . . . . . . . . . . . . . . . . . .
4
ВВЕДЕНИЕ
В соответствии с образовательным стандартом для студентов технических специальностей машиностроительного направления, изучающих дисциплину «Метрология, стандартизация и сертификация» в разделе взаимозаменяемость, предусмотрена курсовая работа или расчетное задание.
Целью курсовой работы (расчетного задания) является закрепление знаний, полученных из теоретического курса и приобретение навыков их практического применения , поэтому в данной работе приводятся как сведения теоретического характера по основным разделам дисциплины, так и примеры решения типовых задач курса. В приложении к работе дается справочный материал, необходимый для решения задач.
Выполнение курсовой работы проводится по индивидуальным заданиям, выданным преподавателем .
Требования к содержанию и оформлению курсовой работы (расчетного задания) изложены в методических рекомендациях .
1 Определение номинальных размеров деталей сборочной единицы
Размеры деталей, составляющих сборочную единицу, зависят от задания и варианта на курсовую работу. Для определения их номинальных значений необходимо вычислить масштабный коэффициент. Рассчитывается он следующим образом. На чертеже задания на курсовую работу измеряется размер, соответствующий диаметру вала под подшипником качения (d 3 измеренный). Заданный по заданию размер (d 3 заданный) делят на этот измеренный размер и получают масштабный коэффициент μ
Измеряя все другие размеры деталей сборочной единицы и умножая их на этот масштабный коэффициент, определяют расчётные размеры.
Для сокращения числа типоразмеров заготовок и деталей, режущего и измерительного инструмента значения номинальных размеров , полученные расчетом, необходимо округлить до значений, указанных в ГОСТ 6636-69 «Нормальные линейные размеры» (таблица А.1). После этого округленные значения номинальных размеров следует занести в таблицу 1.1. Размеры, связанные с подшипником качения, при этом, следует принять по стандарту на это изделие, независимо от величины расчётного размера. Для этого следует расшифровать условное обозначение заданного подшипника качения, определив его серию, тип и конструктивные особенности, а затем по ГОСТ 520-2002 или справочникам выписать все параметры подшипника качения, необходимые для дальнейших расчетов (присоединительный диаметр наружного кольца, ширину колец, динамическую грузоподъемность подшипника).
Затем назначают размеры, связанные с подшипником качения. Такими размерами являются размер d 1 (посадочный диаметр сквозной крышки подшипника), d 2 (диаметр отверстия в корпусе для установки подшипника), d 4 (внутренний диаметр дистанционной втулки), d 5 (посадочный диаметр глухой крышки подшипника). Обозначения по .
Например, если по заданию известно , что d 3 = 30 мм, тип подшипника 7300, то это значит, что типоразмер подшипника 7306 (d 3 /5=30/5 = 6), подшипник роликовый конический и наружный его диаметр D = 72 мм . В соответствии с этим размеры d 1 = d 2 = d 5 = 72 мм, и d 4 = d 3 = 30 мм.
При заполнении таблицы 1.1 следует обращать внимание на размеры нормированных и стандартных деталей, которые необходимо также принимать согласно соответствующим нормативным документам. К таким деталям относятся уплотнения подшипниковых узлов, шпонки, гайки круглые шлицевые, крышки подшипников сквозные и глухие, стаканы подшипников .
По полученным размерам вычерчивают в соответствующем масштабе сборочную единицу.
2 Общие сведения о размерах, допусках, посадках и предельных отклонениях
Размер – числовое значение линейной величины (диаметр, длина и т. п.) в выбранных единицах измерения. На чертежах все линейные размеры указываются в миллиметрах.
Действительный размер – размер элемента, установленный измерением с допускаемой погрешностью.
Предельные размеры – два предельно допустимых размера, между которыми должны находиться или которым может быть равен действительный размер годной детали. Больший из них называется наибольшим предельным размером, а меньший – наименьшим предельным размером. Обозначаются D max и D min для отверстия и d max и d min для вала.
Номинальный размер – размер, относительно которого определяются отклонения. Размер, который указан на чертеже является номинальным. Номинальный размер определяется конструктором в результате расчетов на прочность и жесткость или с учетом конструктивных и технологических особенностей. Для деталей, образующих посадочное соединение , номинальный размер является общим.
В
Таблица 1.1 - Размеры сборочной единицы
№ п/п
Обозначение размера
Размер измеренный, мм
Размер расчетный, мм
Размер по ГОСТ 6636-69
1
. . .
. . .
. . .
. . .
2
. . .
. . .
. . .
. . .
n
. . .
. . .
. . .
. . .
ерхнее отклонение ES, es – алгебраическая разность между наибольшим предельным и соответствующим номинальным размерами.
ES = D max – D - для отверстия, (2.1)
es = d max – d - для вала. (2.2)
Нижнее отклонение EI, ei – алгебраическая разность между наименьшим предельным и соответствующим номинальным размерами.
EI = D min – D - для отверстия, (2.3)
ei = d min – d - для вала. (2.4)
Действительное отклонение – алгебраическая разность между действительным и номинальным размерами.
Допуск Т – разность между наибольшим и наименьшим предельными размерами или алгебраическая разность между верхним и нижним отклонениями.
Т D = D max – D min = ES - EI - для отверстий, (2.5)
Т d = d max – d min = es - ei - для вала. (2.6)
Допуск всегда положителен. Он определяет допускаемое поле рассеивания действительных размеров годных деталей в партии, то есть заданную точность изготовления.
Поле допуска – поле, ограниченное наибольшим и наименьшим предельными размерами и определяемое величиной допуска Т и его положением относительно номинального размера. При графическом изображении поле допуска заключено между двумя линиями, соответствующими верхнему и нижнему отклонениям относительно нулевой линии (рисунок 2.1).
Основное отклонение – одно из двух отклонений (верхнее или нижнее), определяющее положение поля допуска относительно нулевой линии. Основным является отклонение ближайшее к нулевой линии. Второе отклонение определяется через допуск.
Нулевая линия – линия, соответствующая номинальному размеру, от которой откладывают отклонения размеров при графическом изображении допусков и посадок.
Вал – термин, условно применяемый для обозначения наружных (охватываемых) элементов деталей, включая и нецилиндрические элементы.
Отверстие – термин, условно применяемый для обозначения внутренних (охватывающих) элементов деталей, включая и нецилиндрические элементы.
Допуск отверстия обозначается T D , а вала T d . Помимо охватывающих и охватываемых элементов, называемых отверстиями и валами, в деталях имеются элементы, которые нельзя отнести ни к отверстию, ни к валу (уступы, расстояния между осями отверстий и т. д.).
Посадка - характер соединения двух деталей , определяемый разностью их размеров до сборки. Посадка характеризует свободу относительного перемещения соединяемых деталей или степень сопротивления их взаимному смещению. По характеру соединения различают три группы посадок: посадки с зазором, посадки с натягом и переходные посадки.
Зазор S – разность размеров отверстия и вала, если размер отверстия больше размера вала. Зазор обеспечивает возможность относительного перемещения собранных деталей. Наибольший, наименьший и средний зазоры определяются по формулам:
S max = D max – d min = ES - ei; (2.7)
S
Рисунок 2.1. а – сопряжение
б – схема расположения полей допусков вала и отверстия
min = D min – d max = EI - es (2.8)
Государственное образовательное учреждение высшего профессионального образования
«ТЮМЕНСКИЙ ГОСУДАРСТВЕННЫЙ НЕФТЕГАЗОВЫЙ УНИВЕРСИТЕТ»
ТЕХНОЛОГИЧЕСКИЙ ИНСТИТУТ
КАФЕДРА«ТЕХНОЛОГИЯ МАШИНОСТРОЕНИЯ»
Контрольная работа
Нормирование точности, допуски и посадки
Вариант№ 16
Тюмень2010
Задача№1
Дано: Ш77 ,для номинального размера построить расположение полей допусков трех видов соединений.
Определить и указать на схеме значение предельных отклонений размеров, зазоров и натягов.Определить:допуски, посадки и в каких пределах может находиться действительный размер годной детали.
1). Ш77Н8 ES=+0,046 мм
Ш77 d7 es= -0,100 мм
Предельные размеры:
Посадка с зазором
для вала от Ш76,900до Ш76,870мм
2). Ш77Н8 ES=+0,046 мм
Ш77 n7 es= +0,050 мм
Предельные размеры:
Посадка переходная
Зазор и натяг
Действительные размеры годной детали:
для отверстия от Ш77,046до Ш77,0мм
для вала от Ш77,020до Ш77,050мм
3). Ш77Н8 ES=+0,046 мм
Ш77 s7 es= +0,089 мм
Предельные размеры:
Посадка с натягом
Действительные размеры годной детали:
для отверстия от Ш77,046до Ш77,0мм
для вала от Ш77,059до Ш77,089мм
Задача№2
Дано: вид шпоночного соединения–С (свободное),диаметр вала Ш77
1). Выбираем размеры призматической шпонки:
22 х 14, интервал длины от 63 до250 мм
9мм глубина паза на валу
5,4мм глубина паза во втулке
2). Выбираем поля допусков для шпонки и для пазов зависимости от характера шпоночного соединения:
для шпонки- 22h9 х 14h11 х 100h14
ширина шпоночного паза на валу- 22H9
ширина паза во втулке- 22D10
3). Эскиз шпоночного соединения
4). Схема расположения полей допусков шпоночного соединения
5). Условное обозначение шпонки:
2-22h9 х 14h11 х100h14 ГОСТ23360-78
Задача№3
Дано:шлицевое соединение6х11х14, закалена втулка.
1). Принимаем способ центрирования шлицевого соединения-центрирование по внутреннему диаметру втулкиd.
2). Находим из таблицы ширину зуба- b= 3 мм.
Для размераd = 11
Для размераb= 3
4). Эскиз шлицевого соединения:
5). Схема расположения полей допусков шлицевого соединения
6). Условное обозначение шлицевого соединения
d – 6 x 11 x 14 x 3
Похожие рефераты:
Взаимозаменяемость, стандартизация и технические измерения
Допуски и посадки цилиндрических соединений.
Нормирование точности в машиностроении
Допуски и посадки гладких цилиндрических сопряжений и калибры для контроля их соединений. Выбор посадок подшипника качения. Понятие шероховатости, отклонения формы и расположения поверхностей. Прямобочное и эвольвентное шлицевое и шпоночное соединение.
Метрология расчет типовых соединений
Выбор посадки для соединения с зазором в зависимости от диаметра и скорости вращения. Расчет посадки для втулки, запрессованной в корпус. Расчет резьбового соединения, определение исполнительных размеров калибров. Выбор посадок подшипника качения.
Нормирование основных деталей и узлов
Особенности расчёта и подбора посадок. Нормирование точности болтового и шпилечного соединения, точности диаметрального размера втулки и вала при нормальной температуре. Определение посадок под подшипники, шпоночных соединений. Расчёт размерной цепи.
Расчет элементов механизма подачи металлорежущего станка
Расчёт гладких цилиндрических соединений механизма подачи металлорежущего станка. Методика определения калибров для контроля деталей соединения. Подбор и расчет подшипников качения, резьбовых и шпоночных соединений. Составление схемы размерной цепи.
Расчеты средств технических измерений и контроля
Определение элементов сопряжения, условное обозначение посадок и квалитетов на чертежах и расчет калибров. Выбор посадок с зазором для подшипников жидкостного трения. Расчет допусков и посадок шпоночных соединений. Выбор деталей под подшипник качения.
Взаимозаменяемость, допуски и посадки
Особенности выбора допуска и посадок для гладких цилиндрических соединений, выбор полей допусков для деталей, сопрягаемых с подшипниками качения. Выбор допусков и посадок шпоночных, шлицевых соединений. Расчет допусков размеров заданной размерной цепи.
Определение параметров основных типовых соединений
Методика расчета параметров сопряжений: гладких цилиндрических, резьбовых, шпоночных и шлицевых соединений. Построение схем расположения полей допусков деталей и их сопряжений в соответствии с требованиями Единой системы конструкторской документации.
Гладкое цилиндрическое соединение. Определение элементов соединений, подвергаемых селективной сборке
Основные параметры гладкого цилиндрического соединения. Групповые допуски вала и отверстия. Составление карты сортировщика. Расчет и выбор полей допусков для деталей, сопрягаемых с подшипниками качения. Допуски и посадки шпоночных и шлицевых соединений.
Расчеты деталей машин
Выбор посадок гладких цилиндрических соединений, для шпоночного соединения, для шлицевых соединений с прямым профилем зуба. Расчет размеров деталей подшипникового узла, предельных и средних натягов и зазоров. Проверка наличия радиального зазора.
Метрология, взаимозаменяемость, стандартизация, сертификация
Обоснование, назначение и анализ посадок для типовых соединений деталей машин заданной сборочной единицы, выполнение их расчёта. Вычисление исполнительных размеров калибра-скобы и калибра-пробки. Исполнение рабочих чертежей вала и зубчатого колеса.
Особенности выбора посадок для гладких цилиндрических и шпоночных соединений редуктора, применяемого для понижения оборотов двигателя и повышения крутящего момента. Методика расчета размерной цепи методом полной взаимозаменяемости и вероятностным методом.
Сопряжения с зазором и натягом
Характеристики посадки с зазором и натягом, верхнее и нижнее отклонения, наибольший и наименьший предельные размеры, допуск зазора и натяга. Расположения полей допусков для сопряжений. Обозначение предельных отклонений на сборочном и рабочем чертежах.
Выбор и расчет посадок типовых соединений
Расчёт гладкого цилиндрического соединения 2 – шестерня – вал. Вычисление калибров для контроля гладких цилиндрических соединений. Выбор нормальной геометрической точности. Определение подшипникового соединения, посадок шпоночного и шлицевого соединения.
Анализ качества изделия машиностроения
Расчет и выбор посадки с натягом для соединения зубчатого колеса с валом. Анализ полученной посадки и построение схемы расположения полей допусков. Обозначение посадки соединения и полей допусков сопрягаемых деталей, поправка к расчетному натягу.
Расчет, выбор и обоснование посадок соединений
Стандартизация и унификация деталей и сборочных единиц: ускорение и удешевление конструирования, изготовления, эксплуатации и ремонта машин. Выбор посадок для гладких цилиндрических сопряжений, шпоночных и шлицевых соединений, подшипников качения.
Расчет, выбор и обоснование посадок соединений редуктора
Выбор посадок для гладких цилиндрических соединений, расположенных на тихоходном валу, обоснование выбора системы и квалитетов. Расчет и выбор посадок с натягом. Решение линейных размерных цепей методом полной взаимозаменяемости и вероятностным методом.
Составление схем расположения полей допусков стандартных сопряжений. Расчёт соединения подшипника качения с валом и корпусом. Расчет размерных цепей
Схемы расположения полей допусков стандартных сопряжений. Соединение подшипника качения с валом и корпусом. Расчет размерных цепей. Решение задачи методом максимума - минимума. Решение задачи теоретико-вероятностным методом (способ равных квалитетов).
Посадки и допуски
Расчеты калибров и контркалибров посадок колец подшипника, контроль размеров и расчет на вероятность зазоров. Параметры цилиндрической зубчатой передачи и расчет размерной цепи заданого замыкающего звена. Размеры и предельные отклонения соединений.
Допуски и посадки
Расшифровка посадки по буквенному написанию или другим параметрам. Обозначение системы, в которой обозначены отверстие и вал. Буквенное обозначение размеров вала и отверстия. Расчет предельного размера вала и отверстия S(N) max и min допуск посадки.
Трудовые отношения
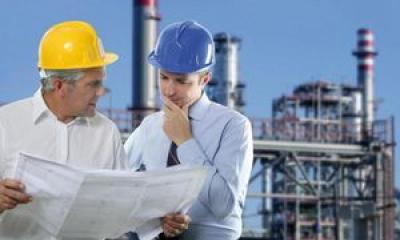
Должностная инструкция главного инженера, должностные обязанности главного инженера, образец должностной инструкции главного инженера Должностная инструкция главного инженера рэс
Открытие бизнеса
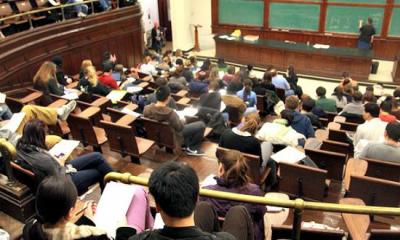
Где можно и где нельзя работать после туберкулеза Где можно работать после
Форекс
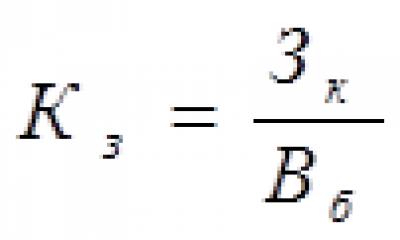